閃きプラットフォーム開発レシピギャラリー
Recipe 6 ローコスト自働組立機
開発のポイント
- 1 これまで紹介してきた開発レシピを組み合わせて、船外機部品の自働組み立てを実現
- 2 フィーダーには特殊な形状のパーツを最適な姿勢に整える「水平循環コンベア」を搭載
- 3 3台のPLCをネットワーク接続することで、複数のシステムを連携させて制御
これまでのレシピでは、ねじやボルトなどのパーツを適切な姿勢に整えて定数供給する単機能設備を紹介してきました。それらの設備を掛け合わせることで組み立て作業を自働化したのが「ローコスト自働組立機」です。パーツ単体の切り出しを自働化することはできても、それらを使って1つの中間部品へと組み立てるには、複数のシステムを連動する高度な制御が必要です。それがシステム全体の高価格化につながり、現場導入するうえで高いハードルになっていました。このレシピではヤマハ発動機製スカラロボット2台と高性能2Dカメラ、そしてFAチーム(*1)オリジナルのパーツフィーダーを使った自働組立機を独自に設計。それぞれを制御する3台のPLC(*2)をネットワークで接続して、各設備を複雑に連携させています。フィーダーで切り出した6種類のパーツを1つの中間部品へと組み立てるほか、完成品を払い出すまでの全工程を自働化しました。
*1:「テミル:ラボ」プロジェクトを主導的に進めているチームのこと
*2:製造設備などのシーケンス制御を行う装置
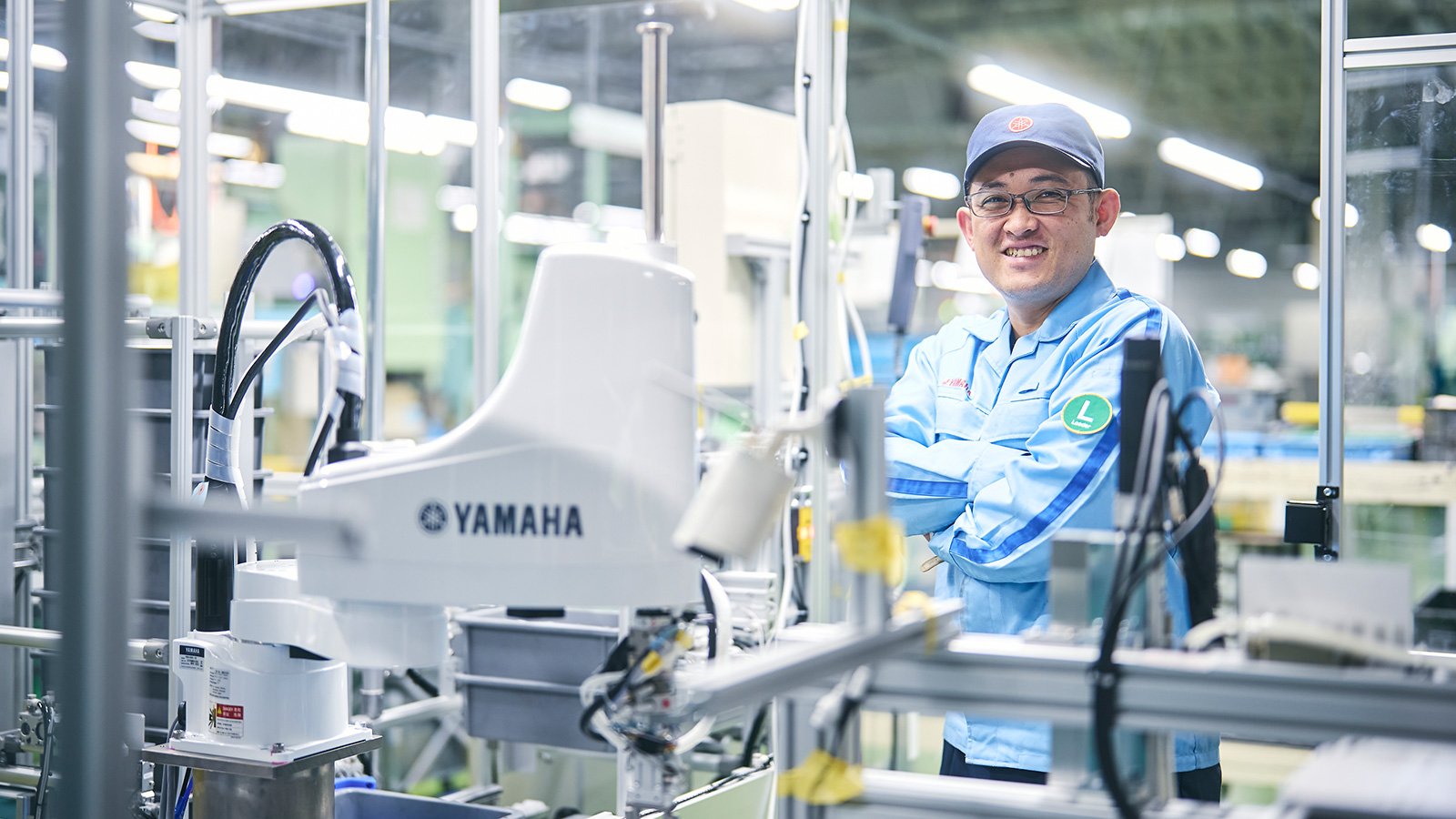
現場の声
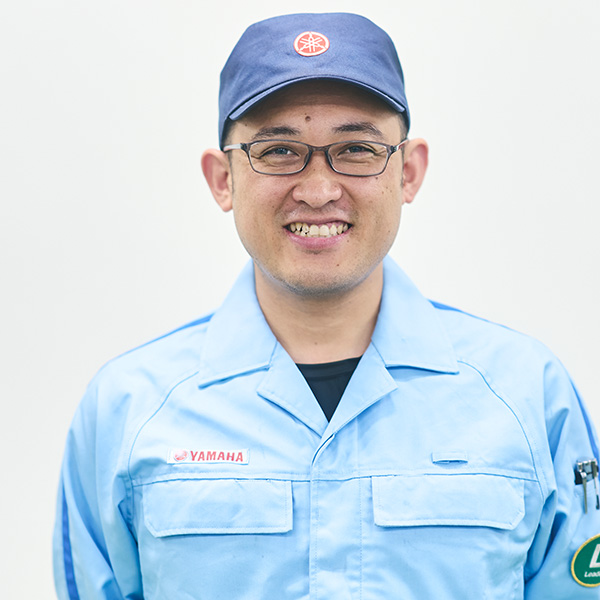
梅田 浩介さん
ヤマハ発動機株式会社
磐田南工場
磐田第3製造部生産4課 第一工区
どこに導入しましたか?
