閃きプラットフォーム開発レシピギャラリー
Recipe 4 COW-el(廉価AGV)
開発のポイント
- 1 高機能化・高価格化が進むAGVを導入しやすいコストで実現
- 2 画像認識でルートを検出するので、ビニールテープを貼るだけでルート設営が可能
- 3 動力に電動車いすのユニットを使用し、屋外や段差のある路面も走行可能
製造現場では、材料・部品・工具・製造物などを必要な場所へ滞りなく運ぶ必要があります。これまでは台車やフォークリフトを使って人が運ぶのが一般的でしたが、業務を省人化する新たな運搬手段としてAGV(自動搬送機)のニーズが高まっています。しかし近年のAGVは多彩な機能が搭載され、高価格化する傾向にあります。またAGVの多くは磁気計測で走行するためコストの高い磁気テープを敷く必要があり、同時に段差やスロープが苦手という特徴にもつながっています。
COW-elはヤマハ発動機製電動車いすのドライブユニットを活用することで、屋外環境はもちろん、路面の段差も安定して運行できるタフな走行性能を実現したAGVです。カメラが画像認識で経路を検出するため、ビニールテープなど安価な材料でルートを設営できるだけでなく、変更も容易です。汎用品を活用することで、機材費を安く抑えることができています。
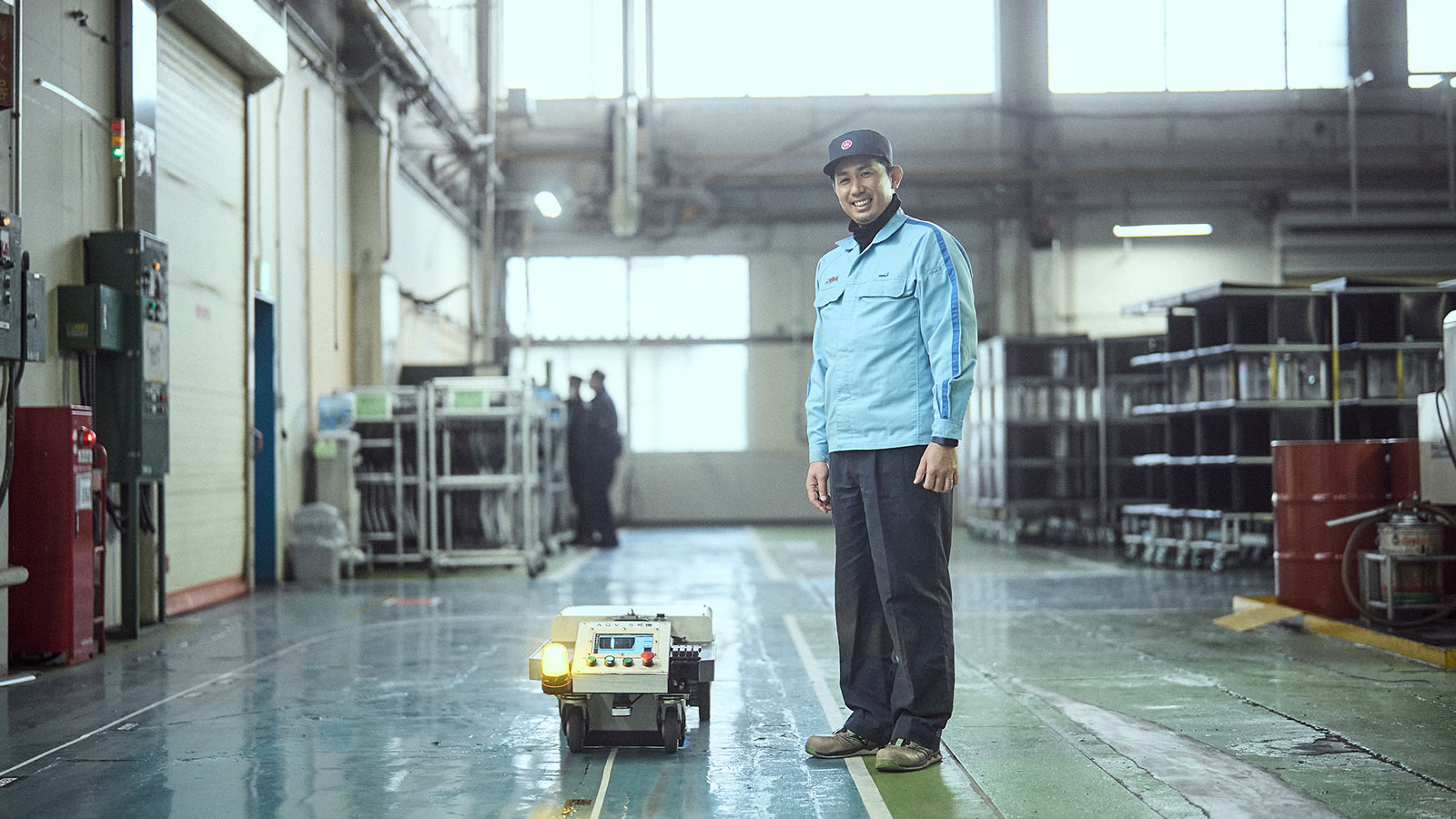
現場の声
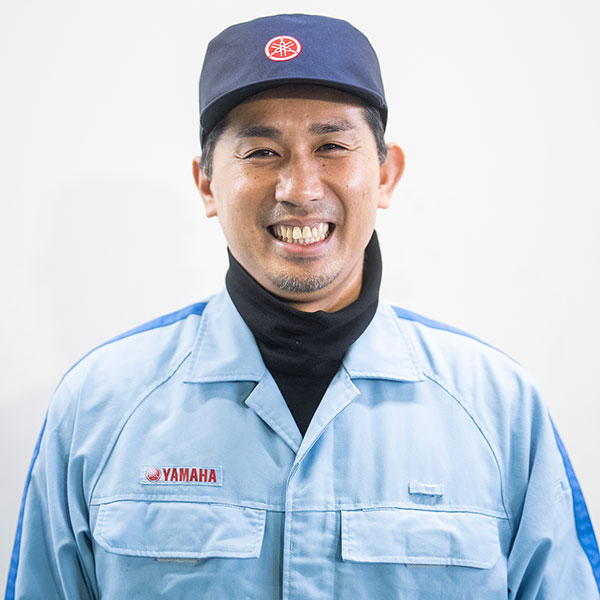
平野 敬二さん
ヤマハ発動機株式会社
PF車体技術部合理化グループ
合理化係
どこに導入しましたか?
オートバイのタンクやフレーム溶接を行う本社9号館から、塗装・組み立てを行う7号館に完成したタンクを運ぶ手段としてAGVを検討していました。しかし建屋の間は屋外なので、雨天でも走行できるものはないかとFAチーム(*1)に相談したところ、COW-elを導入することになったんです。現在1日1台当たり125回ほど往復しています。
*1:「テミル:ラボ」プロジェクトを主導的に進めているチームのこと
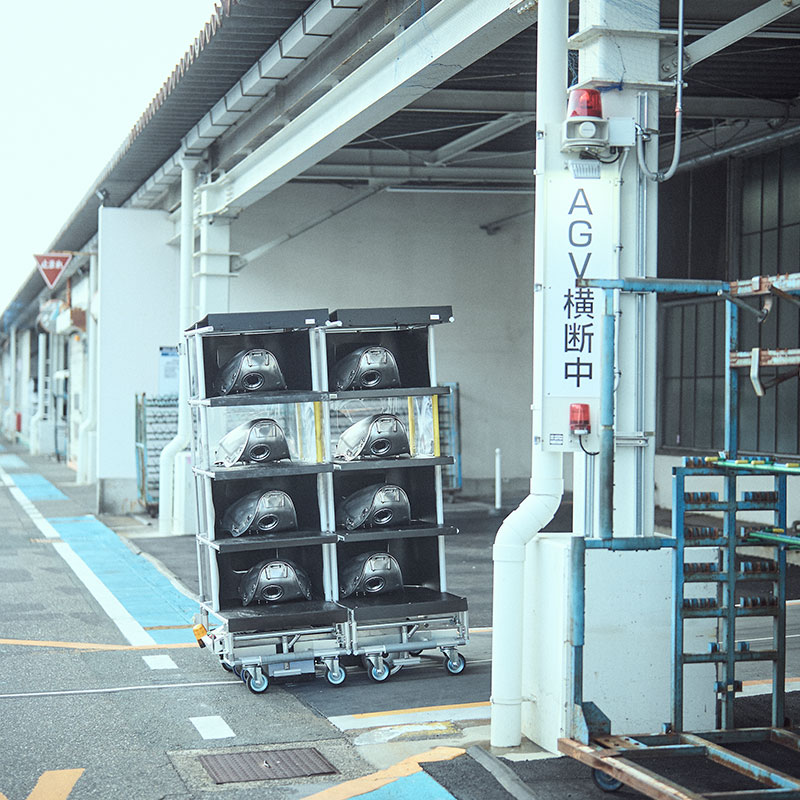
どんな課題がありましたか?
