Recipe 5 廉価パーツカウンター
閃きプラットフォーム開発レシピギャラリー
閃きプラットフォーム開発レシピギャラリー
Recipe 5 廉価パーツカウンター
開発のポイント
- 1 シンプルな設計かつ汎用部品を組み合わせることで、低価格化を実現
- 2 ステッピングモーターを使った独自の回転で、パーツの引っかかりを解消
- 3 3Dプリンターで作るシューターは、現場の要望に応じてカスタマイズ可能
製造現場では生産効率を上げるために、小さなパーツを正確かつ大量に切り出す工程が欠かせません。重要な工程ですが単調な繰り返し作業を伴うため、人手で行う場合はどうしてもヒューマンエラーが生じがちでした。しかしそれを解消する産業用のパーツカウンターやパーツフィーダーは高価格なものが多く、多くの現場で導入のハードルになっているのです。この廉価パーツカウンターは、筐体やトッププレートの設計にいたるまでなるべく汎用品を組み合わせる形で開発を進め、コストを低く抑えることができました。フィーダーは正転と逆転を繰り返す独自の回転にすることで、引っかかりをなくしてスムーズにパーツ供給を行います。シューターも現場に合わせてカスタマイズで製作することで、作業効率の向上に貢献します。
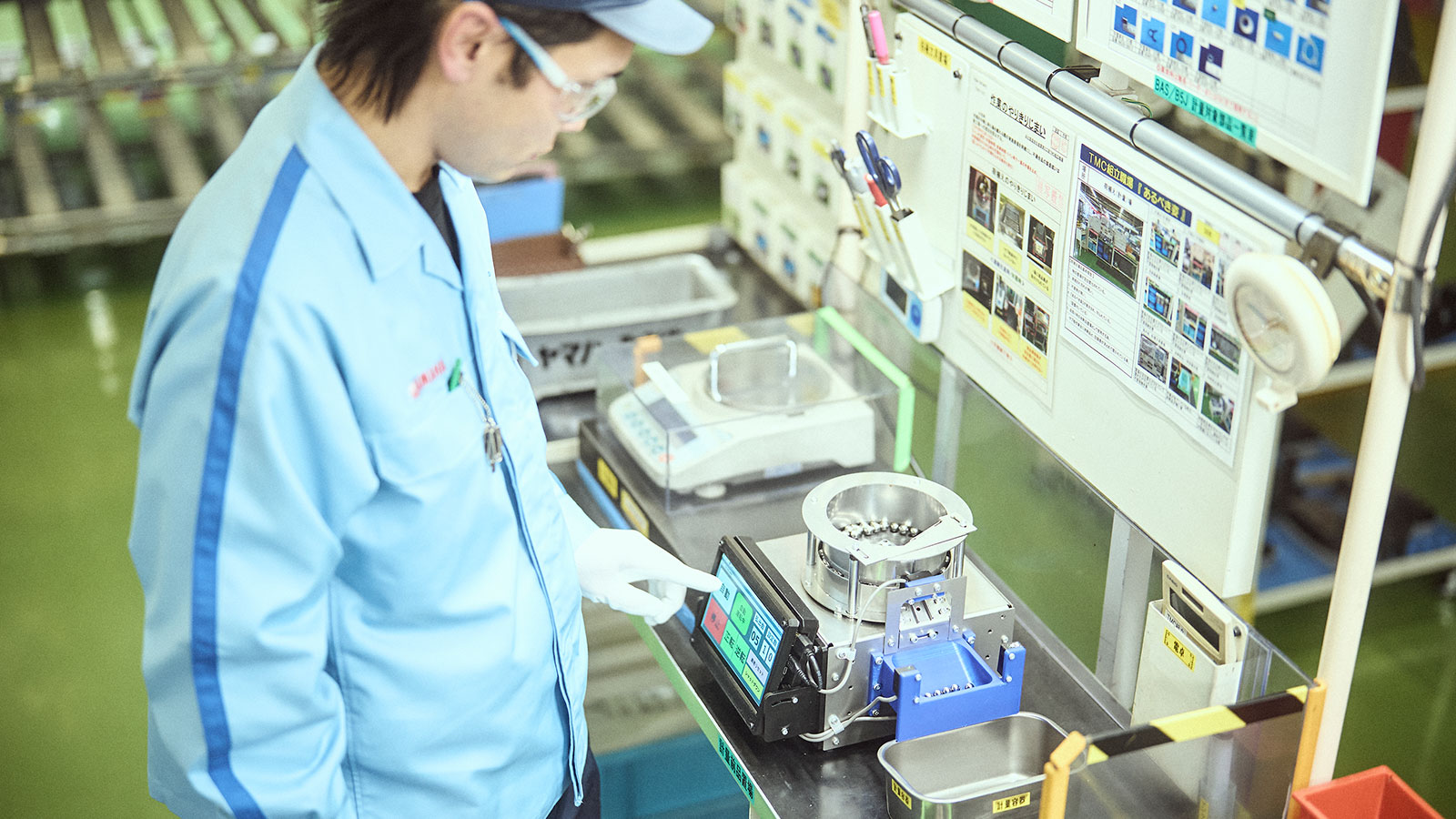
現場の声
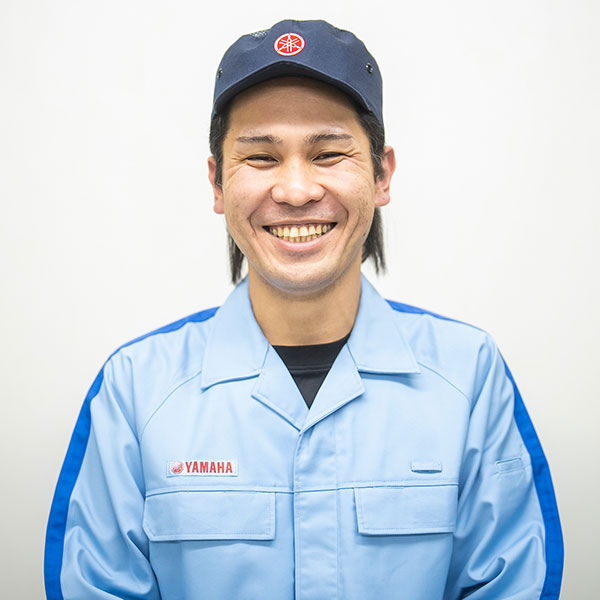
足立 貴之さん
ヤマハ発動機株式会社
浜北製造部生産課第2工区
どこに導入予定ですか?
ヤマハ発動機浜北工場にある、TMC(トランスミッションケース)組立という職場です。ここはROVと呼ばれる四輪バギーのトランスミッションを組み立てる職場で、今回はその中の「部品計量工程」といって、部品の受入・切出しを行い、構成部品のロット保証を行う作業で導入することになりました。
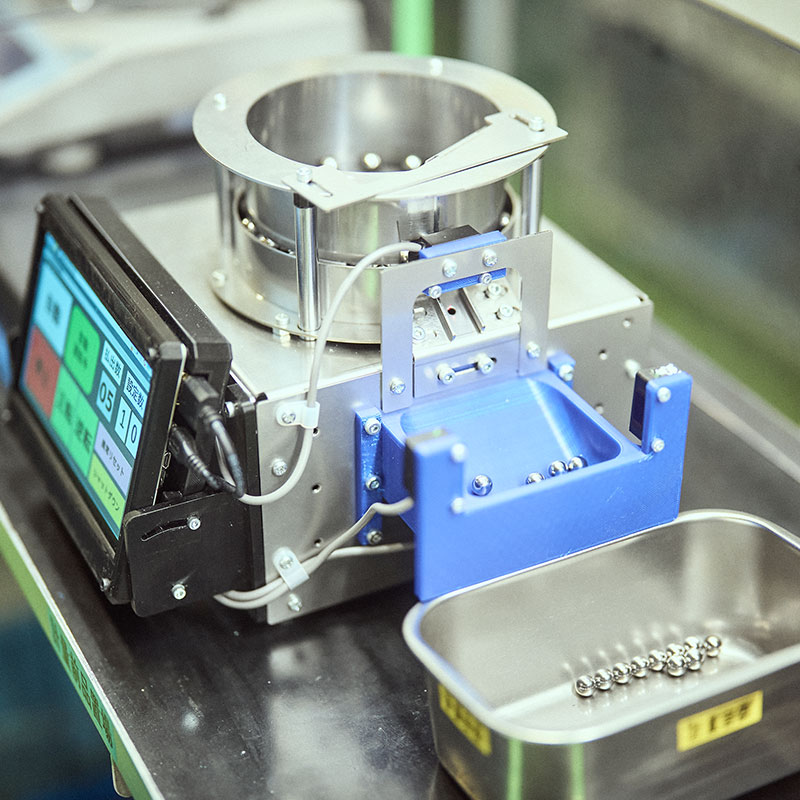
どんな課題がありましたか?