船外機エンジンのヘッドシリンダーに取り付けるアノードカバーの組み立てを自働化するために導入しました。アノードカバーは6種類のパーツで構成された中間部品で、それぞれのパーツは自働的に設備の中で切り出されています。組み上がったアノードカバーは1箱20個入りを3段積みにして排出され、それをラインキーパー(担当するラインに必要な部品を運搬して供給する作業者のこと)が各ラインに運んで次の工程に流しています。
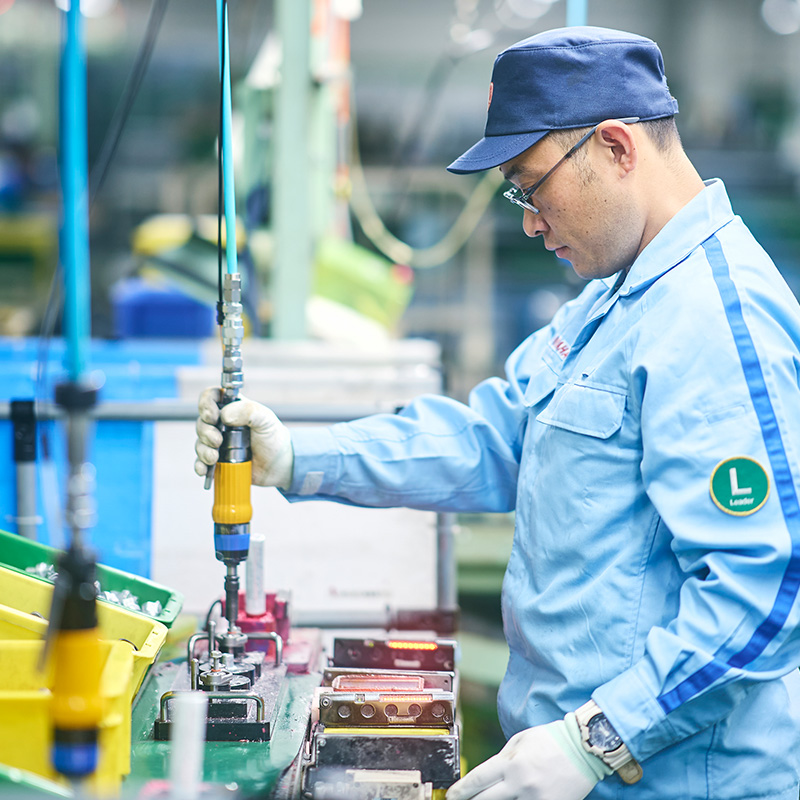
どんな課題がありましたか?
ここは船外機のヘッドシリンダーのサブ組み立てを行っている職場で、作業の大半が人の手で行われています。生産効率を高めて残業を減らすためには、作業の自働化に取り組む必要があるのはわかっていました。しかしこの職場は長年にわたって「人の手作業が中心であることが当たり前」という環境だったので、どの作業が自働化できるのか誰も見当がつかなかったんですね。そこでFAチームの方に職場まで来ていただき、実際の作業工程を見学してもらったのです。技術者目線で見ると自働化できそうな作業はいろいろあったそうで、いくつか設備を提案していただきました。そのなかから手始めにアノードカバーの組み立てを自働化することにしたのです。
ここは特にヒューマンエラーが多い工程というわけではないのですが、ヘッドシリンダーにアノードカバーを1つ取り付ける機種もあれば最大で4つ取り付ける機種もあったりと、1日の所要量が変動することがネックでした。手作業のときは作業者を増減したり残業で対応していたのですが、自働化すればシステムの設定に任せられるのではないかと考えたんです。
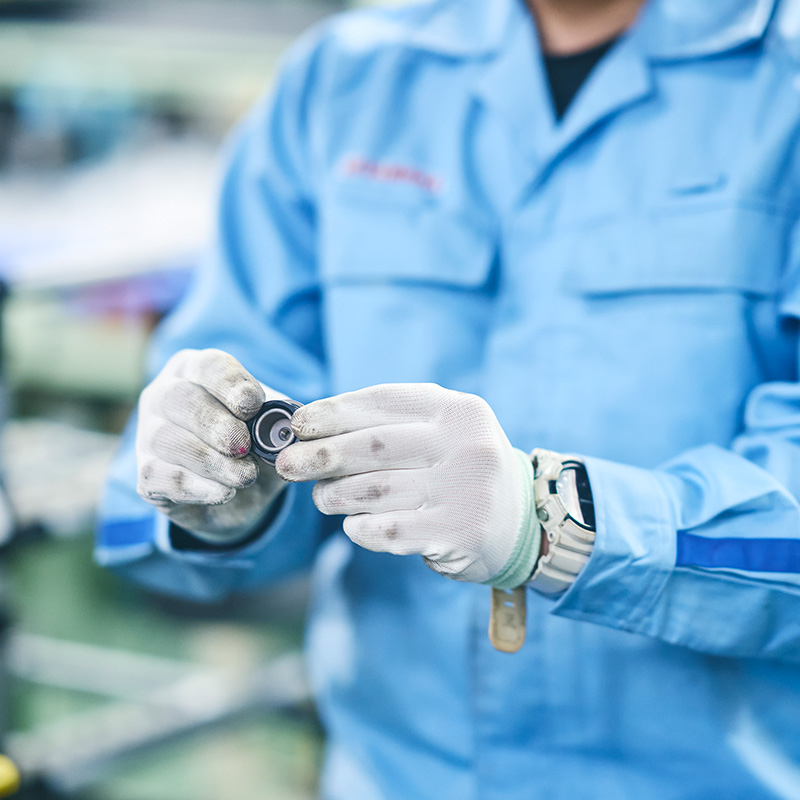
現場に最適化するためにどんな工夫をしましたか?
