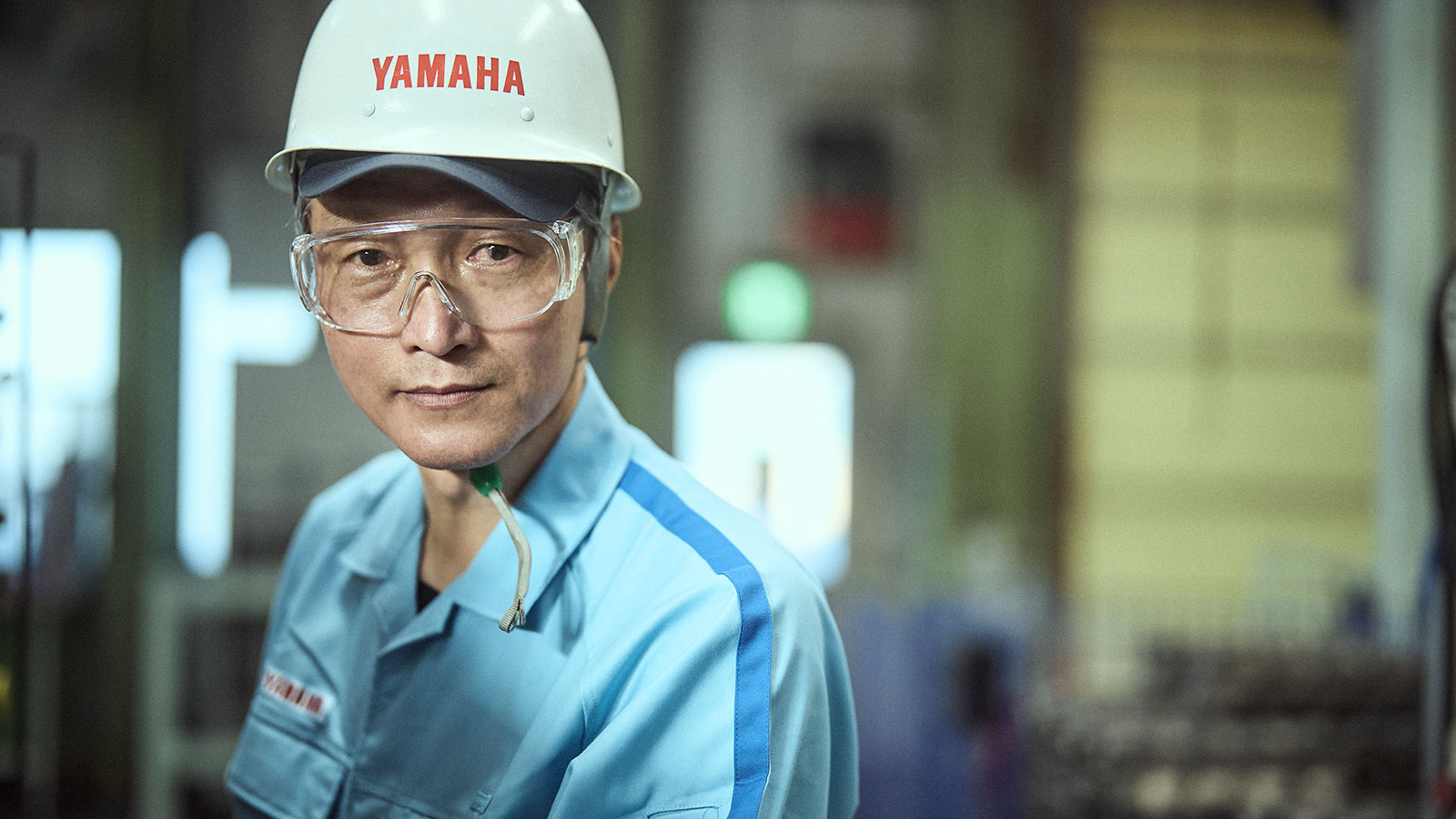
パフォーマー人財紹介
現場歴35年のベテラン、異色の開発エンジニアへ!