以前のタンク職場は、もっと離れた14号館という場所にあって、7号館の塗装職場までトラックを使って運んでいました。そして2年前にタンク職場が9号館に移されて、搬送距離が約300メートルに短縮されたんですね。トラックを使う必要はないけれど、そこにまた人手を割けば余計なコストがかかってしまう。それで省人化と効率化を図るためにAGVを導入することになったんです。いまだにフレームの運搬は人手に頼っていて、フォークリフトが1日何往復もしていますが、ここも2023年3月からCOW-elを導入して、搬送を自働化する予定です。
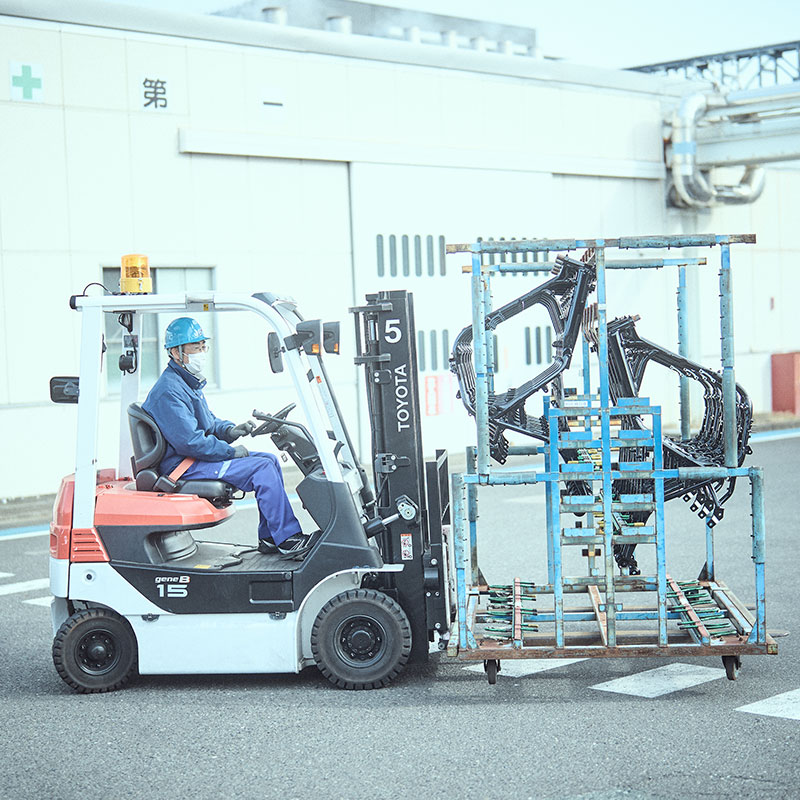
現場に最適化するためにどんな工夫をしましたか?
