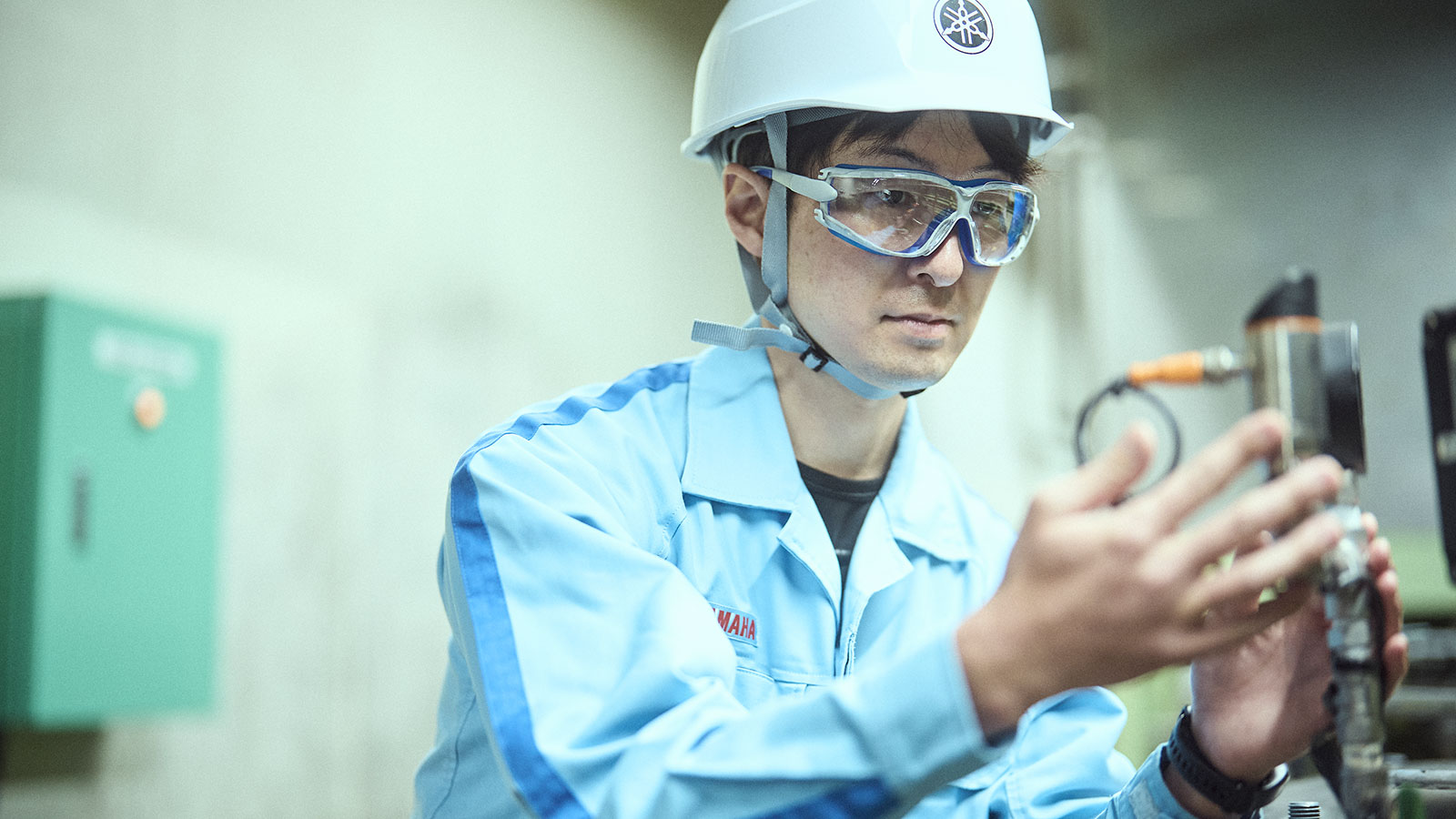
パフォーマー人財紹介
現場の安心感と品質向上をかなえた、「人に寄り添うDX」とは?