きっかけは2年前に発生した不具合で、作業に使う球状の部品がひとつ余ってしまったことです。製造現場では部品が1つでも余剰・不足が発生してはいけません。と言うのも、品質保証の観点から「製品に組み付け忘れてしまった、2つ重ねて組み付けてしまった」という可能性をまず排除しなくてはいけないからです。そのため今回の余剰が発生してしまった事案については、当日その時点までに組んだすべての製品を点検して、つけ忘れがないことを確認してからやっと「もともと1つ多く入っていたのでは?」と推測できたんです。その部品は10個分の総重量を計測して切り出していたのですが、計量器のゼロリセットが正しく行われていなかったことが原因でした。それ以来さまざまな部品の切り出し方を試行錯誤してきましたが、なかなか使いやすくて現場に馴染む方法が見つからなかったんです。そこでFAチーム(*1)に相談すると、ワッシャー用のパーツカウンターを調整してボール部品にも使用できることを教えてもらったんです。すぐにデモ機を入れて検証してみて、手ごたえがあったので今年度中に2台導入することが決まっています。
*1:「テミル:ラボ」プロジェクトを主導的に進めているチームのこと
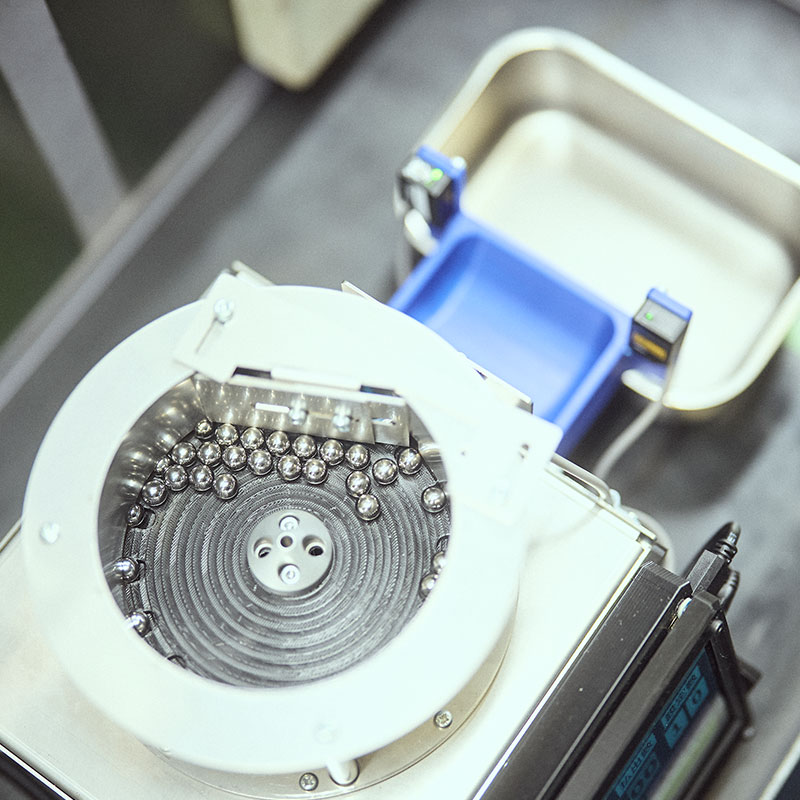
どんな効果を期待していますか?