まずは台車の軽量化です。以前の台車は鉄製で260kgもある非常に重たいものを使っていたので、タンクやフレームを載せると1台の総重量が400~500kgにもなっていました。AGV用の台車はアルミ製で、1台約60kgと非常に軽量です。COW-elの最大積載重量は250kgなので、タンク8個(40kg)を積載しても十分余裕がありますね。
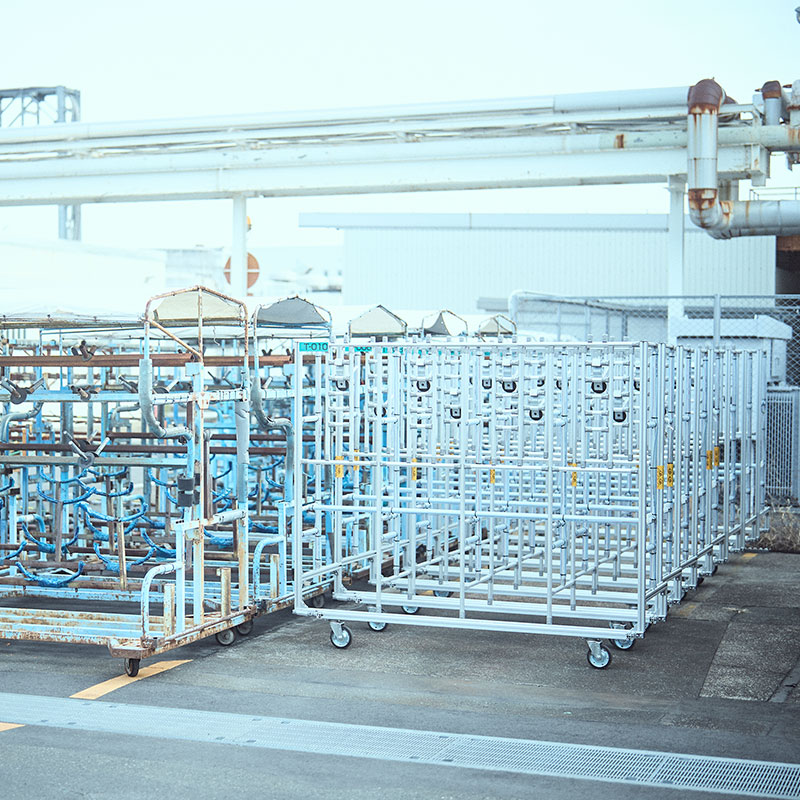
また建屋の間は屋根もないので、天候にも対応する必要があります。タンクは燃料が入るところですから、水濡れには気を使います。だから台車に雨除けカバーをつけたんですけど、今度は風の影響を受けてしまって(笑)。次はそこに風抜きを作って風圧を逃がしたりと、いろいろ工夫を重ねました。