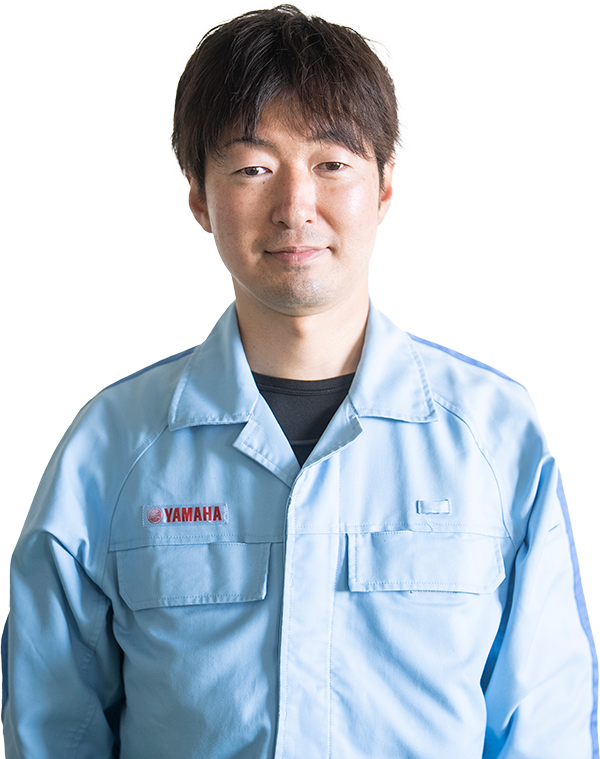
#01 齋藤 義彦
2005年に掛川工業高校を卒業後ヤマハ発動機に入社。
磐田南工場アルミ加工職場に配属され、以来16年にわたって生産現場で経験を積む。2021年にデータセンシング技術開発グループに異動し、システム開発者としてプログラミング、ネットワーク/データベース構築などデジタル技術を学びながら、磐田南工場でDX推進に取り組んでいる。趣味は改善と釣り。
改善マニアからシステム開発者へ
ヤマハ発動機株式会社の磐田南工場M1号館。この工場では、ヤマハ発動機のマリン事業における主力製品のひとつ、船外機を製造しています。齋藤義彦さん(36歳)は地元の工業高校を卒業してヤマハ発動機に入社、以来16年にわたってアルミ加工職場の生産ラインで内燃機部品の製造に携わってきました。経験を積むにしたがって、加工を担当する部品は徐々に大型化し、作業工程もより複雑なものへとステップアップ。2018年からは、20~30名のメンバーをまとめるリーダーに昇格します。
その後は経験を積みながら、さらに上のポジションに昇進したり、現場マネジメントや後進育成を担っていく、というのが一般的なキャリアパスなのかもしれません。しかし齋藤さんはある部署への異動をきっかけに、突然そのキャリアを大きく方向転換することになりました。その異動先とは、データセンシング技術開発グループ(通称:DS技術開発)。ここではさまざまなデジタル技術を活用して、生産現場の困りごとや課題をDXで解決する取り組みが行われています。
「僕はもともと改善マニアなところがあって、ちょっとした工夫やムダを削ることで効率を上げるのが好きなんです。だからウチの部門からDS技術開発に人を出すという話を聞いたときに、自分のまわりでも”これは齋藤が適任なんじゃない?”という空気がありましたね(笑)」
これまでも齋藤さんはNC加工機(*1)のプログラムを勉強し、刃具の材質・回転数・切削スピードなど加工条件の組み合わせで品質が向上することを検証したり、加工機や部品に合わせた刃具の最適化に取り組んだりと、以前から改善熱心なことで知られていました。「いままでパソコンもあまり使ったことがなくて不安もあったんですけど、僕は新しいことをやるのに抵抗がない性格なんですね。いままでとは全然違う環境で働けることもチャンスだと考えて、前向きに挑戦しようと思いました」
