パフォーマー人財紹介 #04
現場を変えるため、自分自身を変えていく
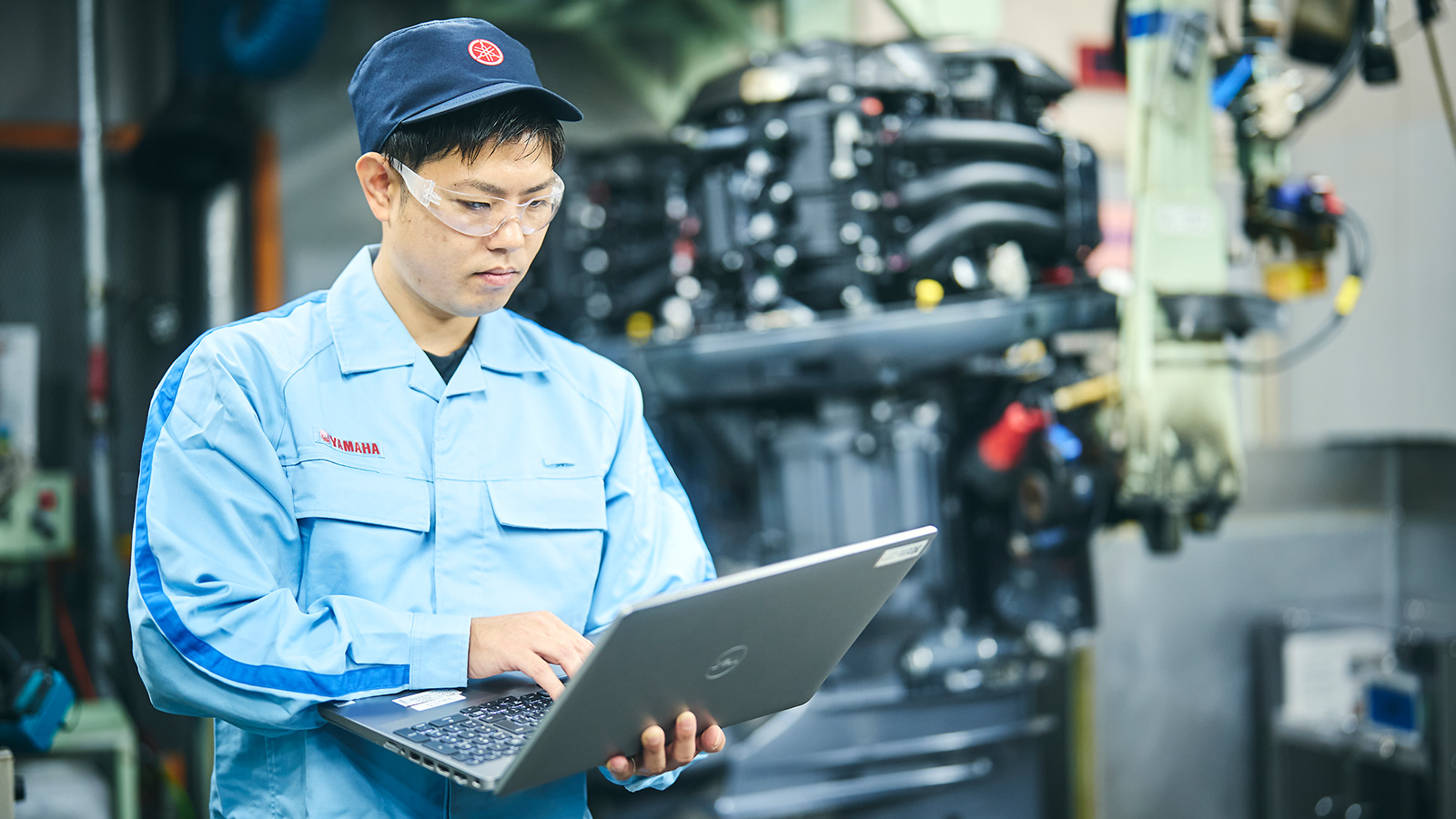
パフォーマー人財紹介
現場を変えるため、自分自身を変えていく
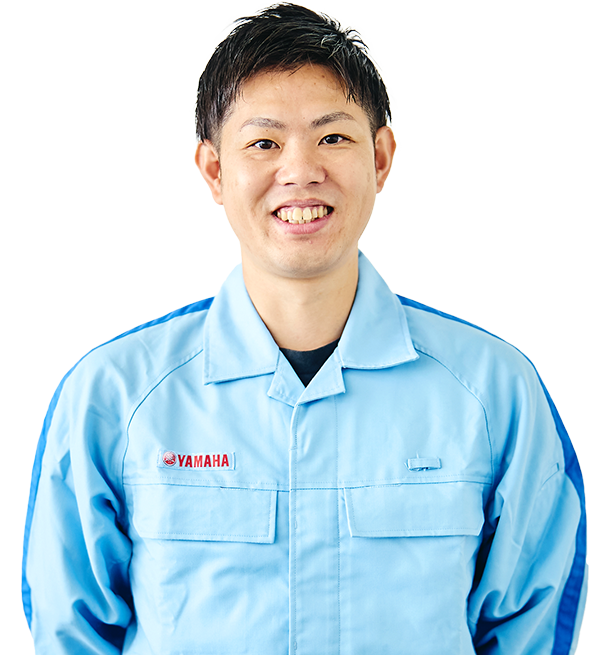
#04 岡本 守央
2009年にヤマハ発動機に入社。本社の組立工場に配属され、トヨタ自動車向けのエンジンの組み立てを担当する。現場での経験からもっと大規模な改善に携わりたいと、2020年に生産技術本部 生産技術部に異動。知識ゼロの状態からプログラミングを学び、さまざまなシステム開発の実績を積む。2024年1月には開発を担当した袋井南工場向けのパワーチルトの異音判定装置が導入された。高校時代はバスケットボールに熱中し、インターハイ出場経験もあるスポーツマン。
大学との共同研究で生まれた最新技術を、ものづくりの現場へ
ヤマハ発動機と静岡大学は、イノベーションの創出や人材育成を目的として産学連携協定を締結しており、近年さまざまな先進技術の共同研究を行っています。さらにヤマハ発動機社内においても、共同研究で得られた知見を活用して、現場課題を解決しようという取り組みが進んでいます。
その事例のひとつが、2024年1月に袋井南工場で導入された「船外機パワーチルトの異音判定装置」です。船外機はボートの推進機として漁船やレジャーボートなどで幅広く使用されていて、袋井南工場では中型・大型馬力の船外機を生産しています。パワーチルトとはボートが浅瀬や海岸付近を航行したり、係留または陸揚げする際、船外機を上げ下げするための装置のことで、モーターや油圧シリンダーで構成されています。