このシステムでは、現場に合わせて以下の組み立て工程が自働化されています。
①コンベアからカバーアノード(アノードの台座となる部分)を拾い上げる
②グロメット(黒いリング状のゴムパーツ)を装着する
③裏返して下からアノードをセット
④ボルトに緩み防止の接着剤を塗布して頭部にインクで印をつけ、ガスケットを装着
⑤上から④のボルトを締めてアノードとカバーを組み付ける
⑥後工程で使用するための組み付け用ボルトを通す
⑦組み上がった部品を箱に詰め、1箱20個入りを3段積みにして排出する
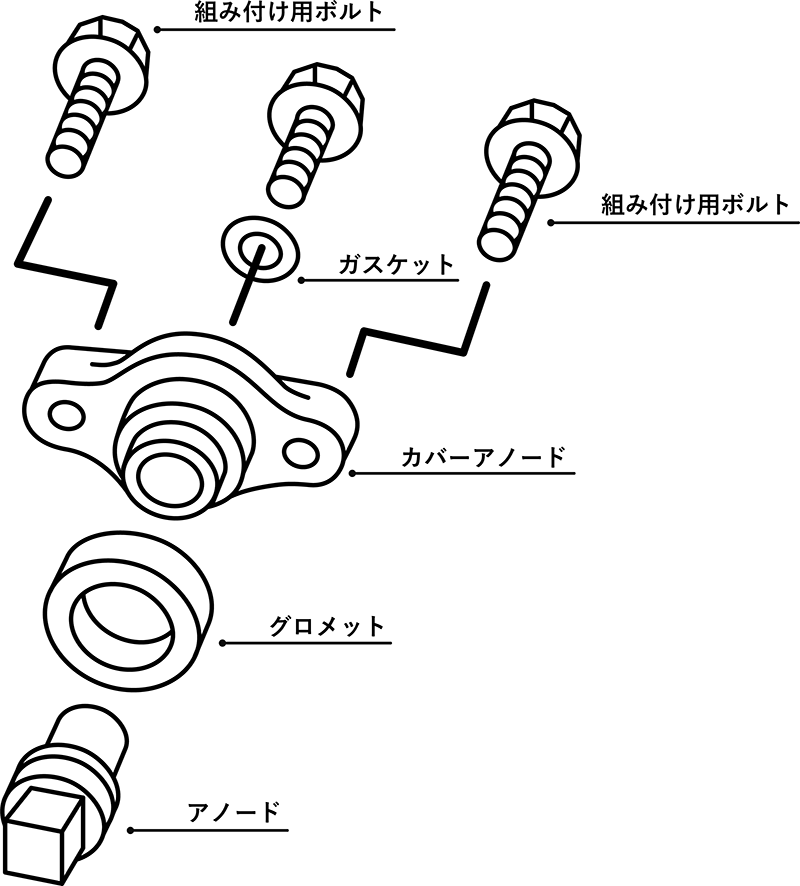
FAチームにリクエストしたのは、まずは品質を維持してほしいということです。これまでは作業者がインパクトドライバーでボルトを締めていましたが、設備ではナットランナーが自働で行います。万が一ボルトが斜めに入ったり、極端なケースでは締め忘れがあったときに、ちゃんと設備が検知してはじいてくれるのか。あるいは締め付けトルクが低くなったり強くなったときも止まってくれるのか。不良の検知については細かく要望を出して、設備内のさまざまなところにセンサーを設置していただいてます。
次に、1日に2000個の生産目標を達成してほしいということです。具体的には1箱20個入りを5分、1個当たり約15秒を作業スピードの目標に設定して、かなり近い数字を実現していただきました。そのうえ手作業の場合は①②⑥の工程を他の作業者が担当していますから(①②はカバーアノードとグロメットの取り付け作業を事前に行ってストックを用意しており、⑥の組み付けボルトはラインキーパーが取り付ける)、作業領域が広がったことでより多くの人の負担が軽減されることになりました。
最後にこれが一番重要なことですが、現場移行されたあと自分たちで安全にメンテナンスを行える設備であることを希望しました。現在はシステムについて私を含めて数名で勉強しているところです。操作系のインターフェースもシンプルでわかりやすく作っていただいたので、これまでシステム関連に馴染みのなかった自分でも扱いやすいと感じています。
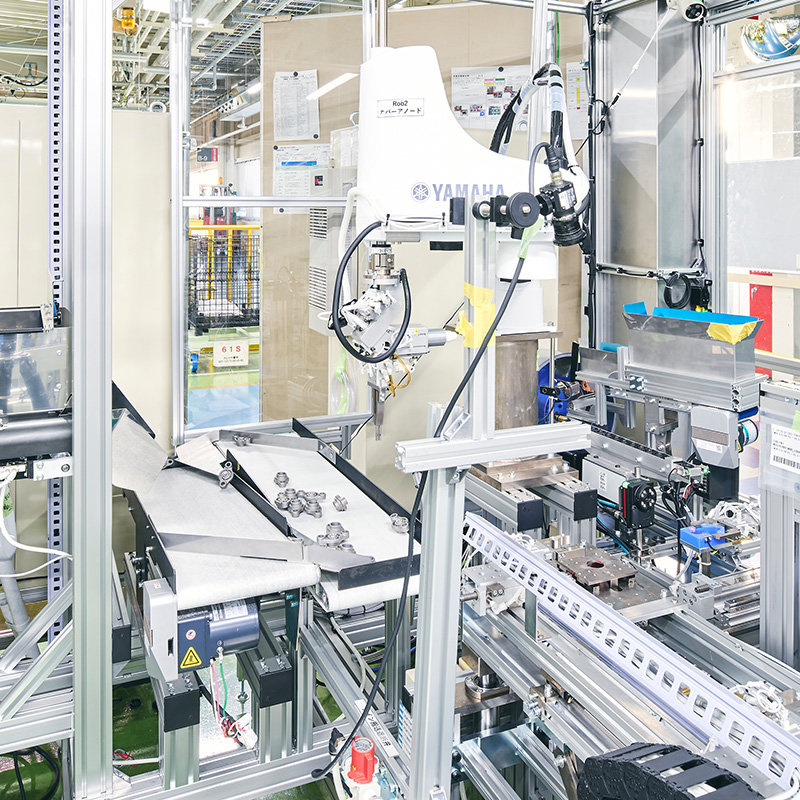
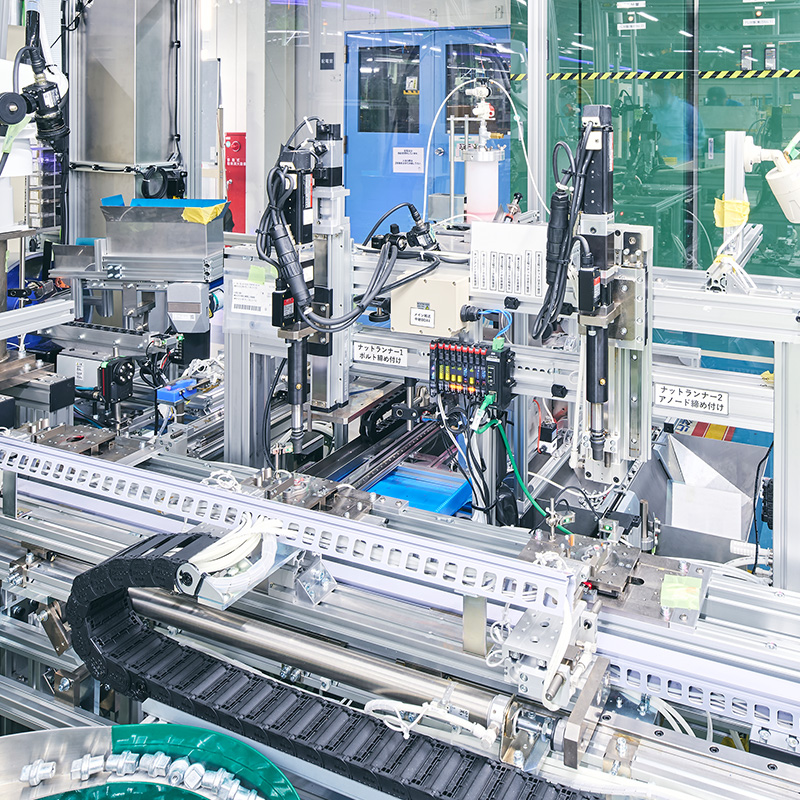
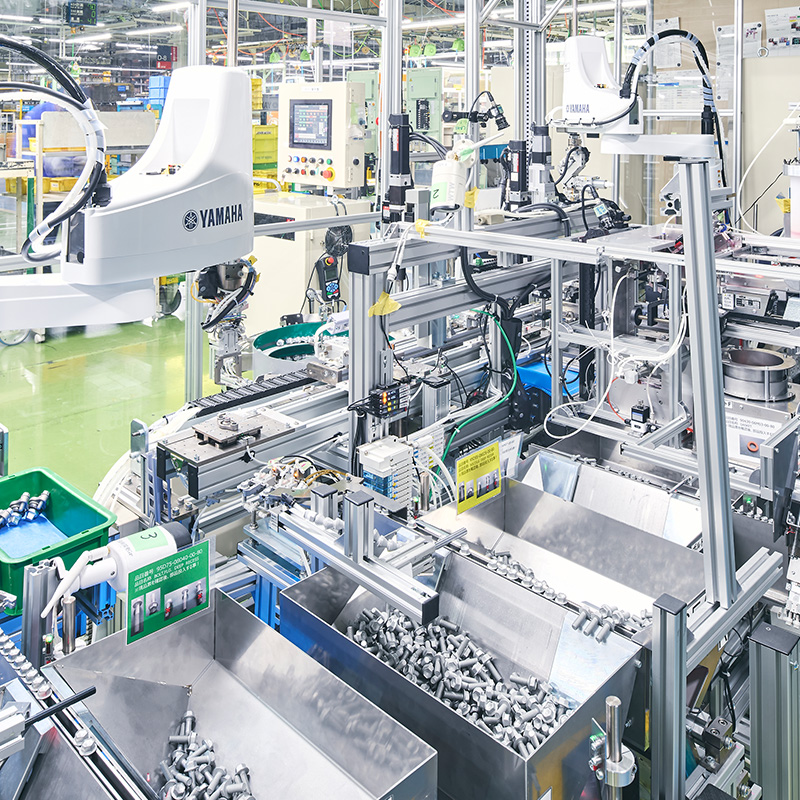
どんな効果を期待していますか?