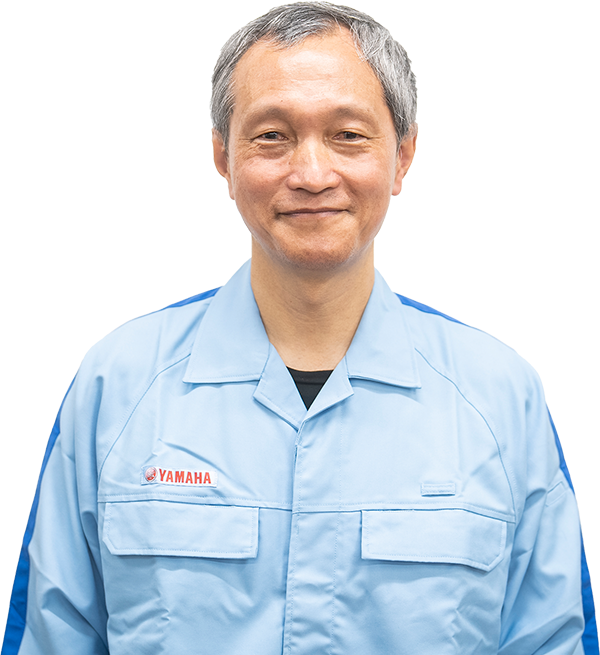
#02 大濱 吉基
1985年にヤマハ発動機に入社。モーターサイクルと自動車のエンジン組み立てを35年にわたって担当する。
2020年5月より生産技術本部 設備技術部 加工設備グループに配属され、6CBエンジンヘッドシリンダーのバリ取り自動化プロジェクトに参画。パソコン操作がほぼ未経験の状態からプログラミング、CAD等の技術を学び、同プロジェクトの生産移行までNCプログラムを担当した。趣味はサーフィンで身体を動かすことと、DIYで手を動かすこと。
キャリアチェンジは突然に
日本社会が空前のバイクブームに沸いていた1980年代。そんな時代のまっただなかに浜松市内の高校を卒業した大濱吉基さんは、バイクに憧れてヤマハ発動機に入社しました。早くお金を稼いでバイクに乗りたい、バイクをつくる仕事に就きたいーーそんな当時の若者らしい動機だった、と大濱さんは振り返ります。入社後は、加工が終わった部品でエンジンを組み立てる「組み立て職場」と呼ばれる工程のラインに配属されました。希望通りモーターサイクルエンジンの組み立てを18年間、そして配置換えで自動車エンジンの組み立てを17年間担当し、気が付けば大濱さんは組み立て一筋35年の大ベテランになっていました。
やがて50代に差し掛かり、大濱さんは自分のキャリアの終盤を見据えるようになります。というのもヤマハの製造現場には、50歳以上の男性と女性は10kg以上のものを持ち上げてはいけないという規定があったからです(50歳未満の男性は15kgまで)。これはケガや事故を予防するための労務管理上のルールでしたが、同時に自分の年齢を意識させられるものでもありました。「このまま健康を維持しながら、組み立ての仕事を定年まで続けられたらいいな」そんな期待のもとに大濱さんが描いていた未来予想図は、ある日突然上司から受けた呼び出しで一転してしまいます。
「2020年5月から部署を異動してもらう。バリ取りを自動化するプロジェクトが動いているので、そこに開発担当として参加してほしい」
「バリ取り」とは、溶かした金属を鋳型(いがた)に流し込んで部品を形成する鋳造(ちゅうぞう)の工程で行われている作業です。バリは鋳型の隙間に流れ込んだ金属が製品本来の形からはみ出して付着した部分のことで、現場の作業者はそれをグラインダーなどで削り取らなければなりません。この除去作業のことをバリ取りといいますが、組み立て一筋で働いてきた大濱さんにとって全く馴染みのない作業でした。
「鋳造職場にいた人よりも、別の職場にいた人のほうが固定概念がなくて新しい気づきがあるかもしれない、という理由らしいです。でもそんなことより "えっ、開発ってなに!?” と頭の中が真っ白になりましたね。パソコンの知識なんて皆無でしたから」