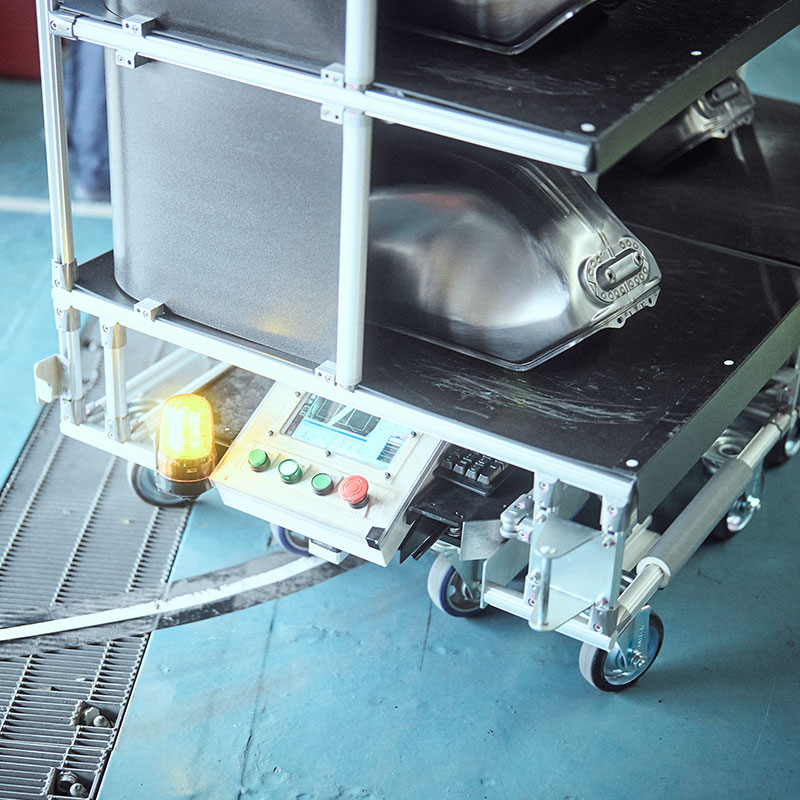
あとは屋外走行への対策です。屋内のルートには安価なビニールテープを使えますが、屋外は耐久性を考えて路面を塗装しました。さらに屋外はフォークリフトやトラックも走っているので、事故防止対策が欠かせません。AGVが通るときはセンサーが感知して「AGV横断中」のサインを点灯させて、音声とともに周辺ドライバーに注意喚起しています。カメラも複数台設置して、常時監視させています。
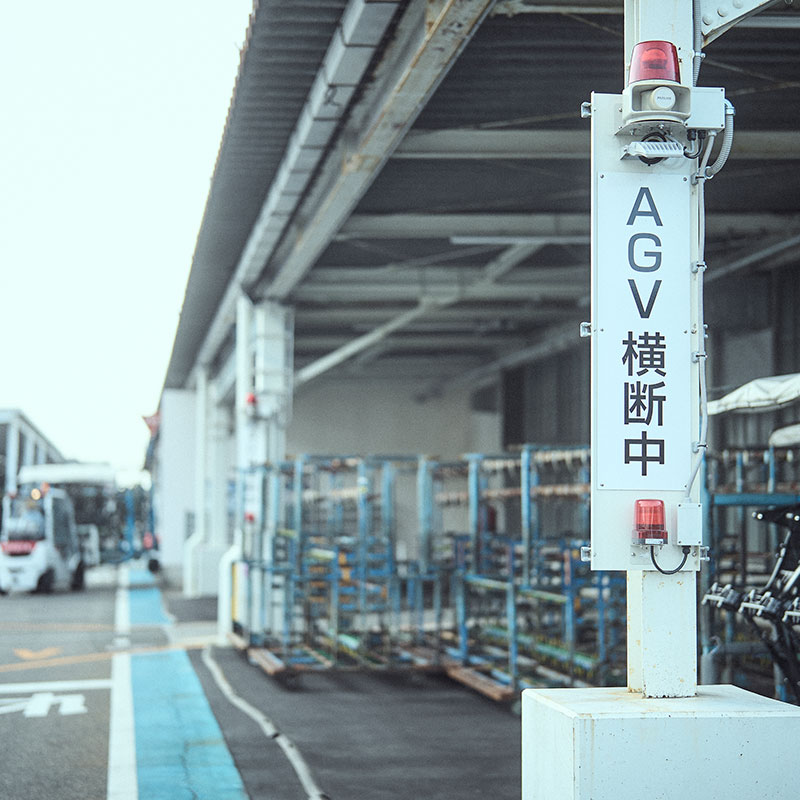
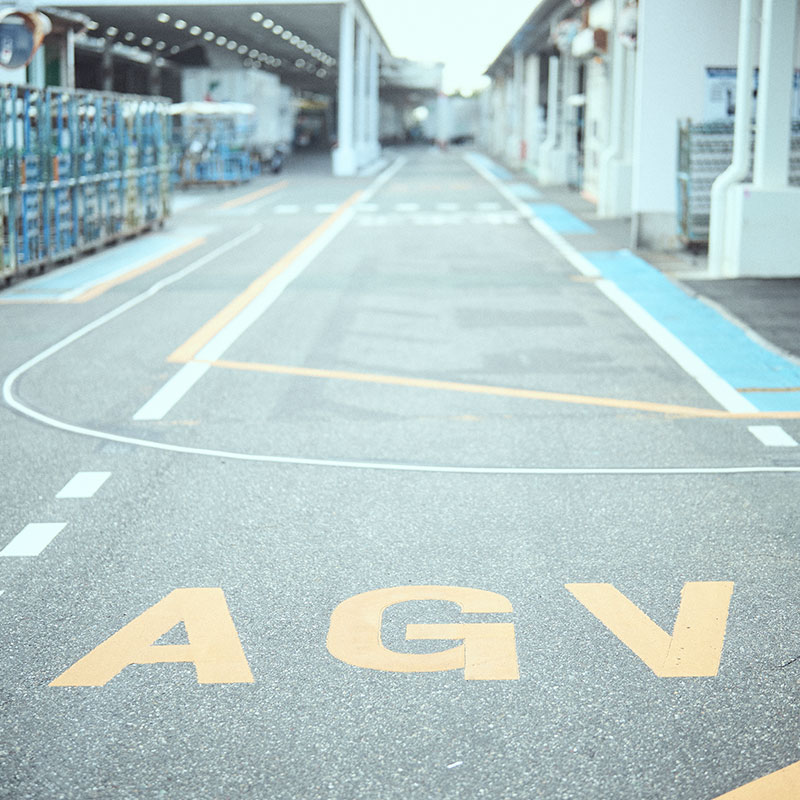
導入後の変化を教えてください!
