閃きプラットフォーム開発レシピギャラリー
Recipe 3 ボルトパーツフィーダー
開発のポイント
- 1 ボルトはすべて頭部を上向きに整えた状態で供給
- 2 中央レーンの両側からボルトをかき上げることで、高効率でボルトを取り出し
- 3 不適切な姿勢でレーンに乗った余剰ボルトのはらい落しに、除去用のゴム板を設置
工業製品の組み立て作業に欠かせない存在であるねじやボルト。大きさやサイズも幅広く、扱う量も膨大であることから、これらはいまだに箱に盛られた状態で供給されて、作業者が手で拾いにいくという工程が多いのが実情です。また市販のボルトフィーダーはボウル形状の高額な製品が多く、スペース効率の低さやコスト面でのハードルが導入のネックになっていました。このレシピでは、ボルトの取り出しを中央のレーン(溝)に両サイドからボルトをかき上げて取り出す、という方式を採用しました。これによって装置全体がスリムで省スペース化されただけでなく、ボルトの頭をすべて上向きに整えて効率よく供給することが可能になりました。機材費も抑え、市販品より大幅に低コスト化することができました。
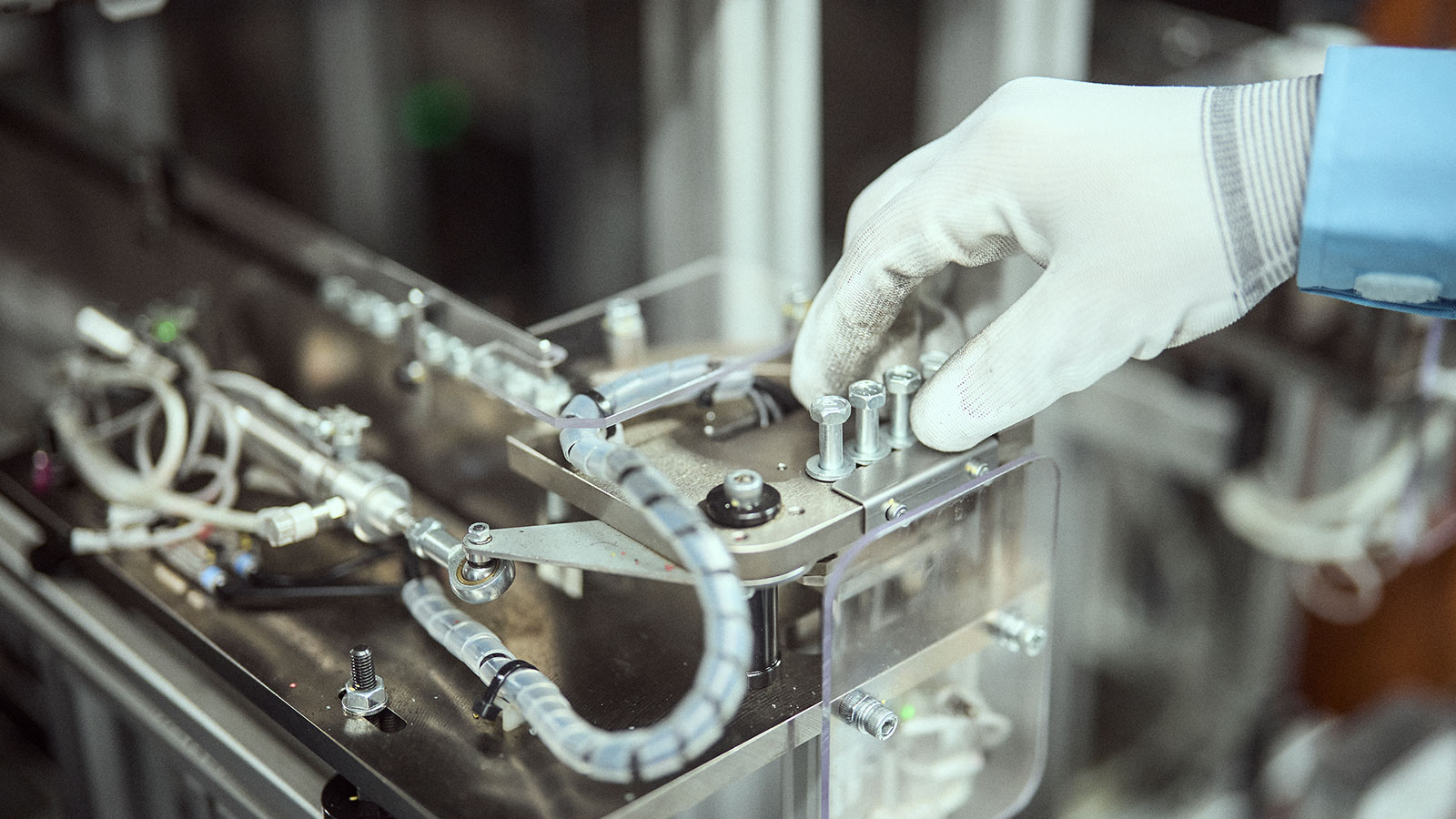
現場の声
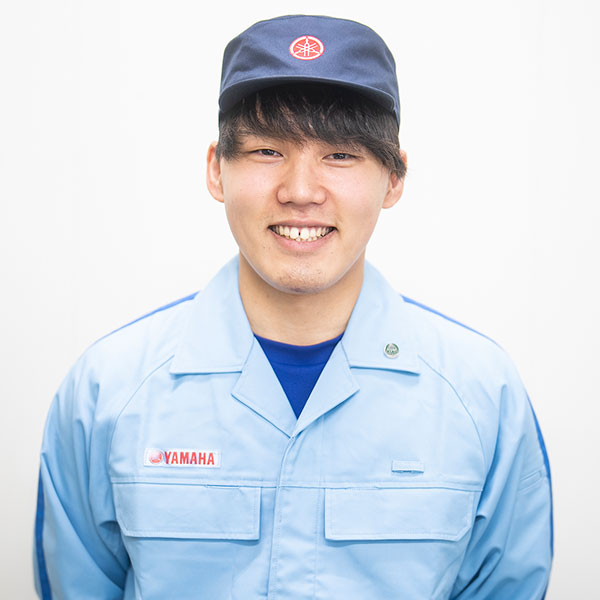
猪原 晃太さん
ヤマハ発動機株式会社
磐田南工場
磐田第3製造部生産4課第2工区
どこに導入しましたか?
63Pという船外機エンジンのシリンダーヘッドに、カムキャップという部品を取り付ける工程に導入しました。ここでは白・黒の2種類のボルトを使って仮締めして次の工程に流していますが、現在は2種類それぞれをボルトフィーダーが自働で定数供給するようになっています。
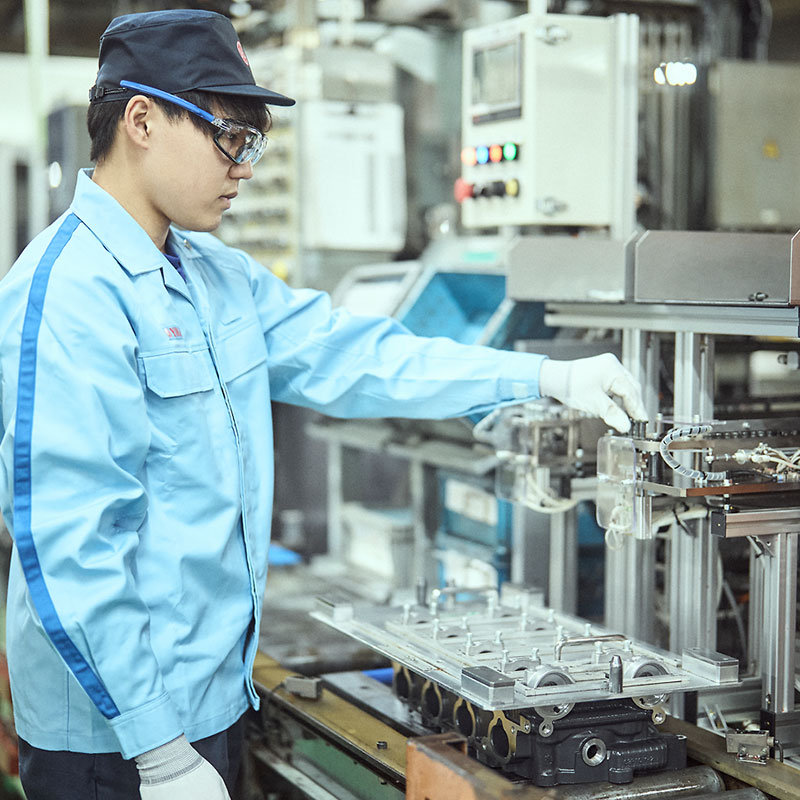
どんな課題がありましたか?
