Recipe 1 超廉価版パーツピッキング装置
閃きプラットフォーム開発レシピギャラリー
閃きプラットフォーム開発レシピギャラリー
Recipe 1 超廉価版パーツピッキング装置
開発のポイント
- 1 汎用品のロボットやカメラを活用し、パーツの自働切り出しを低価格で実現
- 2 ハケで余分なパーツを取りはらって、トッププレート上のパーツを2D認識
- 3 ツールヘッドやトッププレートを交換すれば、複数のパーツに対応
工業製品の製造工程では、ねじ、ボルト、カラーなど種類・数ともに膨大な量の小型パーツを扱っています。生産を効率化するためには、これらの部品を作業工程に合わせて規定数に切り分ける作業が欠かせません。しかし、いまだにその作業の多くは人の手によって行われているのが現状です。
この装置では、汎用ロボットのツールヘッドにピッキング用のチャックを装着してプログラミングすることで、パーツの切り出しを自働化しました。トッププレートに乗ったパーツをカメラで認識して拾い上げ、設置したトレーのマスに設定した個数ごとに配置。すべてのマスに部品を配置し終えたら自働でトレーを送り出し、新たなトレーの設置も行ってくれます。特長はトッププレートをハケではらい、カメラがパーツの形状を認識できる状態、かつロボットがピッキングしやすい姿勢に揃えること。そうすることで上部に設置したカメラがプレート内のパーツの位置と形状を2Dで認識して、ひとつずつ確実にピックすることができるのです。またツールヘッドのチャックとトッププレートを取り替えることで、画像のような円形のパーツだけでなく、さまざまな形状のパーツに対応します。ロボット、周辺パーツ、制御用コンピューターなど部品の大半に汎用品を用いることで、機材費を安く抑えることができました。
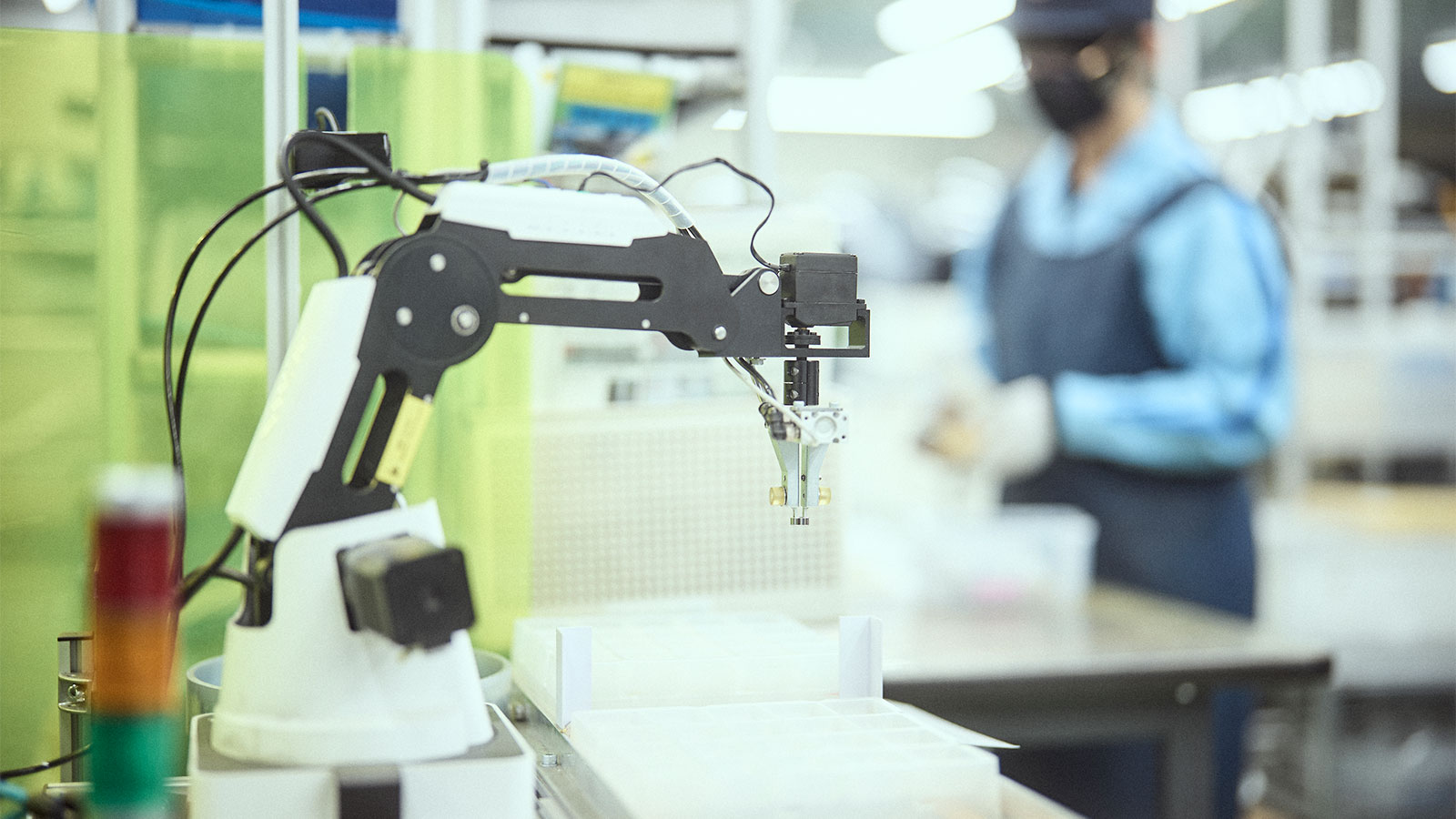
現場の声
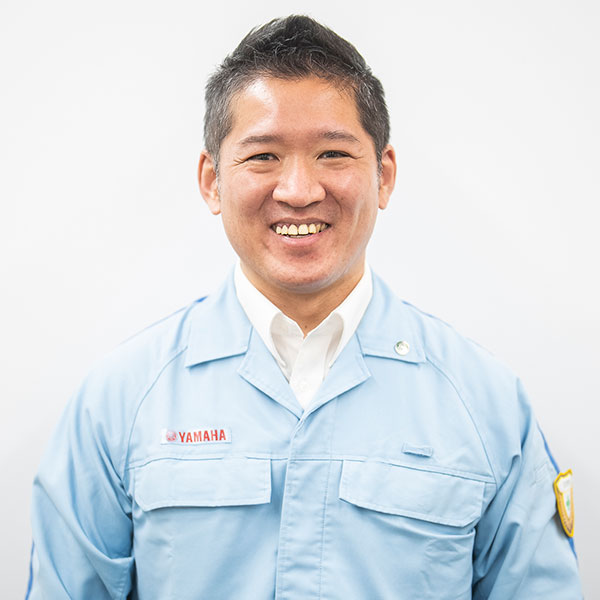
伊藤 三樹さん
ヤマハ発動機株式会社
中瀬工場
車体製造部生産2課 第1工区
どこに導入しましたか?