自宅にパソコンはあったものの、「インターネットでウェブサイトを見るためのツールでしかなかった」という大濱さん。当時、キーボードは左右の人差し指だけで打っている状態でした。上司からは開発の仕事をするために、パソコンの操作やプログラミングの知識を身につけるだけでなく、設備の図面を読めるようになり、バリ取りについて理解を深めてほしい、と告げられました。(こんなにたくさん新しいことを身につけるなんて、50歳を過ぎた俺にできるんだろうか・・・)大きな不安を感じながらも、大濱さんは最初の一歩を恐る恐る踏み出すしかありませんでした。
50代で迎えた大成長期
新たに加工設備グループへと異動した大濱さんは、新しいスキルを獲得するために猛勉強の日々を送りました。図面は組み立ての仕事でも触れてきましたが、開発ではより複雑で難易度の高い3Dの設計図も読めなければなりません。NC加工機(*1)を制御するためのプログラミング(NCプログラム)をはじめ、エクセル、パワーポイント、CAD等のソフトにいたるまで、すべてがゼロからのスタートです。社内講座やフレックススクールを受講しただけでなく、暇さえあればYouTubeで技術分野の解説動画を片っ端から視聴しました。
「”エクセルの図形機能を使いこなせばライン構成を図にできるよ”と上司に言われて、毎日いろんな絵を描いていた時期もありました。エクセルで絵を描くなんてお遊びみたいに聞こえるかもしれませんが、やってる方は真剣勝負でしたね(笑)」
*1:デジタル制御で高精度な切削加工を行う設備のこと
異動して3カ月が経過したころ、大濱さんは設備メーカーやプロジェクトの設計担当者との打合せに出席しましたが、飛び交う単語のほとんどが理解できませんでした。でも根気強く勉強を続けているうちに、インプットした知識が少しずつ線でつながり始める感覚があったと言います。そこからさらに4カ月が経ち、バリ取り設備が入る磐田南工場での会議に参加したころには、おおよその担当業務やバリ取り作業の内容を把握できるまでになっていたのです。
しかし技術知識やITスキルのほかに、もうひとつ大濱さんは克服しなければならないことがありました。それは、控えめで人付き合いが苦手な自分の性格。口下手で自分の考えをうまく周囲に伝えられず、それが原因で異動してから周囲と衝突してしまったこともあったそうです。
「思ったことをすぐに言えなくて、後になってから伝わったことで“どうしてその場で言ってくれなかったの!?”とぶつかってしまいました。新しい部署と人間関係に慣れてなくて、つい相手に遠慮しちゃったんですよね。そのとき“何でも言い合える関係を作らなきゃダメだ”と痛感しました。考えてみれば自分だって技術の知識がないのに年配だからと敬語を使われたり、遠慮されて居心地が悪い時もあるんです(笑)。だからいまは他のプロジェクトに行っても自分と話すときはタメ口でいいし、思ったことをどんどん言ってほしい、と伝えてます」