いま船外機市場が非常に好調で、需要がどんどん伸びています。そのため工場ではときに残業したり土曜・休日に出勤したりと、かなり高負荷で生産対応している状態なんですね。お客様のニーズに応えながら現場の負荷を軽減するためには、日々の生産効率を上げていくしかありません。そのためにも工程上のハンドタイム削減は早急に取り組まなければならない課題でした。
この設備を導入した工程では、2種類のボルトがそれぞれ箱に盛られた状態で作業者の前に並んでいて、そこに手を伸ばして取りにいく、というやり方で作業していました。またボルトがワークの中に落下しないよう「ボルトは手で1本ずつ拾う」というルールがあったので、それがさらにハンドタイムを長くする要因になっていたんですね。これを自働化することでハンドタイムを削減するとともに、作業者によって組みつけ時間にバラつきがあることも均一化できればいいな、と考えていました。

現場に最適化するためにどんな工夫をしましたか?
じつは別の現場にAGV(自動搬送機)の導入を検討していて、それを視察するためにFAチーム(*1)の開発品を展示しているショールームに行ったんです。そこにあったのが今回導入したボルトパーツフィーダーで、しかもそれが新品の遊休機だということがわかって、もう即決で導入を決めましたね。
それをうちの現場によりフィットした装置にするためにいろいろ改造しています。現場の作業者の意見を吸い上げて、開発者の小曽さんも立ち会っていろんな案を出してもらいました。具体的には「作業工程にあわせて4本ずつ切り出すこと」「ボルトは上向きに揃え、頭部を手でつかみやすいよう少しせり上げて供給する」「作業スピードに合わせて最適な速度で送り出す」など、ほとんどの要求を実現してもらっています。ほかにもシリンダーなど可動部にカバーを設置したりと、実際の設置場所にあわせた安全対策も提案していただきました。作業者が働きやすいように改善してくれたおかげで、安心して働くことができています。
*1:「テミル:ラボ」プロジェクトを主導的に進めているチームのこと
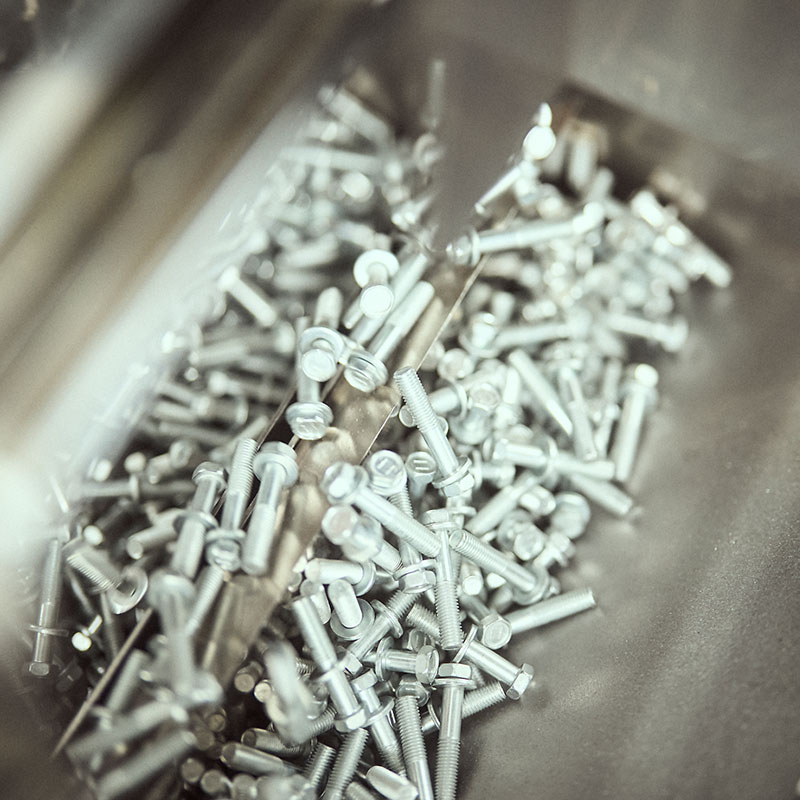
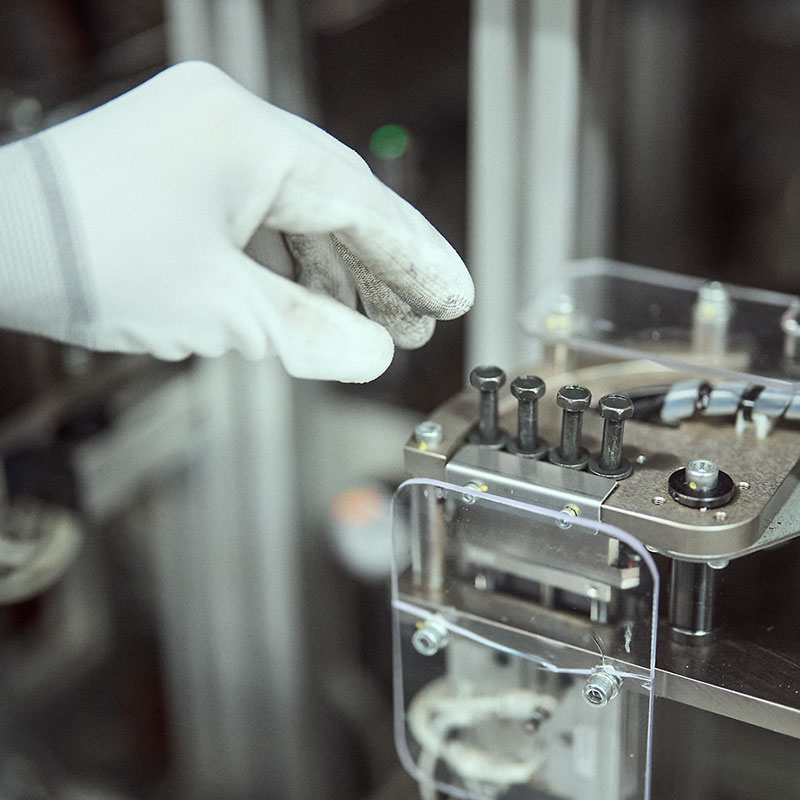
導入後の変化を教えてください!