かくして、パソコンはほぼ初心者というシステム開発者(の卵)・齋藤さんの「社内留学」が始まったのです。
*1:デジタル制御で高精度な切削加工を行う設備のこと
現場がわかる人にしか作れないシステムを
異動後はいろんな技術をひと通り見て、何でも触れてみたと言う齋藤さん。エクセルを始めてマクロを組んだり、Python(*2)を修得したり、Raspberry Pi(*3)を使うなど、幅広くデジタル技術を学びました。しかし慣れない環境に気を張りすぎてしまったのか、学びの幅を広げていくうちに(この技術が現場に必要なのだろうか)(これをどうやってシステムに実装すればいいんだろう)と気持ちが落ち込んだ時期もあったそうです。
「現場の困りごとを解決するために技術の勉強をしているのに、それをどう活用するか明確なイメージを持たないまま、やみくもに学びすぎてしまって。でも結局自分がやりたいことって、外部のコンサルティング会社やシステム屋さんには作れないような、現場でかゆいところに手が届くシステムを作ることだった、と気が付いて。現場に長く立っていた自分だからこそ、リーダーや作業者の困りごとを理解できるし寄り添える。だから高度な技術を使うことより、ちゃんと現場の人が理解してメンテナンスもできるシステムじゃなきゃダメだなと」
*2:プログラミング言語のひとつ。シンプルで読みやすいコードが特長で、数値計算に強くAI開発分野でよく使われている
*3:シングルボードの基盤と最低限のインターフェースで構成された小さなコンピュータ。通称ラズパイ。数千円程度から入手可能
ここから心機一転、実践型で学ぶスタンスに切り替えた齋藤さんは、さっそく磐田南工場に赴き、ともに汗を流してきた現場の仲間たちに「いま、どんなことに困ってる?」と聞いて回る日々が始まりました。
やがて彼のもとに、職場のリーダーや作業者さんからたくさんの困りごとが寄せられます。「経費がかさむ」「作業時間が長い」といった不満から、大きな予算と時間が必要なものまで、その内容は多岐にわたっていました。齋藤さんはひとつひとつの困りごとを「製品の品質に影響するもの」「その職場のリーダーがどれほど困っているか」という基準で優先順位をつけて、自分の技術で対応できるかどうか丁寧にマッチングしていきました。
はたしてパソコン初心者だった齋藤さんは、どんなシステムづくりで現場の課題に取り組んだのでしょうか。ここでは、実際に齋藤さんが開発を担当した事例のなかから2つのシステムをご紹介します。