そんな大濱さんの奮闘ぶりを、同じ加工設備グループでサポートしながら見守ってきた沼島辰明さんはこう振り返ります。
「私はずっと技術分野で働いてきたので、大濱さんとは業務の知識と経験値にギャップがあり、それを埋めるために最初は苦労しましたね。でも大濱さんは非常に意欲的に勉強してくれていますし、わからないところは率直に伝えてくれるのですごくやりやすいです」
また大濱さんがコミュニケーション能力に自信を持てずにいたことも、「自分の方が年下ですけど、ちゃんと心を開いてくれて普通に雑談もしてますよ。“組み立て職場の方はこんな優秀な人をよく開発に回してくれたよね”と上司と話していたくらいです」と一笑に付した沼島さん。傍らでそれを聞いた大濱さんは、「ありがとうございます」と照れくさそうな表情を浮かべました。
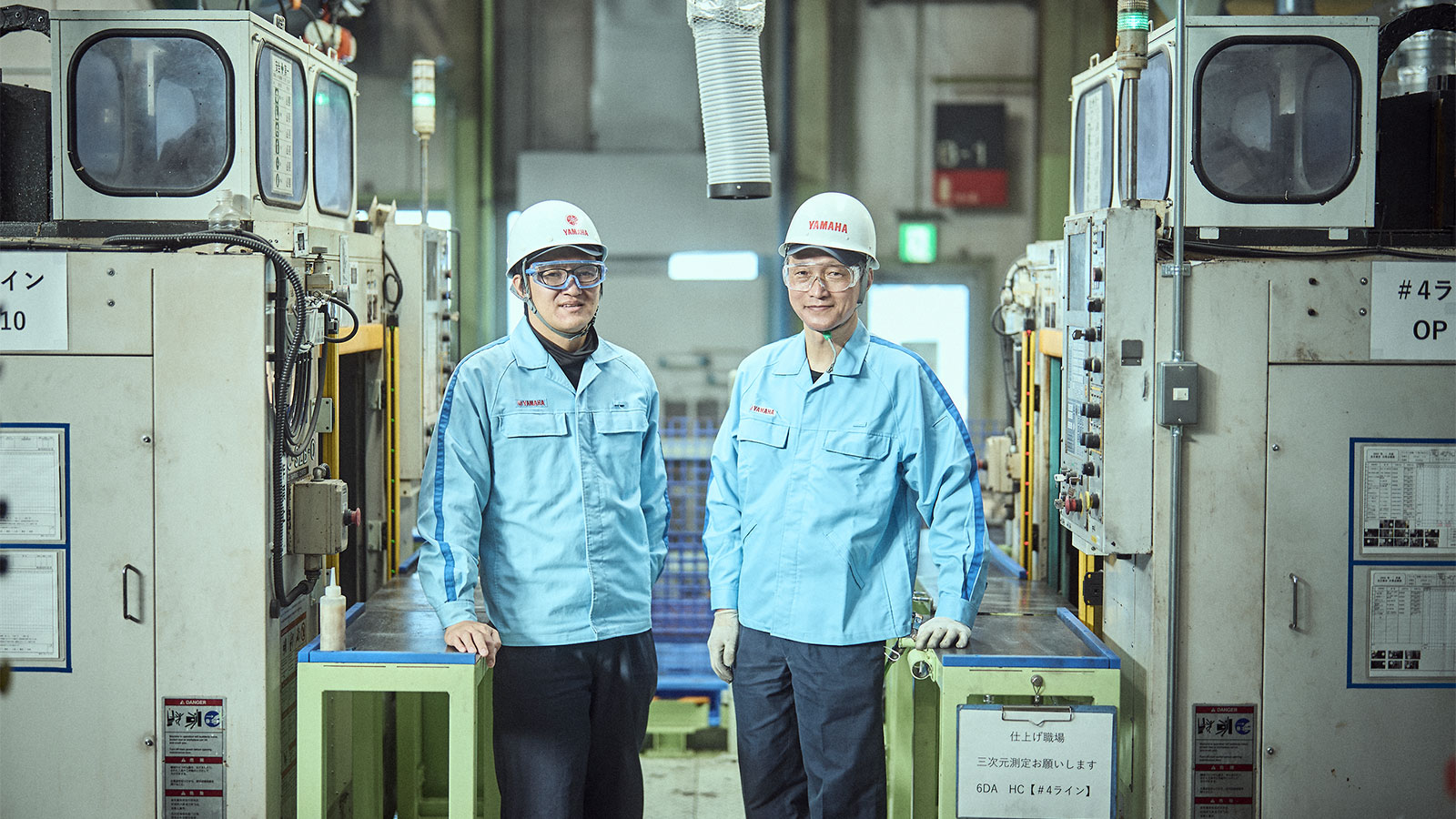
バリ取りをもっと早く、安全な作業に
このプロジェクトでバリ取り用の設備として導入されたのは、NC加工機の一種「マシニングセンタ」と呼ばれる設備です。自動工具交換装置(ATC)を備えていて、コンピューター制御で工具の交換から加工まで人の手を介さず自動で行うことが可能です。今回は6CBという船外機エンジンのヘッドシリンダーのバリ取りを自動化するため、沼島さんと大濱さんがマシニングセンタのプログラミングを担当することになりました。
沼島さんはプロジェクト立ち上げの経緯について、このように語っています。
「効率化とスピードアップが大きな目的ですけど、やはり人手がかかる作業を最小限にしたかったんです。というのも、バリ取りは一般の方が想像するよりずっと大変な作業ですから。小さなバリは手持ちの工具で取りますが、モノによっては10kg以上ある重たい鋳物を抱えて、大きなグラインダーや刃物に押し当てて削ることもある。作業によってはかなり危険を伴うので、労働安全性向上のためにも早急に自動化する必要がありました」
また実際のバリ取り現場を見学した大濱さんも、その必要性を強く感じたと言います。
「工場では全員ヘルメットとゴーグルを着用しますけど、バリ取り現場は粉塵が舞っているので防塵マスクと耳栓が必須です。金属の切り粉が肌に触れると痒みや痛みが出ることもあるので、肌が露出しないように首も手元も厳重に服で覆うように言われました。体力だけじゃなくて神経も消耗するし、とにかくキツイ現場だと思いましたね」
2人が書いたNCプログラムはソフト上で何度もシミュレーションされたのち、遊休機のマシニングセンタにコピーして、実ワークでさらに検証とデバッグが繰り返されました。自分が学んだことが実践で使いものになるのか不安で仕方がなかったという大濱さんですが、自分のプログラムで指示通りに製品が加工される様子を見て、やっと開発の仕事に楽しさを感じられたと語ります。