やっぱり建屋間の搬送を省人化できたことですね。ルートを引くのに市販のビニールテープを使えるというのも、コストもかからないし経路変更も柔軟にできるので、非常に助かってます。 運用ノウハウも蓄積できたので、前述の通りフレームの運搬にも横展開で導入することが決まりました。フォークリフトでは一度に20台のフレームを運んできましたが、今後はCOW-elの最大積載重量を考慮して4台ずつ運ぶ方式に切り替えます。人手に頼らないぶん頻度でカバーできますし、結果的に多品種少量生産への対応にもつながりますよね。
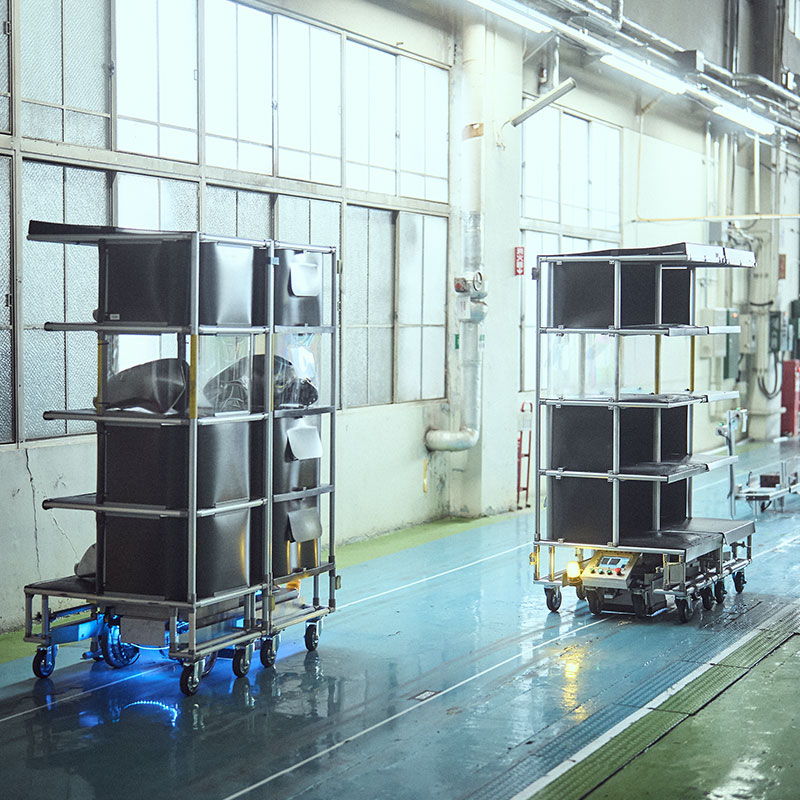
さらなる改善予定は?
実際の運用には、まだいろんな課題があります。ひとつは屋外経路のメンテナンス。屋外経路はペンキで塗装していますが、トラックやフォークリフトも通るのでどうしても汚れやすいんです。ルートの白線が汚れると経路を検知しづらくなって、停止してしまうことがあります。定期的に清掃しながら、もう少し低コストで耐久性の高い塗料やコーティング剤を探して現在も試行錯誤しています。