この設備はもうすぐ最終的な安全認証を受ける予定で、本格的な稼働はもう少し先になります。いまは移行期間として1日の必要数2000個のうち自働組立機で500個、手作業で1500個を並行して組み立てている状態です。具体的な改善効果は設備で1日2000個を生産できるようになってから検証しますが、既に現段階で1週間に8時間の残業を削減することができました。浮いた時間は新たな仕事の教育に充てられますし、作業者の方々も新しい仕事を覚えられるのでモチベーションが上がると喜んでいます。
また副次的なメリットとして、職場のみんなが機械化に興味を持ってくれるようになりました。この設備は機械の動きがよく見えるので、そこからいろんなアイデアが湧いてくるみたいです。先日もあるオペレーターの方が「自分たちの作業の一部を自働化して改善できないか」とアイデアを出してくれました。みんなに少しずつ「自分たちの職場でどんどん新しいことに取り組んでみよう」という気持ちが芽生えてきているのがうれしいです。
今後の展開としては、自働組立機とヘッドシリンダーの効率的な作業動線を作りたいと考えています。現在はヘッドシリンダーとアノードカバーが別々の動線でラインに送られているので、それらを一本化するのが目的です。自働組立機の場所を移設し、ヘッドシリンダーにアノードカバーを組み付けてからラインに流せば、モノの流れもシンプルになるしライン内の作業を1つ軽減できます。組み立て作業の自働化を進めながら、モノの流れとラインをより効率的に連動させれば、さらに大きな改善につながるのでは、と期待しています。
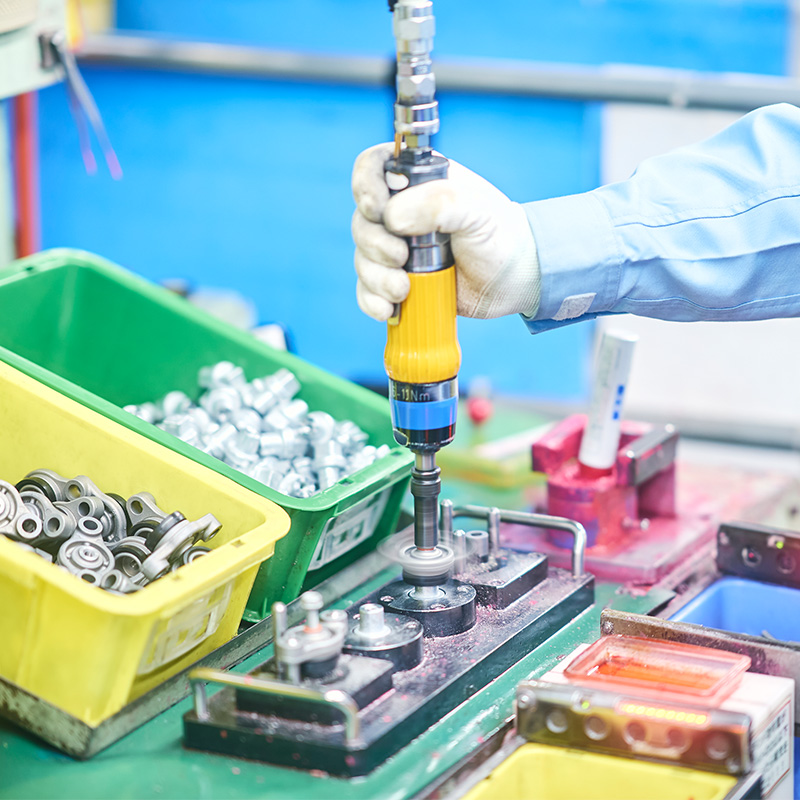
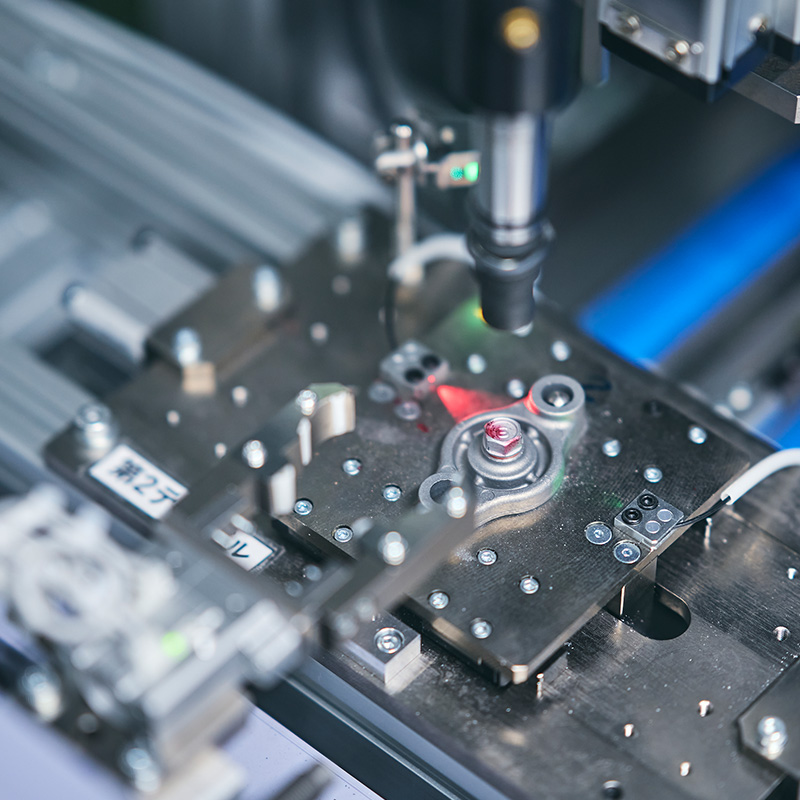
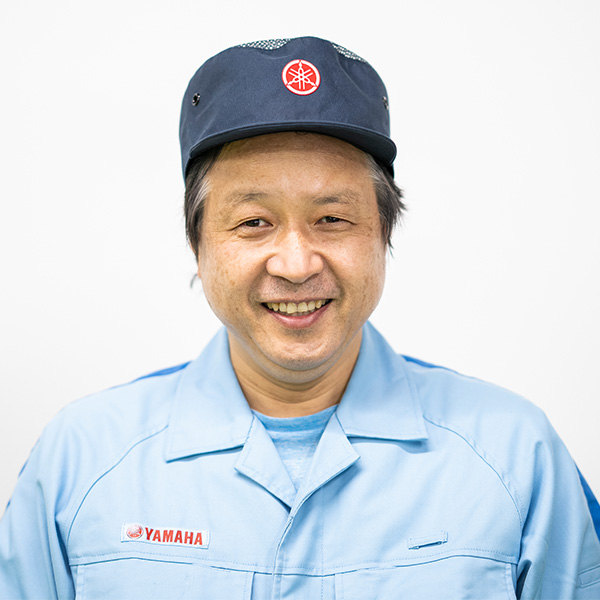
小曽 勉さん
ヤマハ発動機株式会社
FA技術開発グループ
開発者の声
これまでのレシピで紹介してきた単機能のパーツフィーダーを組み合わせて、中間部品の自働組立を可能にしたのが今回の設備です。まず台座となるカバーアノードを1台目のスカラロボットが拾い上げますが、Recipe2と同様に高性能カメラが2D画像で形状を認識しています。このパーツはボルトやガスケットより大きく、非対称でやや複雑な形状をしているため、フィーダーに2つの短いコンベアでパーツを動かす「水平循環コンベア」を開発しました。片方のレーンは水平に、もう片方のレーンは緩い傾斜をつけることで、パーツが高低差を転がって姿勢がうまく整います。一般的なボール型フィーダーよりシンプルかつ安価に、そして省スペースに収めることができました。