船外機のME(マリンエンジン)ユニット部品払い出しという工程です。ここでは担当の作業者が一人で何種類もの船外機用組み付け部品を工程に応じた数に仕分けて切り出していますが、そのうちカラーというパーツの切り出しを自働化しました。
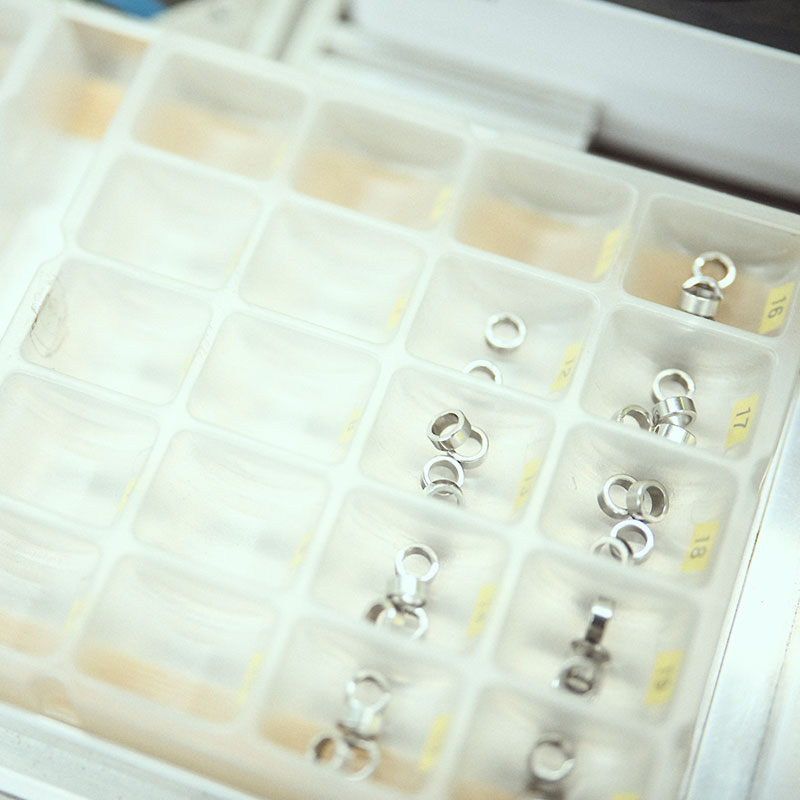
どんな課題がありましたか?
困っていたのは、部品の種類が多いのでただでさえ作業が煩雑なうえに、ほぼすべてが手作業で行われていたことです。しかも現在は船外機の需要が右肩上がり。今年度の生産目標台数も上方修正して、部品切り出しの仕事量は1人工から1.2~1.5人工にまで膨らんでいました。でも、1人工に満たない仕事量のために人を新たに雇うのは難しい。残業や他のラインからの応援で対応していたんです。
しかも人間がこのような単調かつ大量の繰り返し作業を行う場合、ミスを0にすることはできません。もし余分に1本ボルトを配置して作業後にその1本が残ってしまったら、現場ではまず「万が一でもボルトのつけ忘れがないか?」とロットをすべて確認しなければなりません。作業を自働化することでミスの発生率を少しでもゼロに近づけることは、品質向上のためにも必要なことだと考えていました。
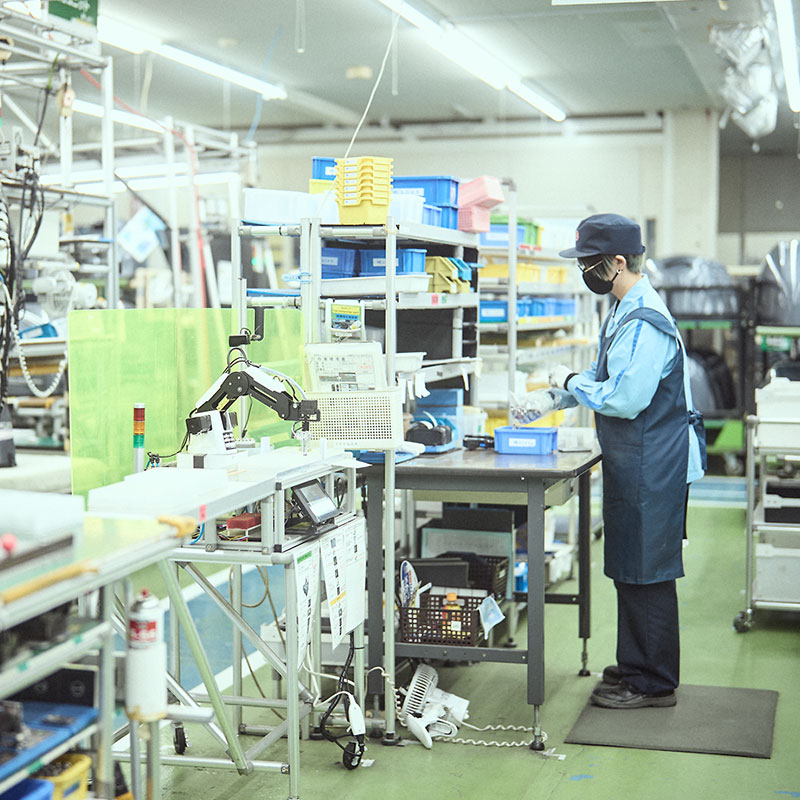
導入後の変化を教えてください!