実機では切り粉が刃物に溶着したり、バリが干渉して製品がラフガイド(位置決めするための治具)に収まらなかったりと、新たな問題も発生しました。しかし地道な対策を重ねて2021年7月にはようやく生産移行を完了。その翌年には同じ設備をもう一つ追加するなど、現在も順調に稼働しています。
大濱さんは生産移行を機にプロジェクトを離れましたが、その後の成果をこう振り返ります。
「一番大きな成果は作業スピードのバラつきがなくなったことだと思います。この製品のバリ取りはラインのリーダーさんが担当して1台につき5〜6分、派遣さんでは7〜8分を要していました。いまはマシニングセンタを2台稼働して、だいたい1台を3分30秒。作業者に習熟してもらう必要もないので、教育コストも減らせていると思います。単純なヒューマンエラーもなくなりましたね。いまのところバリ取りの作業人員を約半数にまで減らせたそうです。現場に残った人の環境が、少しでも快適になっていれば嬉しいです」
エンジニアにとって技術より大切なこと
大濱さんを主に技術面でサポートしてきた沼島さんは、今後は同様のキャリアチェンジが製造現場では増えてくるのではないか、と推測しています。
「ものづくりにおいても、DXによる自動化・効率化の波がどんどん押し寄せていて、まだまだそれを支える人材が足りません。現場経験が豊富な方々をリスキリングして頭脳労働の担い手に転換していけば、より現場の事情に合った効果的なDXが可能になると思います」
そして大濱さんが開発という未経験の業務にうまくフィットした理由をこう分析しました。
「エンジニアにとって大切なのは、学びたい、知りたい、という好奇心です。大濱さんはそれをしっかり持っているし、そうやって好きなことを突き詰めていける人は何歳からでも伸びていけますよね。それに彼はものづくりが大好きで研究熱心な方なので、そんなところにも素養があったのかもしれません」
その言葉どおり大濱さんは、プライベートではものづくりを得意とするクリエイティブな一面を持っています。趣味の木工では自宅の家具を作り尽くしてしまったので、いまはレザークラフトに切り替えて財布やポーチ、キャンプ道具などを製作しているそうです。ここ1~2年は開発業務の勉強に明け暮れる日々でしたが、いまではそこで培った技術やITスキルが趣味の分野でも役立つようになりました。「開発でCADを使えるようになったので、自宅のパソコンにもソフトを入れたんです。レザークラフトもCADで図面を描き起こせるようになったので、作れるものの幅が広がってきましたね」そう語る笑顔には、もうすっかりエンジニアとしての風格がにじんでいました。