そのパワーチルトに関して、3~4年前から「作動時に異音がする」というクレームが寄せられるようになりました。その数は平均して年2回と頻度は非常に低かったものの、社内でこのクレームへの対策をとろうという取り組みが始まります。そこで開発されたのが、前述のパワーチルトの異音を判定する装置でした。音声を解析して画像変換し、AIが異音を判定するこのシステムは、静岡大学と共同研究した音の分析技術がベースになっています。
この開発を担当したのが、生産技術部の岡本守央さんです。彼は2020年に生産技術部に異動するまでは、組立工場で10年以上現場に立って働いていました。今回のテミル:ラボは、未経験の職種に自ら飛び込み、わずか数年の独学でシステム開発を手掛けるようになった異才のエンジニア・岡本さんにお話を伺います。
「現場を変えていくために、現場を去る」という決意
岡本さんは2009年にヤマハ発動機に入社しました。トヨタ自動車向けエンジンの組立工場に配属され、最初はクラウン向けV6エンジンの組み立てからスタートしたそうです。11年間の現場勤務を経て、岡本さんは製造ラインの業務やスタッフを取りまとめるラインキーパーへと昇格していきました。
その後も同じ職場でキャリアを築いていけば、いずれリーダーや職長というポジションも視野に入っていたことでしょう。ところがある日、岡本さんは「異動させてほしい。もっと現場の根本的な改善に関わる仕事がしたい」と上司に申し出ました。
「現場の方はたくさんの困りごとや不便さを抱えています。でもそれを解決したくても、自分たちの裁量でやれる改善は、小規模かつ低予算なものに限られているのが現状です。作業台を作ったり、工具の置き場所を工夫したりする小改善はできても、作業時間が少し短縮できるだけで、彼らの課題は解決できません。本当に必要とされているのは、人がやると間違いやすい、あるいは負担になることを機械化・DX化するような、もっと大きな改善ではないでしょうか」