コンベアと全体の機械設計は私が担当しましたが、この設備ではさまざまなパーツを切り出して組み上げていくため、複数の技術者とチームを組んで製作しました。これまで「テミル:ラボ」で紹介してきたオリジナルのパーツフィーダーがベースになっているため、一般的な自働組立装置や産業ロボットと比較してかなり低コストに仕上げることができています。
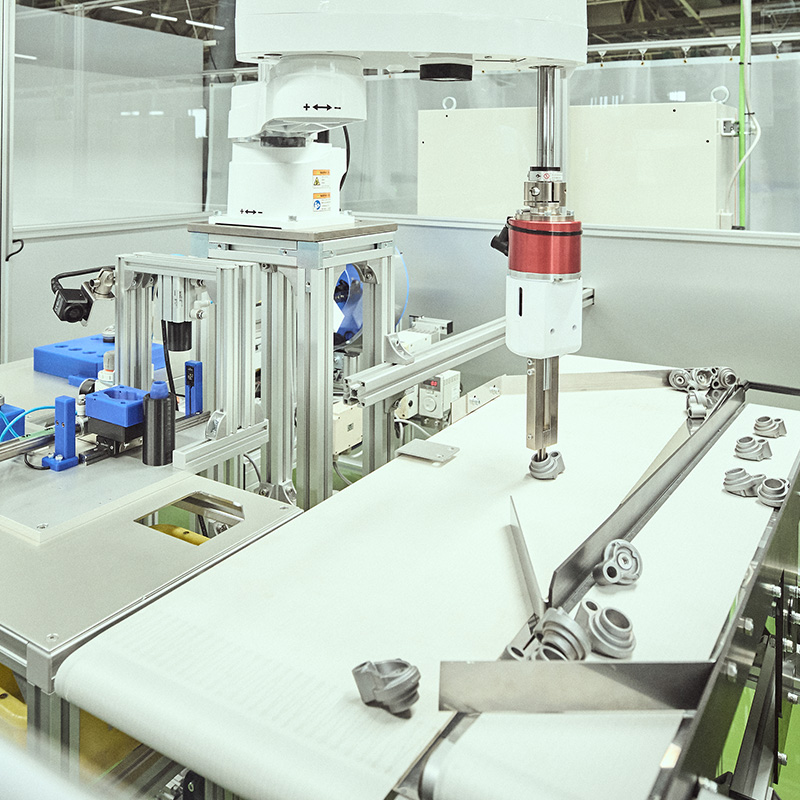
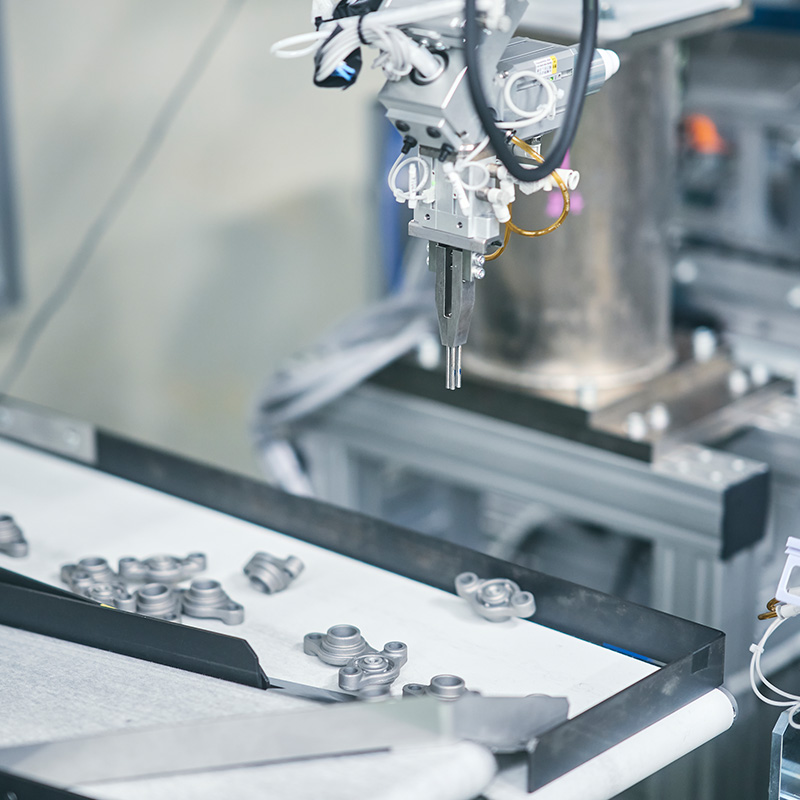
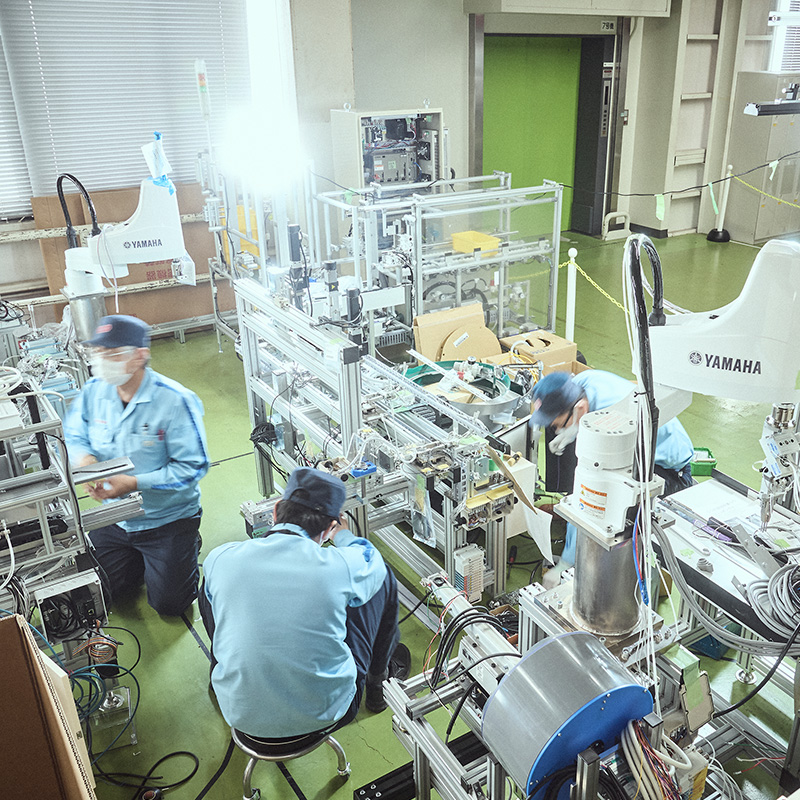
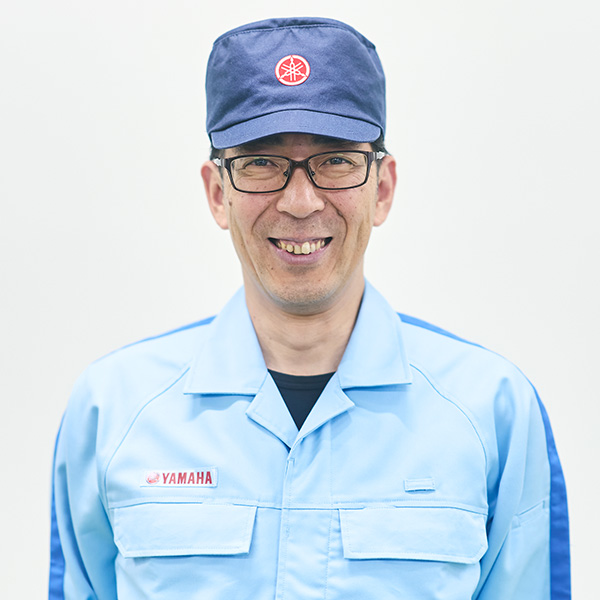
北村 慎次さん
ヤマハ発動機株式会社
FA技術開発グループ
私はグロメットフィーダーの設計・製作と、電装系やシステムまわりを担当しました。このグロメットフィーダーは円柱型のドラム内でグロメットをかき回して直進レーンに乗せ、スカラロボットのピックアップ地点に送っています。内部のかき上げステーはグロメットの形状に合わせて、大きさやかき上げる量を最適化するよう設計しました。