作業を自働化するメリットって、「サイクルタイムが削減できて何人工浮いた」とか「何時間ラクできた」ということばかりが語られますよね。でもここで導入する目的は、あくまで「品質保証へのこだわり」です。個々の作業者の品質保証を上げることで、常に一定の品質をキープしたい。この職場では派遣社員の方が多く、人が入れ替わることも珍しくありません。人間だからミスや漏れもありますし、作業者の習熟度によって作業時間のバラつきもあります。でもこうした装置を作業の仕組みに落とし込んでしまえば、バラつきもミスのリスクも減らせますよね。つまり仕事の確実性を高めて「作業者の方が安心して働ける環境づくり」を実現するための導入なんです。
パーツカウンターはまず2台の導入ですが、思いつくだけでもあと4種類くらいの部品で使えそうだと見込んでいます。今回の導入を皮切りに、品質保証の仕組みづくりをさらに強化していきたいですね。
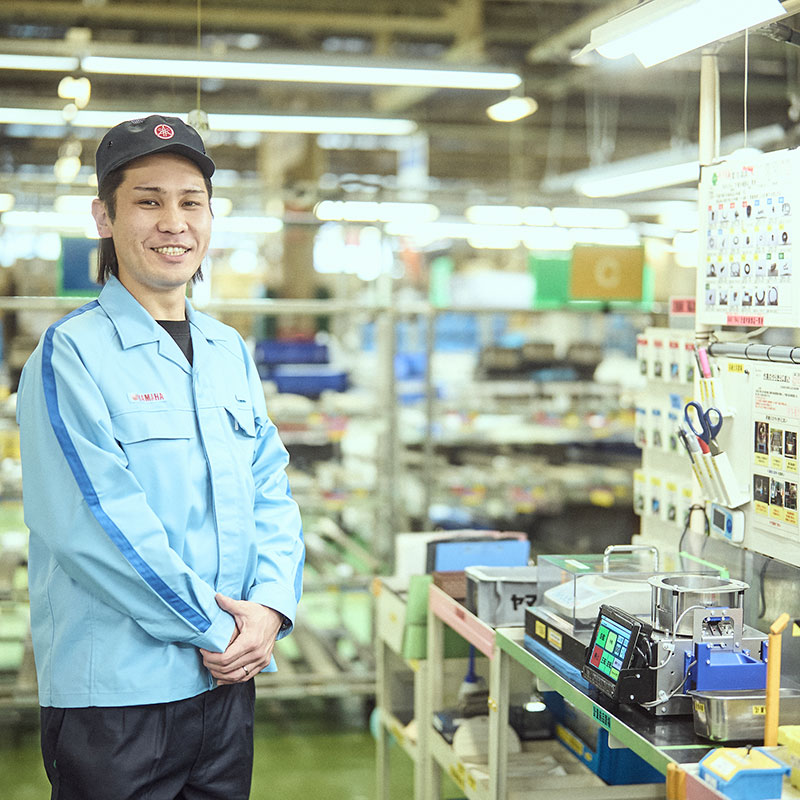
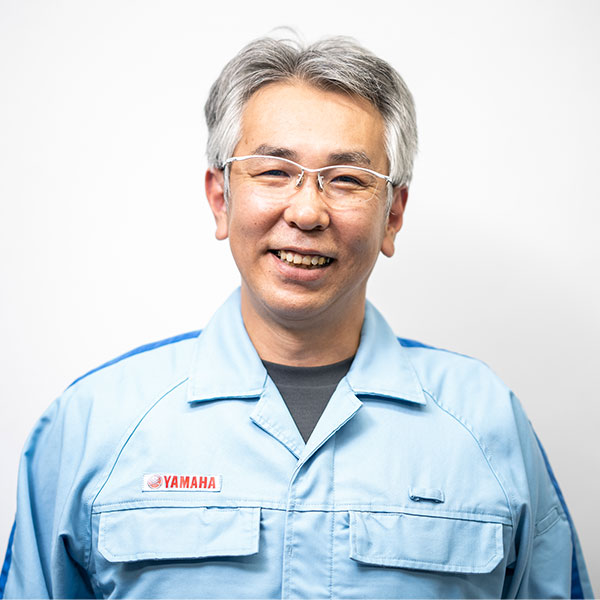
佐々木 徹さん
ヤマハ発動機株式会社
FA技術開発グループ
開発者の声
僕は現在の部署に移る前に、現場で26年の勤務経験があり、そのうち5年間は改善業務に携わっていました。現場では部品やツールをキット化して生産効率の向上を図っていたんですけど、人が手作業でやるとどうしてもミスが起こるんですね。部品が足りなければ届けに行ったり、キットの作業者に伝えたりと、走り回ってものすごく大変だったんです。だから機械で正確に出す必要性は痛感していました。そこでネックになるのが装置のコスト。