じつは組立工場での勤務時代、岡本さんにとって忘れられない出来事がありました。担当していた製造ラインで、オペレーターがエンジンのシリアルナンバーを入力ミスするという不具合が発生したのです。金属製のエンジンに打刻されたシリアルナンバーは読み取りづらく、オペレーターは長い桁数の番号をテンキーで手入力していました。ミスを誘発しやすい作業環境に対して、岡本さんは「そもそも人がやるには間違いやすく非効率な作業です。カメラを入れて読み取ればミスもなく、効率も良いのでは」と考えました。しかし当時の自分の技量では、その発想を形にできないもどかしさがあったといいます。
「これだけデジタルが発達した時代なので、それらをうまく使うことができれば現場をより良くする方法を生み出せるはず。でも、いまの自分にはまだ専門的な知識が足りない、と感じていました」
技術と知識が足りないために、思うように現場を変えられないもどかしさ。あきらめてたまるかという反骨精神。さまざまな思いが交錯した結果、岡本さんがたどり着いたのは自分自身が変わること。それが異動の申し出だったのです。
「何をやってもいいよ、やりたいことを仕事にしよう」
パソコンには全く詳しくなかったという岡本さんでしたが、その熱意が評価されて生産技術部に異動したのは2020年のこと。最初に驚いたのは、「何かやりたいことはある?」と上司から聞かれたことでした。
「現場にいたときは仕事は与えられるものだったので、そんな質問をされた経験がなかったんです。だから正直に『何をやらせてもらえるんですか?』と聞いたら、『何をやってもいいんだよ』と言われました。嫌な仕事を担当しても途中でやりたくなくなるから、まずはやりたいことを仕事にしよう、とおっしゃってくれたのが印象的でした」
そこで岡本さんは早速プログラミングの勉強を始めました。特定の案件という目的があったわけではありませんが、学び始めたことでさまざまな知識がつながり、デジタル領域への理解が徐々に深まっていったそうです。その後はエンジニアとして案件を受け持ち、システム開発を担当するようになりました。そこでの実績が評価されてアサインされたのが、前述の「パワーチルトの異音判定装置」だったのです。