もう一つは屋外では通信が不安定になること。2つの工場のWi-Fi環境をまたぐため、屋外は電波が混線したり、不安定で途切れることがあります。まだ屋外の通信環境は整備しきれていないので、今後もっと改善する必要がありますね。改善できて現場の走行ログデータがしっかり蓄積できれば、FAチームと共有してAGVのさらなる改良にもつながると思います。
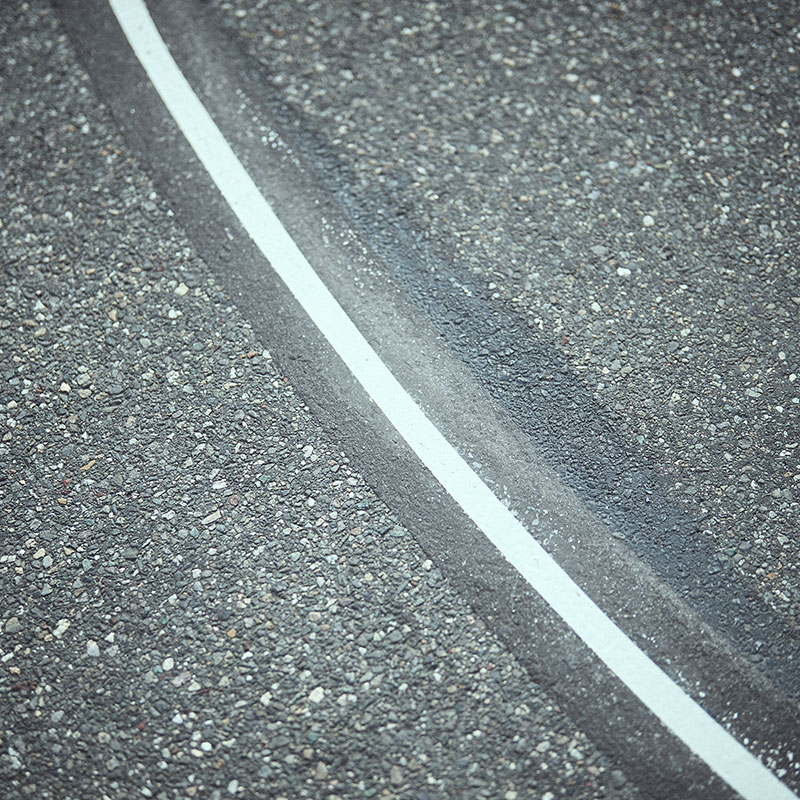
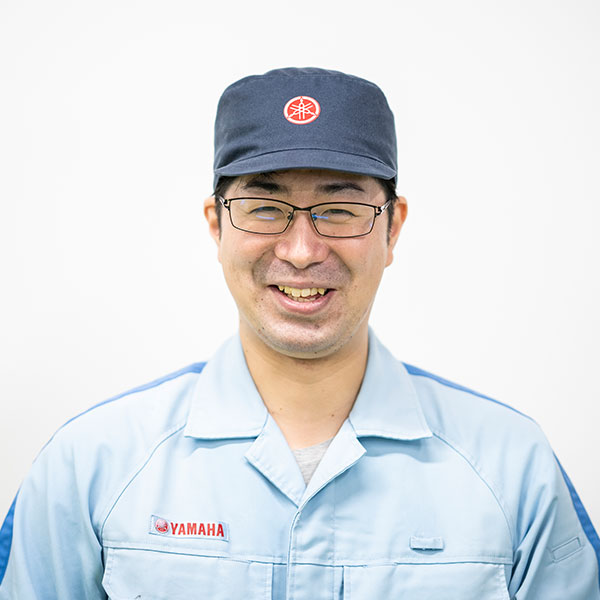
大石 裕也さん
ヤマハ発動機株式会社
FA技術開発グループ
開発者の声
搬送業務の自働化・省人化を支えるAGVですが、一般的な価格は約300万円とそれなりのコストがかかります。とは言えものを運ぶだけの装置なので、導入してもどれだけ利益につなげられるかがわかりにくく、検討段階で二の足を踏んでしまう企業も少なくないようです。また近年は電子マッピング機能や通信機能などを備えた、さらに高機能、高価格なAGVが増えてきました。そこで、もっと現場のニーズに合った機能と装備で、適正な価格のAGVを開発したいと思ったんです。COW-elは搭載するカメラやコンピューターを現場環境に合わせてカスタマイズすることで、コストの設定を低く抑えることに成功しました。