ドラムは塩ビパイプをカットしたもの、直進レーンもアルミフレームをカットしたものなど、材料にはローコストな汎用品を採用しています。ここでは組み立て設備の一部として機能していますが、単体のフィーダーとしても提供可能で、その場合は同等のパーツフィーダーの約1/5のコストで導入可能です。
設備全体に関しては、内部のさまざまなところにセンサーやカメラを配置して、エラーの際はシステムを止めたり、該当製品をはじいて不良が発生しないように監視しています。またシステムにはドライブレコーダーのようにデータをストックする機能を搭載しており、もし設備内で不具合が発生した時は発生前後の画像データを見返して、どんな現象が起きたのか検証できるようにしました。なるべく現場の不安を払拭して作業を設備に委ねてもらえるように、どんな要望も丁寧にヒアリングしてシステムに反映していきたいですね。
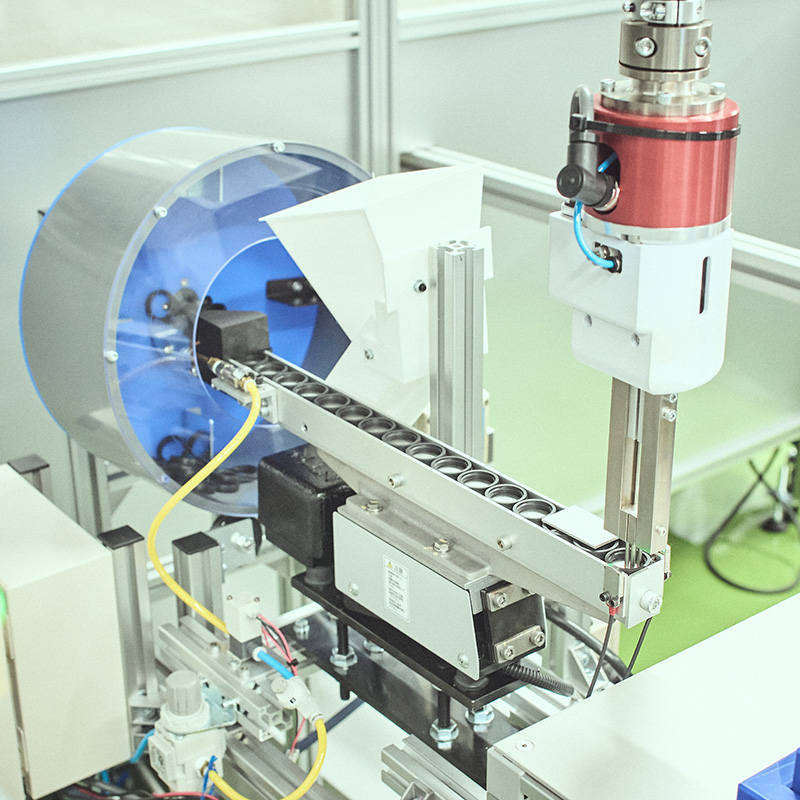
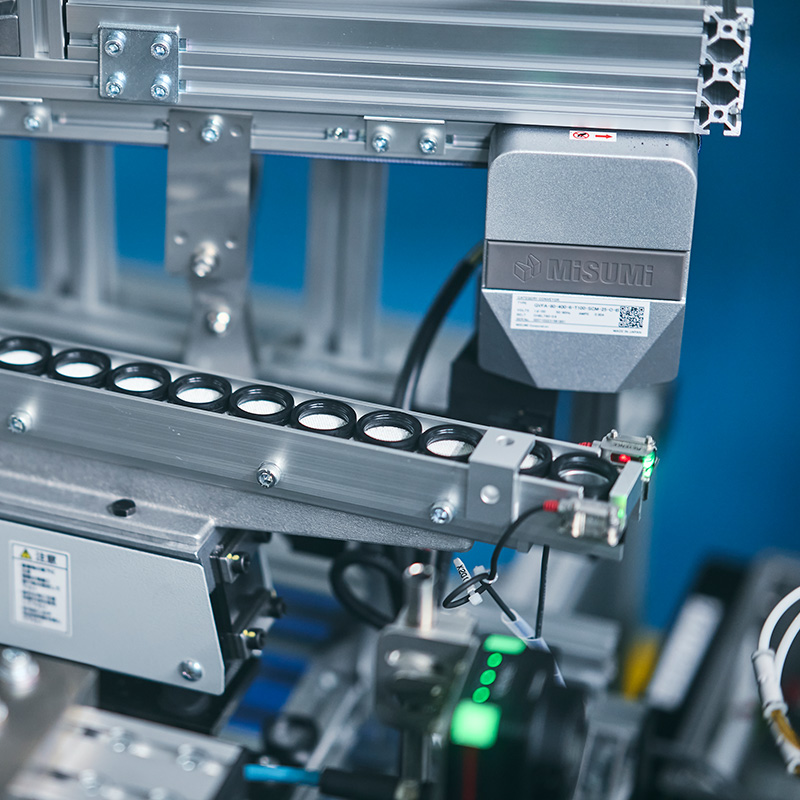
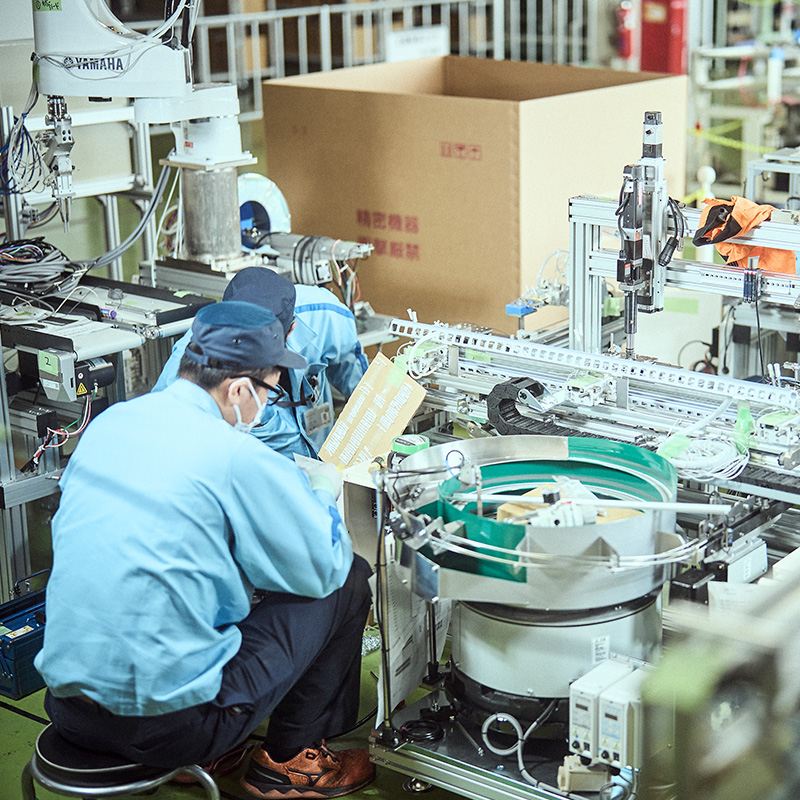
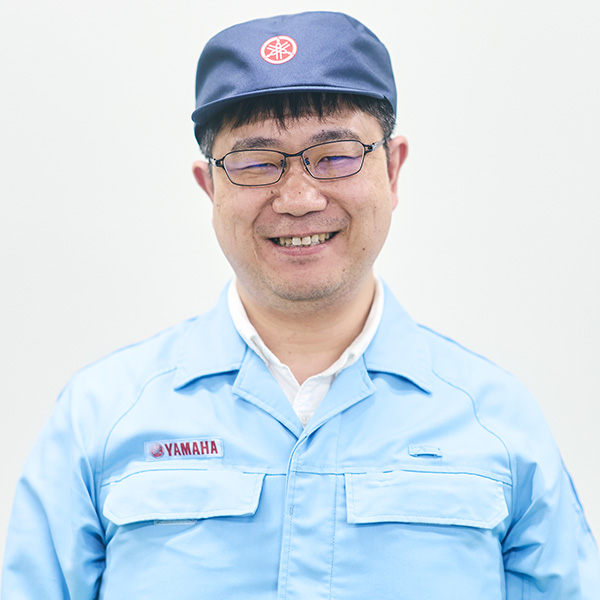
鈴木 健祥さん
ヤマハ発動機株式会社
FA技術開発グループ