現在のところ1日8~10時間くらい稼働しており、担当者の作業量1.5時間分を自働化することができました。システム導入は2021年10月ですが、かかった費用は7〜8か月で回収し終えて、それ以降はすべて利益を生んでいるという計算になります。この実績を受けて、2月中に同じシステムをもう1台導入することが決まっています。低価格なので検討から導入決定までを非常にスピーディに進められることもメリットですね。それに消耗部品もほとんど汎用品なので、一般的な通販サイトで安く入手できるんです(笑)。
またこのロボットの動作は、他の作業にも応用できることがわかりました。同じ職場内では接着剤のディスペンサーと連携させて、ゴムダンパーの接着剤塗布を自働化しています。接着剤は揮発性物質のため作業者への負担が大きいうえに(ゴーグルとマスクが必須)、手作業による塗布は使用量にムラが出たり、静電気による接着剤の糸引きが製品に付着して不良を起こす原因にもなっていました。塗布の自働化でこれらをまとめて解消することができました!
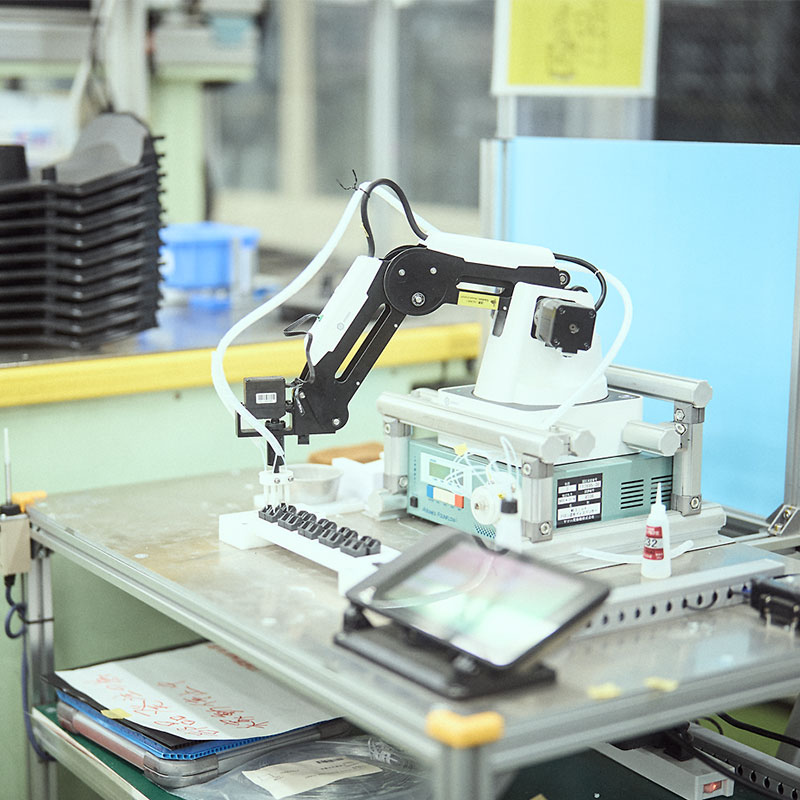
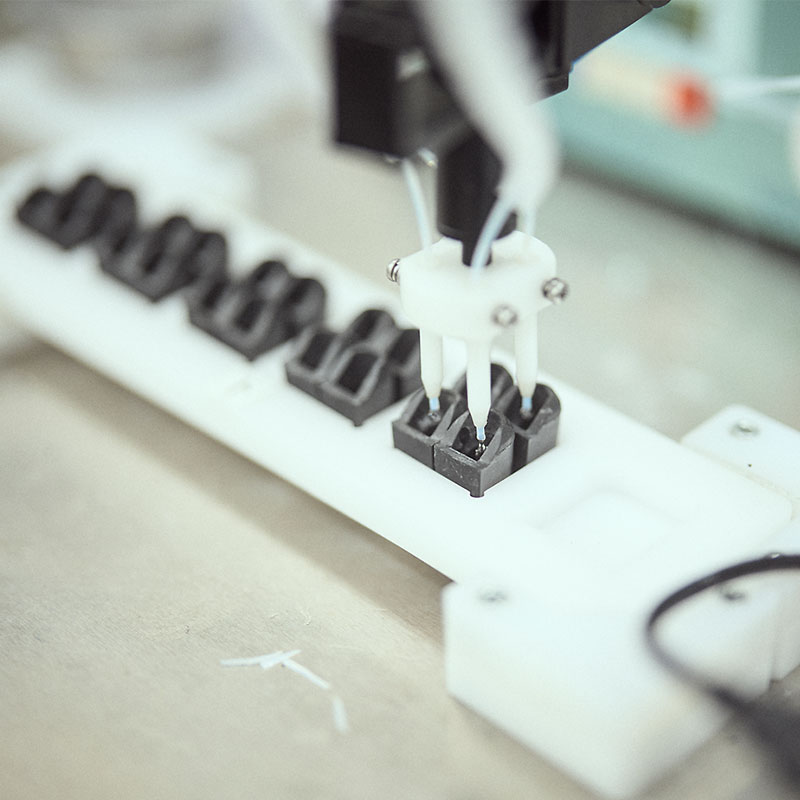
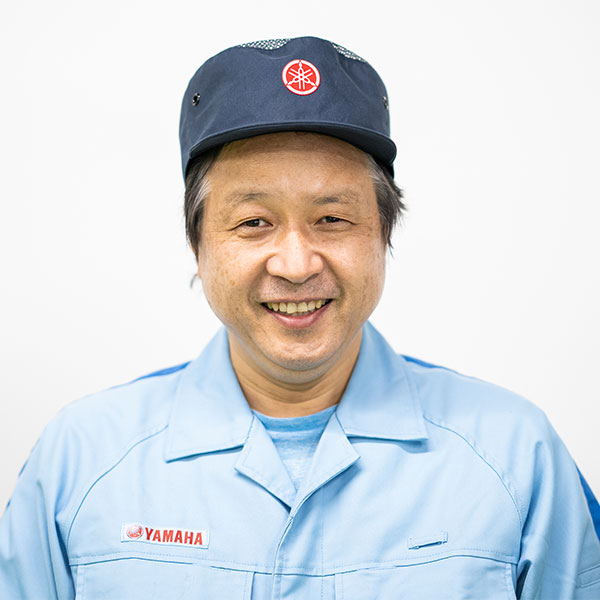
小曽 勉さん
ヤマハ発動機株式会社
FA技術開発グループ
開発者の声
このようなパーツのピッキングを行う装置は、既に世の中にたくさん存在しています。しかしガチガチのFA(*1)機器はいずれも大型かつ価格も数百万円と高コストなものばかりで、導入に踏み切れない生産現場が多いのではないでしょうか。この装置はシンプルな構造でなるべく低コストで実現することを目標に開発しました。そのため、構成要素となるロボットや部品のほとんどに汎用品を活用しています。核となるロボットアームは教育機関などでも用いられるDobotを、制御には安価なシングルボードコンピューターを採用しました。ソフトは基本OSをベースにしつつ、画像解析などはオリジナルで作り込んでいます。カメラやリレーも手に入りやすい汎用品にしたりと、維持管理コストを下げる工夫をしています。