「このシステムでは、マイクで取得した音を周波数分析にかけて、その周波数帯をスペクトログラムに変換します。その変換した画像データをAIに読み込ませて、OKパターンとNGパターンを学習させます。その学習したものをベースに、実際にラインで流れてきたパワーチルトを作動させて、製品の作動音から異音の有無を判定させているんです」
この案件で、岡本さんはAIの開発とチューニングを全面的に担当したほか、製造ラインとの連携システムやトレーサビリティの開発を担いました。チューニングとは、AIが学習するための入力データやパラメーターを調整したり修正する作業のこと。これらの設定が適切でなければ、AIはうまく性能を発揮することができません。判定の精度向上の鍵となる重要な作業を担うことになった岡本さんは、AIの技術領域だけでなく、「音」に関する学術的な勉強にも取り組みながら開発を進めていったのです。
「異音づくり」でAIを支えた、もうひとりの功労者
このシステムを開発するうえで、もうひとつ重要なミッションがありました。それは、AIに学習させるための音声パターンの集積。それらを実務面で支えたのが、マリンエンジン製造部 品質技術課の高林亮介さんです。
「私が所属する品質技術課では、お客さまのところで使用を開始して10時間以内に発生する不具合を『短時間不具合』と定義して、これをなくすための活動を行っています。パワーチルトの異音案件は、その一環で取り組むことになりました。異音に対する人の捉え方はバラバラで、個々の感覚で左右されることも多いんです。ベテラン検査員でも正常品と聞き比べて判定できるレベルで、聞く人によっては違いが微妙すぎて判別しづらいこともあります。人の感覚に頼らず、誰でもOKかNGか判定できるようにする、というのが今回のシステムのコンセプトでした」