このローコスト自働組立機では、主に設備全体の制御やシステム面を担当しました。組み立てる工程ごとに3台のPLCが制御していますが、それらを接続することで2台のスカラロボットと6種類のパーツを切り出すフィーダーの動きを連携させています。やはり難しかったのは工程数が多く、システムがどうしても複雑になることでした。異常が発生したときにはそれぞれの設備をどのように止めるのか、細かく切り分けて設定しなければなりません。設備担当の技術者と話し合って、隣り合う設備同士で止め合ったり、待機するだけでいいところは待機させたりと、ひとつひとつ対応を決めながら制御プログラムを作り込んでいきました。上で北村さんが述べているように、カメラやセンサーが多く設置されている関係でシステム面はどうしても複雑になります。しかしそこが現場の安心感に直結していると思うので、今後も継続的にブラッシュアップしていきたいです。
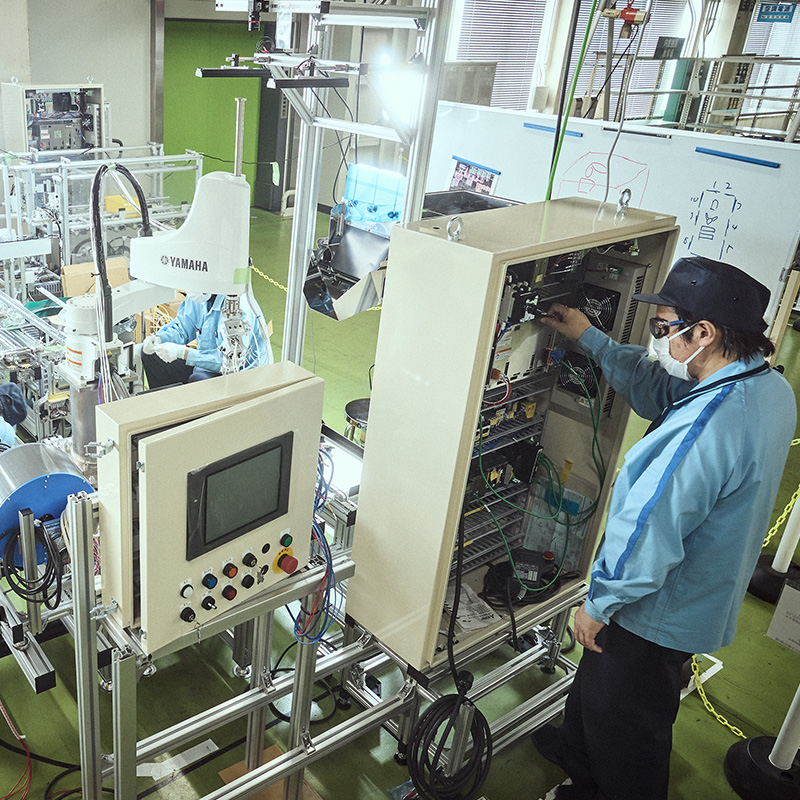
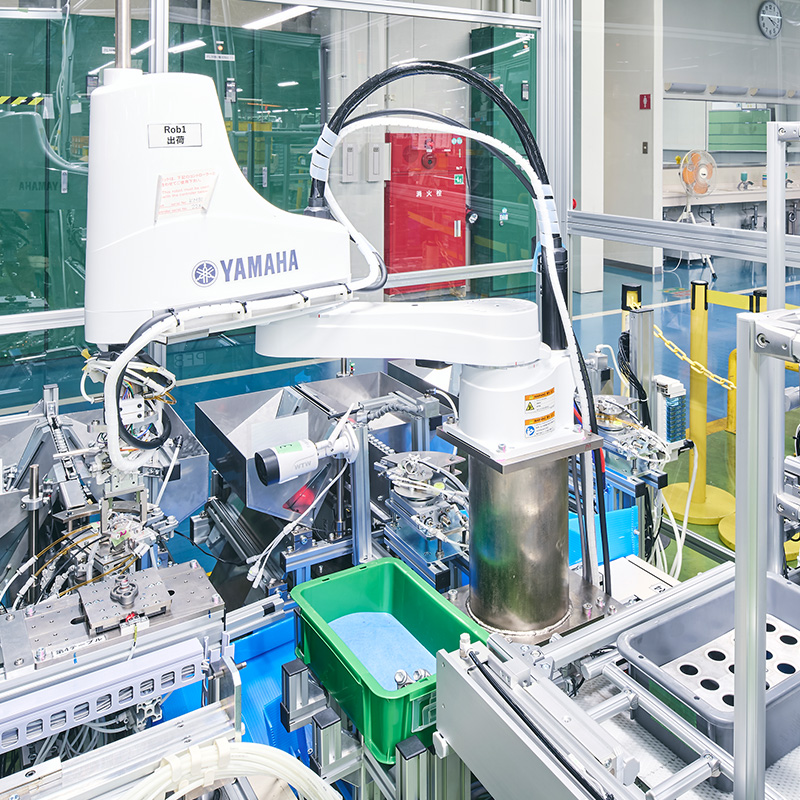
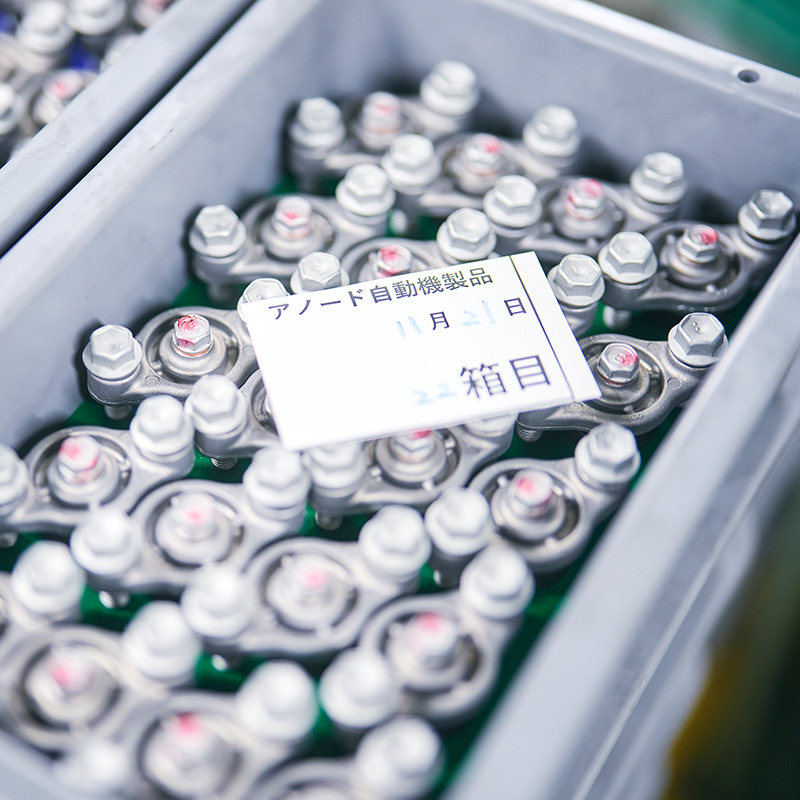
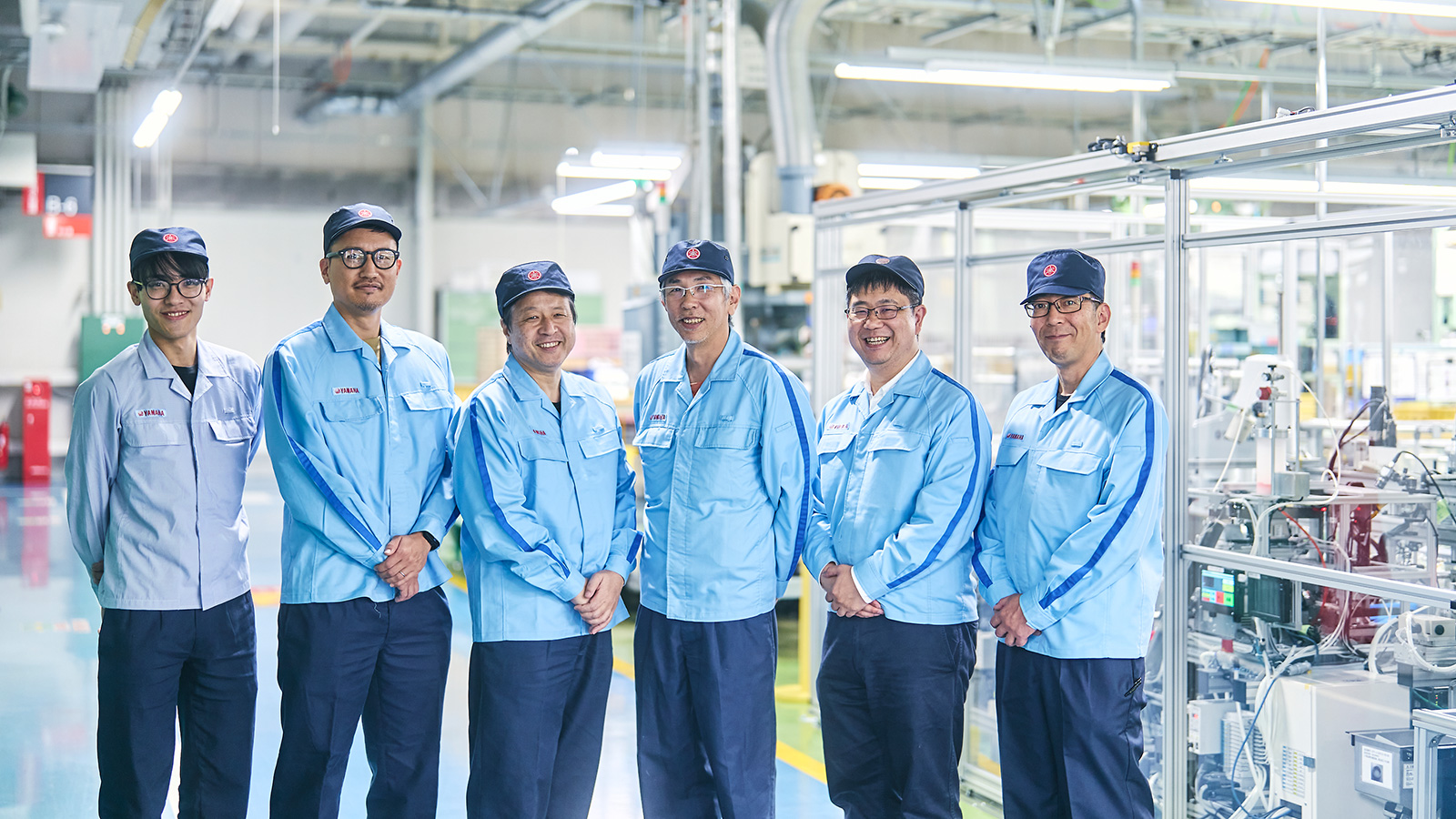