「心から安心できる状態監視システム」
塗装職場から相談を寄せたのは、現場で職長を務めていた太田知樹さん。入社時期も年齢も近い齋藤さんを「よっちゃん」と呼ぶほど親しい間柄でした。
「塗装職場には、薬品や塗料が入ったいろんな槽があって、部品をそれらの槽に順番に浸漬することで塗膜を形成してるんです。槽の中は複数のポンプで塗料を循環させていて、各ポンプの入口と出口の循環圧力の差(=差圧)を2時間おきにチェックする決まりがありました。普段業務を行う事務所と塗装職場までは150メートルくらい離れているので、圧力計を見るためだけに1日4~5回も往復するのは疲れるし、移動時間がもったいないと思ってました。しかもメーターがアナログなので、目盛りを読み取って差圧を確認するのもひと苦労です。よっちゃんには『せめてこれがデジタル表示になって、制御盤のモニターで見られたらなぁ』と相談しました」
たかが150メートルと思えるかもしれませんが、工場内は常にフォークリフトや自動搬送機が動き回っていて、普通の道を歩くよりも時間がかかるし神経も使います。またどんなに仕事に集中しているときでも、時間が来たら否応なく席を離れなければなりません。それでもポンプの差圧チェックを絶対に欠かさなかったのは、かつて塗装現場で大規模な不良が発生した過去があるからだと太田さんは言います。
「塗料槽のポンプのうち1台のモーターが止まってしまって、部品の下面に塗料が付いてない、という事態が発生してしまったんです。そのためにライン内の2時間分の製品がすべてダメになってしまって。部品数は約300台、損害額にすると150万円以上です。幸いにも修正工程を入れることで、破棄せず製品として再利用することはできました。それでも300台の製品をひとつひとつ選別したり、重いものはホイストクレーンで釣りあげてタッチアップしたりと、1週間は膨大な修正対応に追われましたね。もう思い出したくないほど大変だったし、二度とあんな思いはしたくない」
そこで齋藤さんは圧力計のアナログメーターをデジタル化しただけでなく、それらをPLC(*4)やIO-Linkマスターなどのデバイス、そしてデータベースサーバとLANでつないでネットワークを構築。また事務所にPCとタッチパネルを設置して同じネットワークにつなぐことで、事務所から遠隔で電着塗装ラインの状態監視ができるシステムを開発したのです。