まずは作業時間の短縮化です。手でひとつずつ取っていたものが4本セットで供給されて、一度に必要数をサッと取れるので、ミスも作業時間のバラつきもなくなりましたね。手伸ばしで箱からボルトを取りに行っていた時は、「位置決めピン打ち込み・カムキャップセット・ボルト仮締め」の一連の工程に138デシマル(*2)を要していました。ボルトパーツフィーダー導入後は108デシマルと、1作業につき23デシマルの短縮化を実現しました。1直あたり70台の生産なので、1日にその70回分の短縮です。1か月では960分と、まるまる2直分の作業時間が削減できたことになり、労働負荷の軽減にもつながりました。この装置は遊休機だったこともあってかなり低コストで導入できたんですけど、約半年ほどで回収を終えました。非常に高い投資対効果があったことは言うまでもありません。
でもメリットは導入した工程だけじゃなくて、じつは工場全体に及んでいます。この工場はもう完成して25年で設備もそれなりに古いので、メンテナンスが必要なのはわかっていました。しかしここ数年は高負荷生産が続いていたので、そのための時間がなかなか取れなかったんです。設備に不具合が発生するとラインが停止してしまい、結局は生産遅延で予定外の休日出勤、という悪循環に陥ってしまいます。それも見据えて、いまはシステム導入で短縮化できた時間をメンテナンスに充てて、万が一の事態を未然に防ぐための対策をとっています。
*2:10進法式の単位。工場の工程管理や作業分析、研究機関での計算などに用いられる

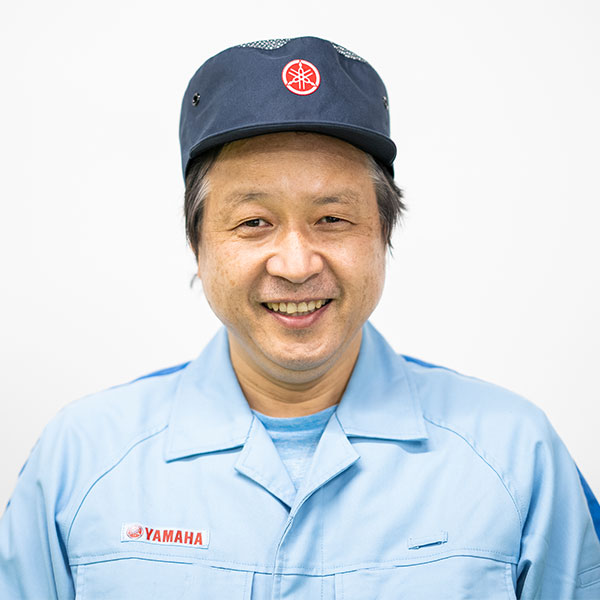
小曽 勉さん