*1:ファクトリーオートメーションの略称。工場などにおける生産ラインや検査を自働化するシステム
じつはこの装置で一番こだわった部分は、パーツの姿勢を揃え2D認識するために「ハケ」を採用したことですね。意外でしょう(笑)? 鉄板やゴム板などいろんな素材で試行錯誤してやっとハケにたどり着いたんです。毛の素材、コシ、毛足の長さも理想的なものを追求しました。ツールヘッドとトッププレートを交換すればいろんなパーツのピッキングに応用可能で、エアで吸い上げて球状や板状のパーツを拾うこともできます。1台で複数のパーツに使ってもいいし、小型で安いのでパーツの種類ごとに導入してもいい。現場の事情に合わせた使い方で役立ててほしいですね。
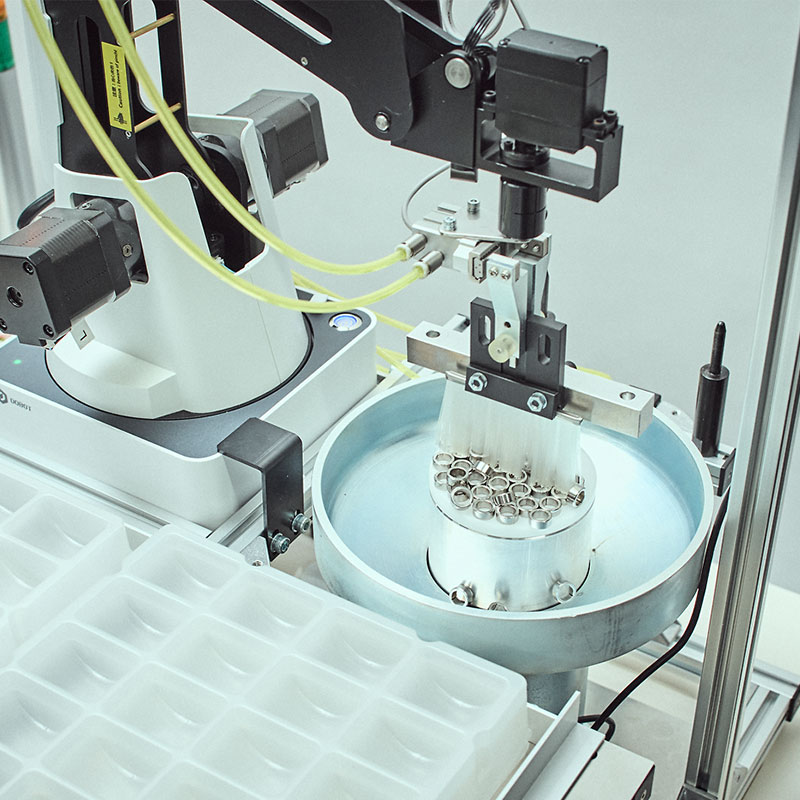
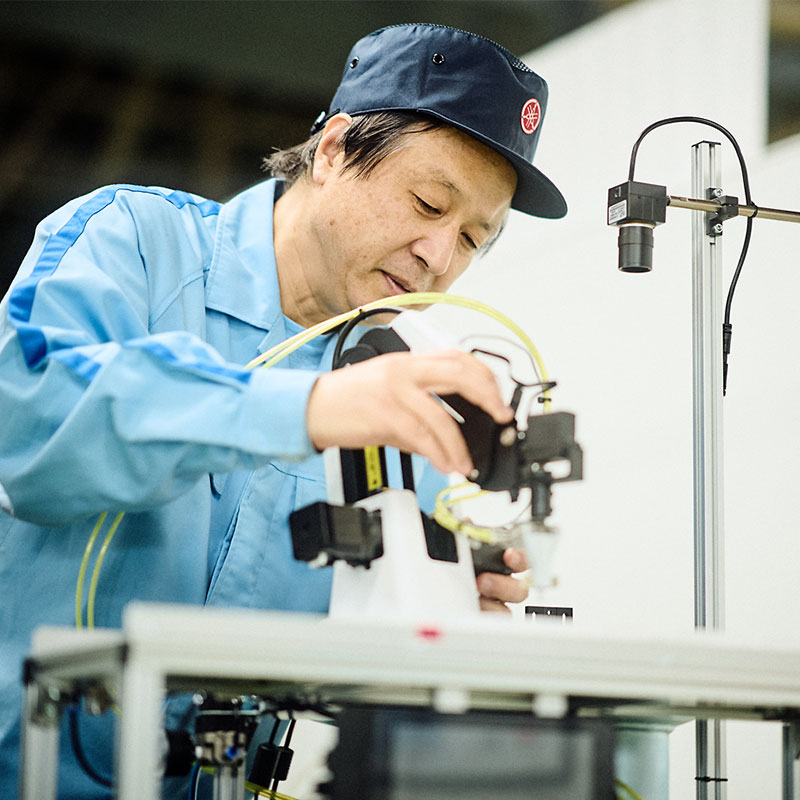