高林さんはパワーチルトメーカーの技術者や、自社の品質保証部門とも協議を重ねて、パワーチルトの機種や不具合の原因を検討しました。その結果、異音はすべてAラインで製造される大型機種に限定されていること、そして異音の原因の9割はモーターが原因で、なかでもモーターまわりのマグネットにクラックが入ることが最大の要因であることがわかったのです。
ところが異音の最大要因が特定できても、年間で約2000台の船外機が生産されているAラインで、年に2回の頻度で起こる異音を集めることはほぼ不可能です。そのためAIに学習させる異音のサンプルは、疑似的に作り出すしかありません。そのために船外機を分解して、パワーチルトのモーター周辺のマグネットを破損させ、異音の出る状況を何パターンも作りだすことになりました。そして再び船外機を組み上げて音を測定し、NG品のデータを集積するというこれらの作業は、すべて高林さんが一人で担当したそうです。
「いろんなパターンの異音を作り出しては岡本さんにAIの学習を依頼し、岡本さんからは学習させた後のソフトを戻してもらい、再度判定してもらう。これを何度も繰り返しました。異音の捉え方は個人差があると言いましたが、このシステムで画像化されたものを見れば一目瞭然です。システムは今年の1月に導入されて10カ月以上運用していますが、これまで明確なNG判定が出たり、市場で異音の不具合が発生したことはありません」
今後はAラインを通るすべての機種に異音判定装置を横展開するために、岡本さんと高林さんは既に準備を進めています。また現在運用中のシステムは、判定で使用する音を保存し、検査履歴のエビデンスとしてデータベース化するための改良工事とシステム開発が予定されているそうです。
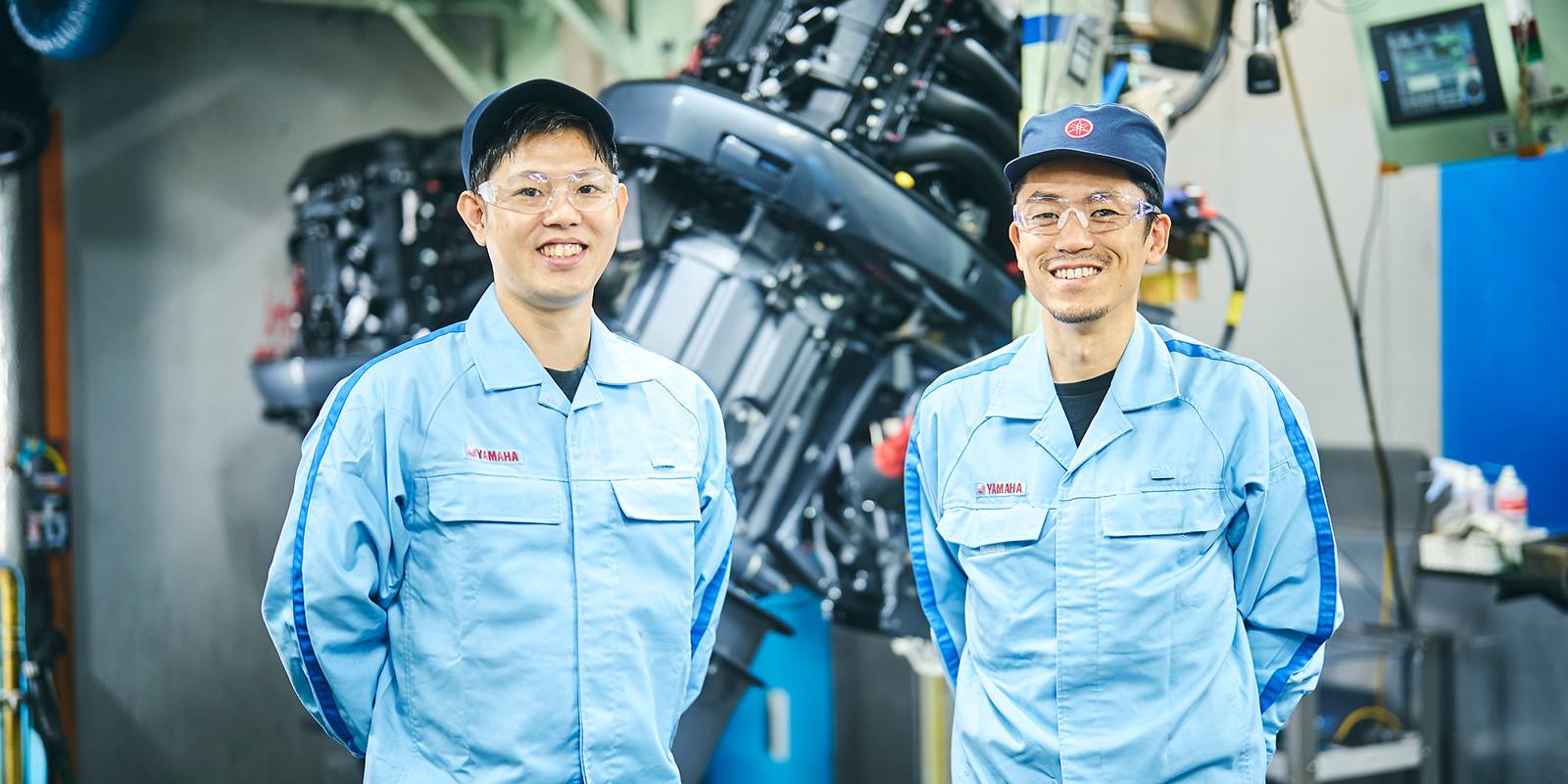
どれだけ学んでいけるか。すべては自分の努力次第