ヤマハ発動機株式会社
FA技術開発グループ
開発者の声
ボルトフィーダーという装置自体は特にめずらしいものではなくて、昔から存在している装置です。でも主流であるボウル型フィーダーは大きくて場所を取るためライン内でスペースを確保する手間もかかるし、コストの高さもハードルになっていました。このシステムでは中央のレーン(溝)の両側からかき上げてボルトを取り上げることで、非常にスリムで省スペースなフィーダーにすることができました。パーツピッキング装置ではハケで余剰パーツをはらっていましたが、ここではゴム板がその役目を果たしてレーン上の余分なボルトを落としています。これによって頭が上向きのボルトだけがレーンに残るという仕組みです。ゴム板の硬度やスリットの間隔もボルト形状にあわせていろいろ試して最適化しています。
ボルトを振動で送り出す直進フィーダーでは、途中に設置したセンサーがかき上げ動作タイミングを調整しており、供給量が超過しないようコントロールしています。供給速度もその工程の作業のサイクルタイムにあわせて調整可能です。
この装置のように、既に市販されているありふれた製品でも、同じことを違う方法で実現することに開発のおもしろさがあるんですよね。既製品もいいんですけど、現場に合わせて工夫した製品があってもいい。求められる機能を現場にフィットしたかたちで提供するほうが、結果的に生産現場の自働化が早まるんじゃないか、という信念で日々開発にあたっています。
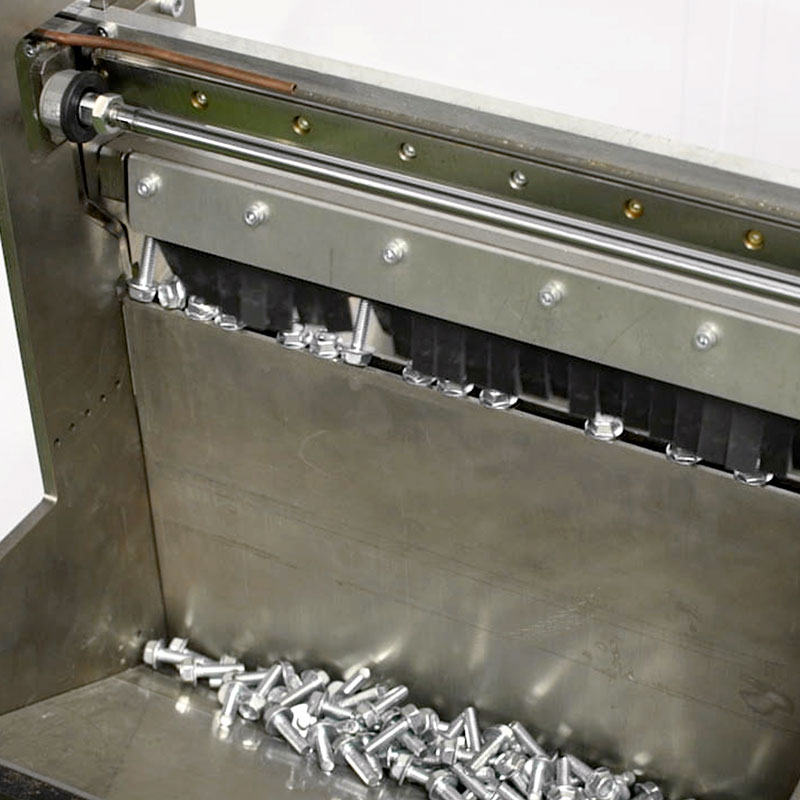
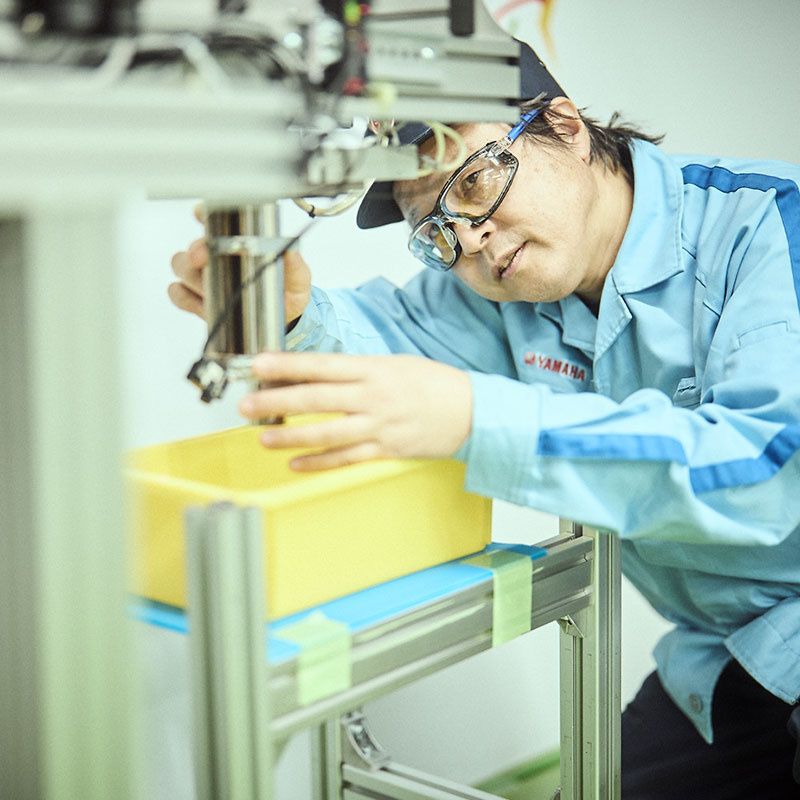