*4:外部設備をコントロールするための制御装置
さらにこのシステムで太田さんが驚いたのは、システムが監視している圧力計の数値がデータベースとして蓄積されることでした。「単に点検工数が減っただけじゃなくて、循環圧力のデータが蓄積されることでその傾向を把握できるようになりました。これまでポンプのフィルターはだいたいの間隔で交換してたんですけど、データからもっと長く使えそうなことがわかったので、メンテナンスのサイクルまで見直すことができたんです」
齋藤さんが太田さんの負担を理解できたのは、自分もリーダーとして品質を重視してきた経験があったからだと振り返ります。「塗装工程は品質に直結する管理項目が多く、その管理の工数が課題だったので、これは絶対どうにかしたいと思いました。体力的な負担のほかにも、毎日の移動時間は見えないコストとして相当かかっているはず。目の前の仕事に追われると他のことが考えられなくなって、ムダとわかっていても決められたことをこなしてしまう。できることは自動化して点検時間を減らすことで、職長やリーダーの方に業務を見直したり考える時間を作ってあげたいと思いました」
齋藤さんが開発した電着塗装職場の状態監視システムは、思わず太田さんが「あぁ、これでやっと心から安心できるわ・・・」と漏らしたことに由来して「心から安心できる状態監視システム」と命名。工場内の設備盤にもしっかりプレートで掲示されています。
今後は塗装現場でこのシステムを横展開することで、別の薬品槽や配管なども状態監視できるようにしたいと考えているそうです。そうすることで現場のみんなが安心して気持ちよく働ける環境を作っていきたい、と太田さんと齋藤さんは嬉しそうに語りました。
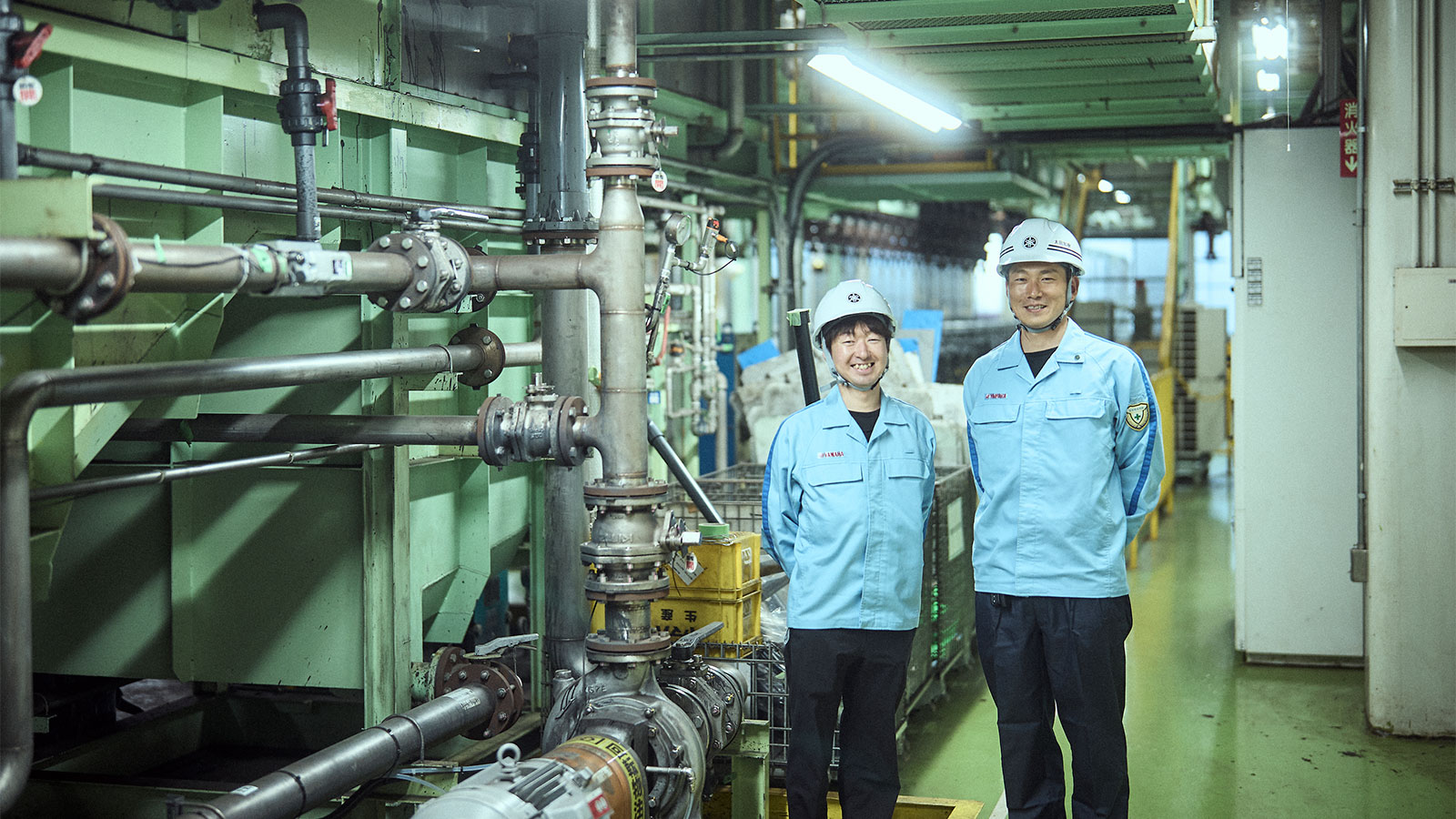
「レーザー刻印機を介したトレサビシステム構築」
次に齋藤さんが着手したのが、内燃機のヘッドシリンダーのトレーサビリティ(*5)を確立するためのシステム構築。これは鋳造・塗装・加工と異なる職場のラインをまたいで流れる製品の作業履歴を、一気通貫で管理してデータベース化するというものです。「ここは誰かが困っているというより、品質管理コストがムダにかかっていることが大きな課題でした。それまでは各工程の中だけで品質を管理していたので、前後の工程と情報がつながっていなかったんです。後工程で不良がわかっても、1か月後に紙のチェックシートが戻ってきて初めてわかるような仕組みで、自分たちの工程記録と照合するにも長い時間を要していました」