1つの小さな部品を正確な個数で出すために、何十万円も何百万円もするようなフィーダーを導入するのは現実的じゃない。だからコストカットには特に配慮して設計しましたね。フィーダー底面のプレートや筐体も、余計な加工費がかかりにくいシンプルな形状にしました。素材はパーツとの摩擦にも強く、摩耗したり金属カスが出ないように、硬度の高いステンレスを採用しています。制御には安価なシングルボードコンピューターを使い、操作用のタッチパネルも汎用品を組み合わせて、コストを低く抑えることができました。
最も工夫したのはフィーダーの回転ですね。時計回りに正転しているように見えて、じつは正転と逆転を細かく繰り返しています。パーツはひたすら一方向に回っていると、そのうち引っかかりが生じてしまうんです。この装置では遠心力でパーツを外に押し出し、正転と逆転を繰り返すことで、引っかかっていた部品の姿勢を変えて部品詰まりを解消しています。
シューターと呼ばれる青い部分は3Dプリンターで作りました。この部分は作業工程によって横に落としたり手前に転がしたりと、現場の要望に応じてオーダーメイドで対応しています。切り出し方もパーツカウンターとして定数供給したり、個数を設定しないでフィーダーとして使用することも可能です。種類もワッシャーのほかに、ナットや球状のパーツ用に製作することもできます。パーツって結局はいろんなものを組み合わせて使うので、本来はこれを種類に応じて複数台入れるのが理想なんですよね。だからこそ1台当たりの単価を極力抑えて開発したので、員数管理で課題を感じている現場で役立てていただきたいですね。

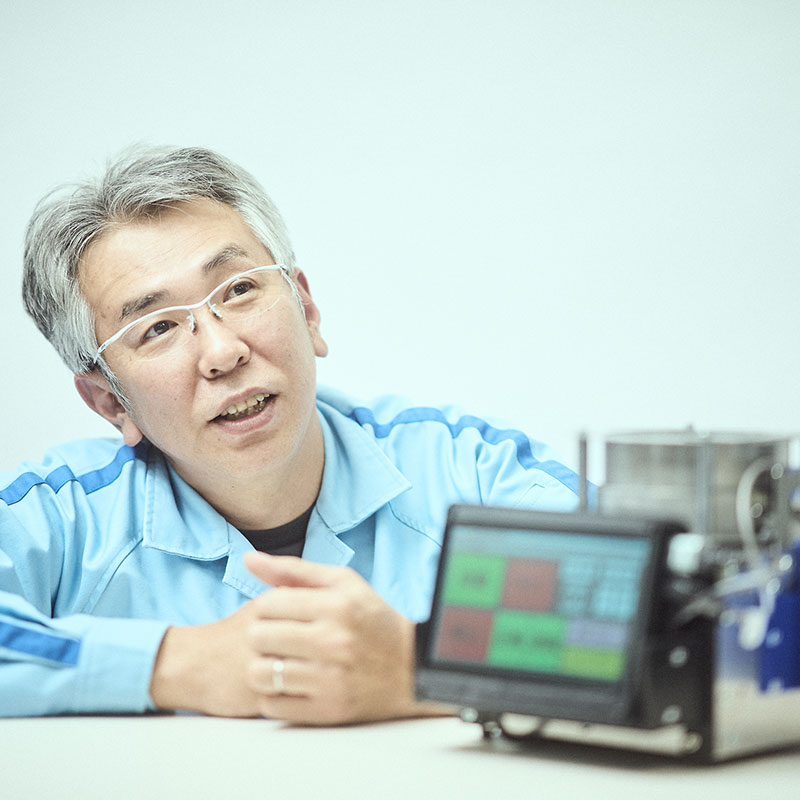