このシステムが現場導入されるのと時を同じくして、2024年1月に岡本さんは生産技術部のプロセス先鋭グループに異動しました。研究開発中の技術のなかでも文字通り先鋭的なものを扱うこのグループでは、検証して確立させた技術をシステムに落とし込み、現場に移行する役割も担っています。
「学術的な知識がないので、いまだに同僚や研究員が話す技術用語についていけないときもありますよ。日本語なのに全然意味がわからなくて、あとで調べまくってます(笑)。どんな経歴の人でも、がんばって勉強すれば学術的な知識は身についていきますし、環境よりも自分の頑張り次第だな、と感じています」
そんな少数精鋭のチームに抜擢されて働いている現在の立ち位置を、ご自身はどのように捉えているのでしょうか。
「どうして上司が自分を引き抜いてくれたのかは、正直に言ってわかりません。ただ現場にいたのに技術を学んで、たった数年でここまでやって来れた、というところを評価してもらえたのかもしれませんね。同時に『君はもっとエンジニアとして技術を磨いていけるよな、もっとやれるよな』という期待も感じています」
そんな岡本さんは現在、大きなプロジェクトを2つ同時に進行しています。
「ひとつはデジタルツイン(※)を活用して設備導入を検証するシステムの開発です。グローバル化が進むいま、世界各拠点において生産性の高い設備開発が急務となっています。デジタルツインを用いることで、素早く検討を行い効率的に設備導入を進めることができます。
2つ目は、アルミニウムの廃棄を遠隔操作で機械化するシステムです。ヤマハ発動機の工場では未だに3Kを伴う大変な職場があります。遠隔化など新しい技術を使うことで、現場の人を3Kから解放をしたいと考えています」
昔の自分が現場で叶えることができなかったさまざまな改善を、いまの岡本さんは違う立場から力強く後押ししているのです。
※現実空間の、ヒト・モノ・コトのさまざまなデジタルコピーをサイバー空間上に表現する先進技術
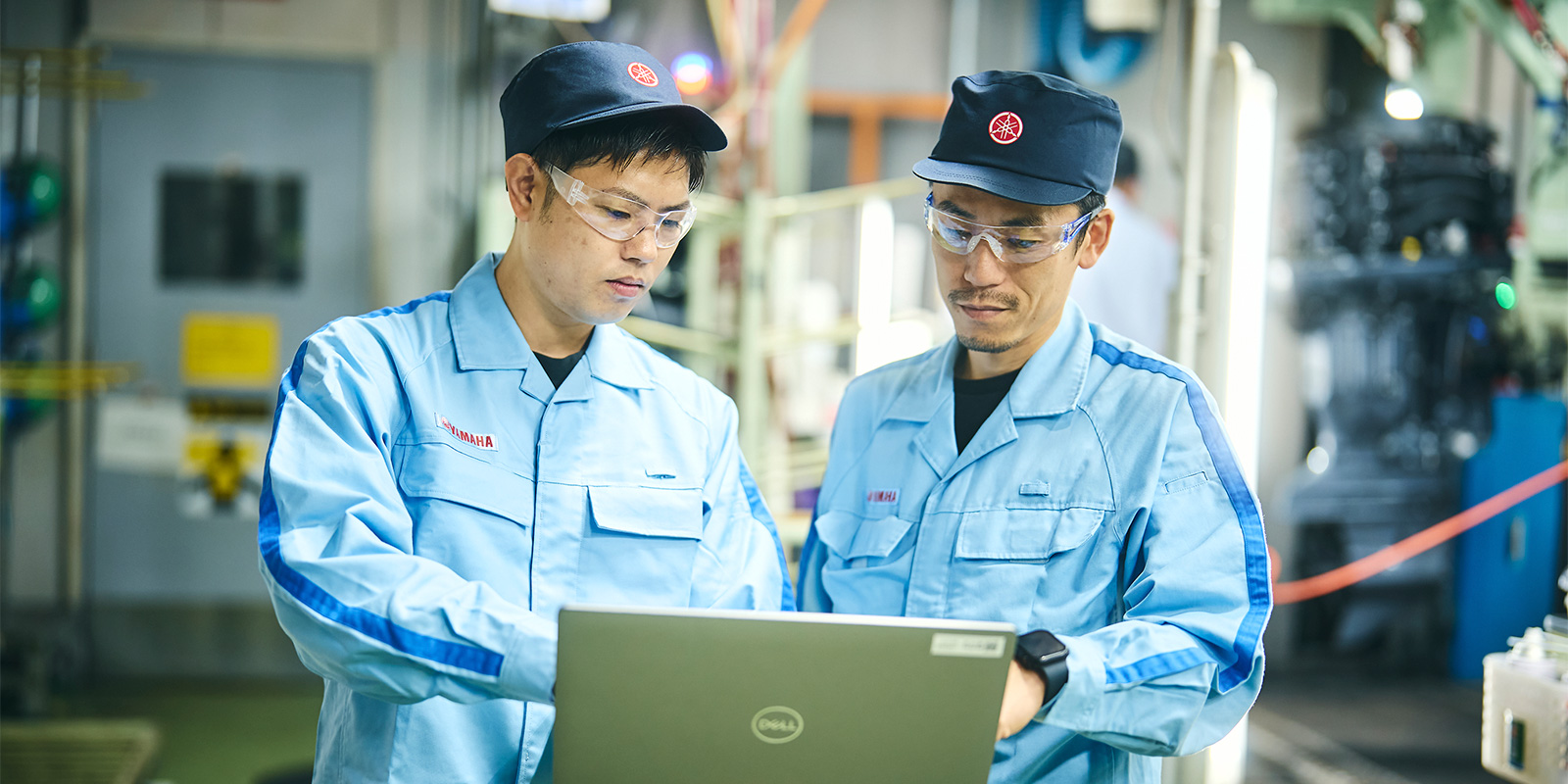