*5:製造や生産の過程、あるいは流通などをさかのぼって追跡できること。ここではトレサビと略称
すべての製品は最初の鋳造工程で2Dの識別コードが刻印されますが、素材面(塗装肌)に刻印すると塗装処理されるため次の工程で読み取れなくなってしまいます。かと言って塗装しない加工面(切断面)に刻印すると、加工の最初の工程で削られてしまいます。刻印を最後まで活かすためにはまず加工面に打ち、そして消失する前に塗装後の加工しない位置に同じものをレーザーで打ち直せばいいのですが、その手間を請け負う加工職場にとっては大きな負担となってしまいます。実際に「それってこの職場にどんなメリットがあるの?」とも言われたそうです。それに対して齋藤さんは、識別コードとそれに紐づく設備データがすべての工程でつながれば、生産ライン全体の改善になるだけでなく、ヤマハブランドの信頼性も高まると説明しました。
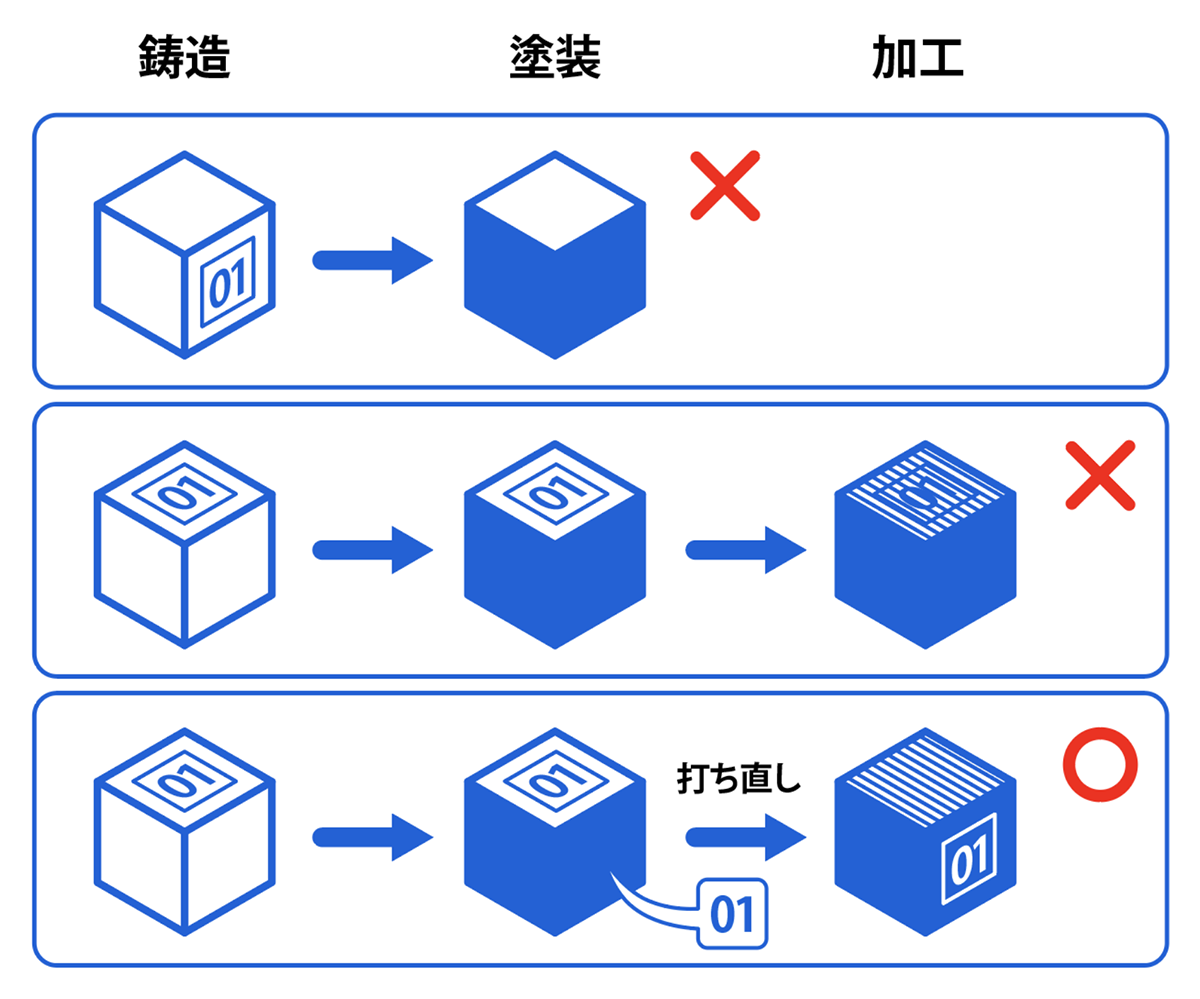
「たとえば鋳造工程で製品内にガスが発生して空洞ができた場合、加工職場で削って空洞を見つけて初めて不良品だとわかるんです。これがデータベースでつながればリアルタイムで前工程にフィードバックされるので、鋳造職場はすぐに改善のアクションがとれるし、結果的に加工職場に流れる不良品が減ります。加工職場での不良も即時にフィードバックされるし、データベースで加工時の設備状態と照合すれば、その時の切削条件が適切だったかどうか答え合わせができるんです。結果として生産ライン全体の改善プロセスが大幅に短縮するので、品質管理コストが下がって品質は向上しますよね。そうやって現場が真剣に品質を追求している姿勢は家族や友人にも伝わっていくし、めぐり巡ってヤマハブランドの信頼感を高めていくことにつながると思うんです。」
このトレサビシステムは複数の部署の協力を必要としたため、齋藤さんはシステムの開発だけでなく各部署の意見ヒアリングと調整に奔走しました。通信システムも自分たちで構築したほか、レーザー刻印機は工業用のものに安価な市販のレーザーヘッドを組み合わせるなど、導入コストを下げる工夫も忘れていません。さらに生産現場と一緒になって開発しなければシステムは浸透しないと考え、レーザー刻印機のプロトタイプを制作してデモンストレーションを実施。現場の作業者から使用感や意見を徹底的に吸い上げたのです。