一番の特長はカメラが画像認識でルートを検出することです。多くのAGVは磁気計測方式で誘導に磁気テープを使いますが、コストも高いし、経路上にある鉄骨などが磁化して走行が不安定になるケースがあるようです。また車体のセンサーと磁気テープの距離が開くので段差やスロープが苦手だったりと、意外と使用環境を選ぶんですね。
COW-elは安価なビニールテープでルートが引けますし、段差があっても走行にあまり影響しません。路面の傾斜も6度くらいであれば問題なく通過できますね。ルート上にあるQRコードのようなものはARマーカーといって、これをカメラに読み取らせることで走行速度を切り替えたり、停止して何かの処理をさせるなど、配置するだけで100種類くらいの指示を与えられます。
運用面では走行ログを取って、運行の管理・分析に役立てることができます。バッテリーの消耗具合がわかるだけでなく、各ポイント間の所要時間を比較して、時間を要しているポイントでは作業工程に問題がないか分析したりと、幅広い業務改善につなげられると思います。
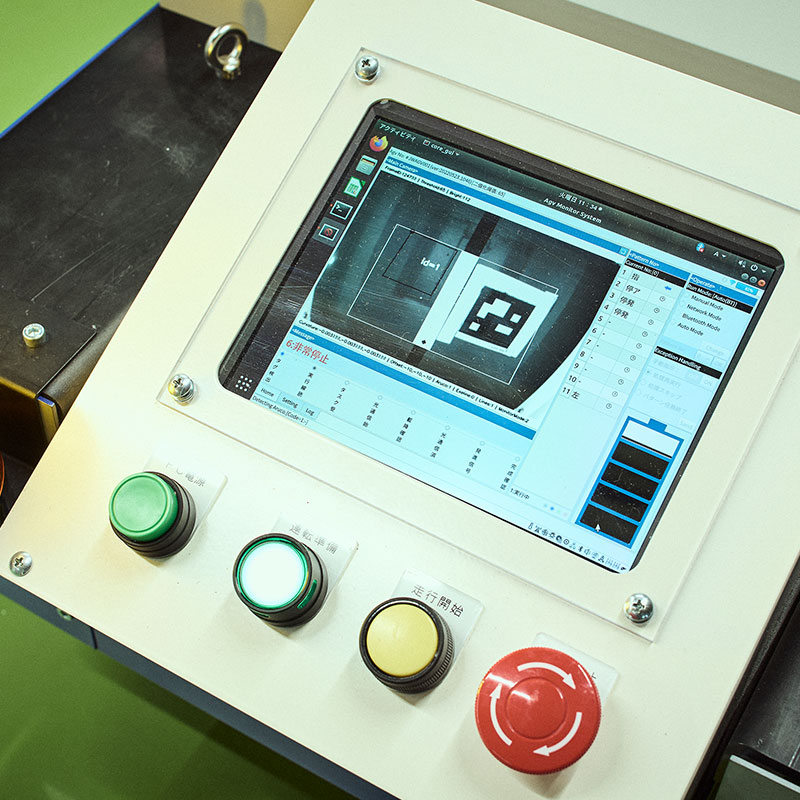
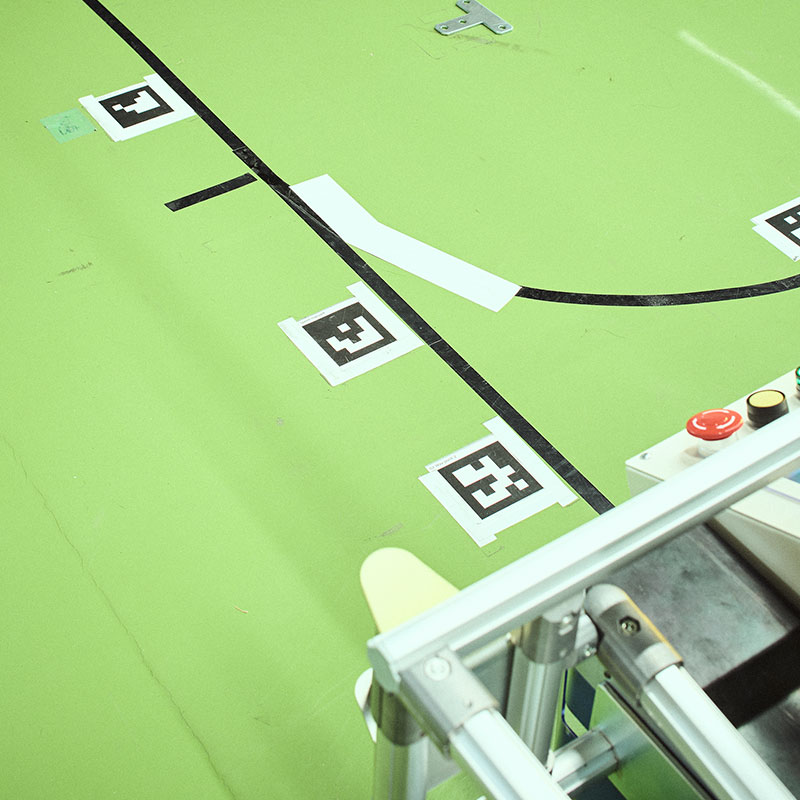
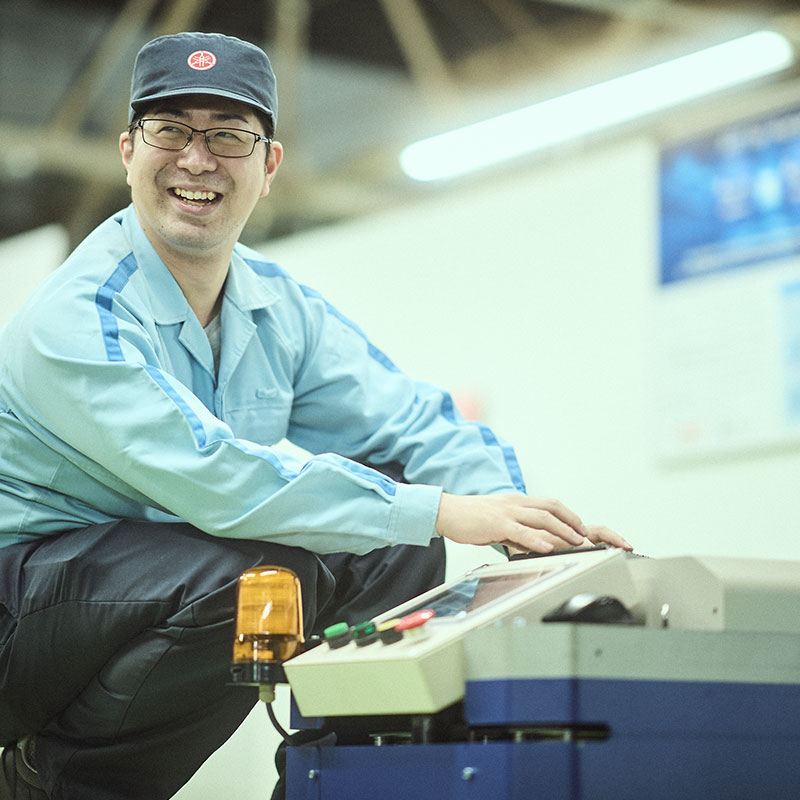