そしてシステムが稼働し始めた現在、齋藤さんは思いがけない効果を目の当たりにしています。このシステムの役割やデータがつながることの意味を現場の作業者たちに話すと、みんなが笑顔になり「それじゃこんなデータも取れない?」「このデータを取ればこういうことがわかるよね?」と、どんどん意見が上がるようになったのです。 かつての自分と同じように、パソコンもほとんど使わないような現場の方の意識が変化してきている、と語る齋藤さん。もしかするとその中から、齋藤さんの後進となる人材が出てくるかもしれません。
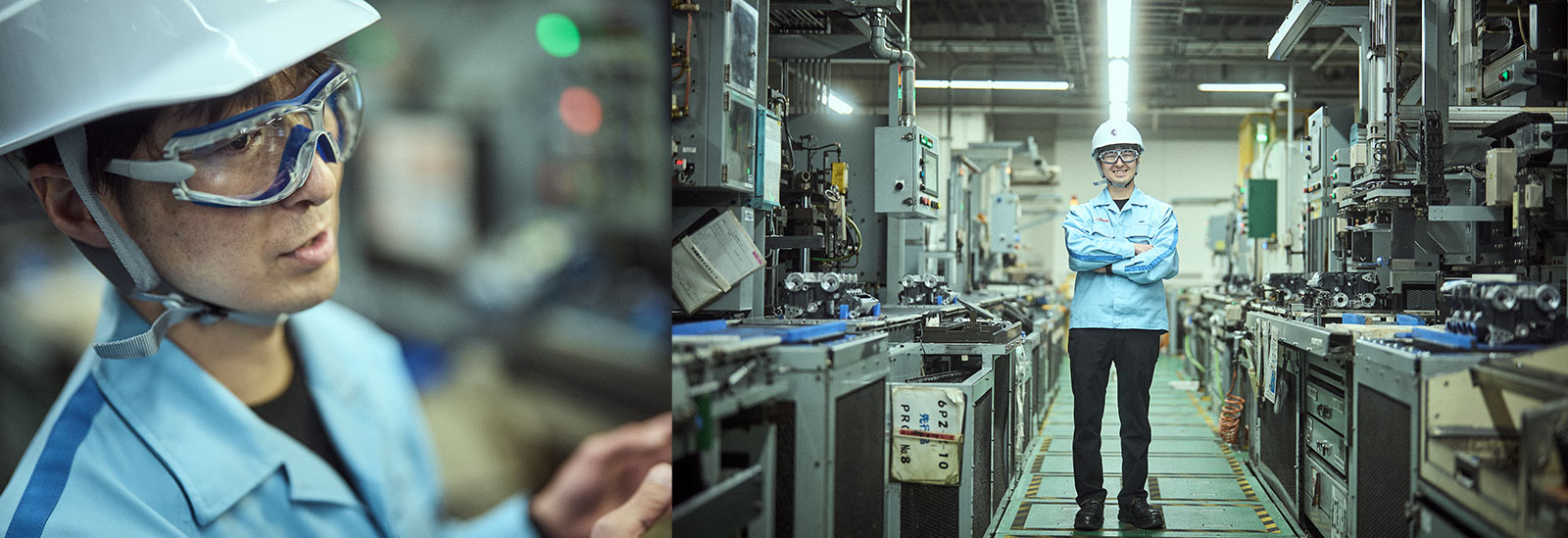
末端からのデジタル化で基幹を支えたい
DS技術開発グループにある齋藤さんのデスクには複数のモニター、パソコン、ラズパイがところ狭しと並んでおり、もうそこにはパソコン初心者だった齋藤さんの面影はありません。「デジタル化やプログラミングは、自分でも一足飛びで順応したなと思います。でも僕は特別手先が器用なほうでもないし、ただ改善が好きなだけ。むしろいま仕事で役立っているのは、人と話をすることが好きで、いろんな年齢層や役職の方とも抵抗なく話ができる性格だと思ってるんです。僕はおばあちゃんに育てられたので年配の方と話をするのが好きだし、四兄弟の末っ子だったので人の懐に入っていくのが得意なんですよ(笑)」
そして2023年、ここで紹介した電着塗装状態の監視システムやトレサビ管理システムは、磐田南工場でさらなる横展開や拡大導入が予定されています。現在齋藤さんはその準備に追われていて、部署内の調整や機材選定など大忙しの毎日を送っています。今後はどんなシステムづくりを手がけていきたいか、目標や展望についてうかがいました。
「やっぱり自分が最もこだわってきた、品質を守れて、かつその生産ラインの事情に合った廉価なツールやシステムを開発して現場に恩返しをしたいですね。低予算にこだわっているのも、やはり現場に導入するハードルを下げていきたいからなんですよ。僕の考えでは、大きな基幹となるシステムは全体で入れて統一化しながら、末端部分の毛細血管みたいなところでは、僕のような現場の事情がわかる開発者が、しっかり当事者ニーズを拾い上げてDXを整備していかなければと思っています」