納得の品質が叶う!「量×質×省人化」SMTソリューション
ヤマハSMT装置の導入により、品質管理業務で体感することができる具体的なSMTソリューション例を紹介します。
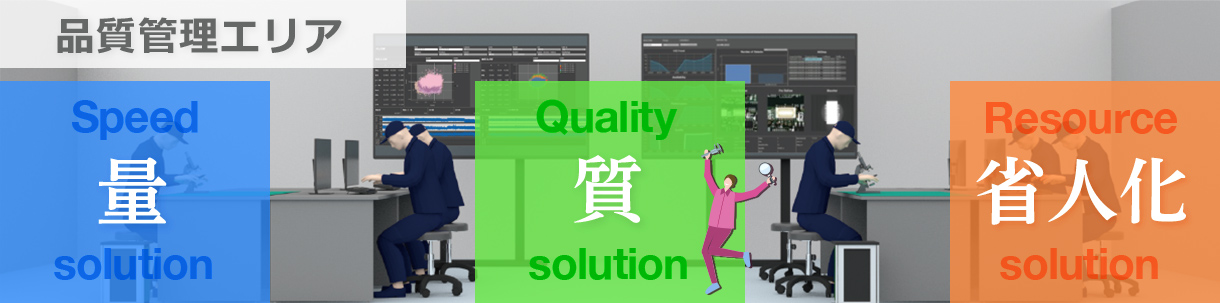
量

工程内不良件数の最小化
工程内不良の発生が多い場合、出荷数量を満たすために少し多めに生産しておくなど、リスク対策が必要になります。
1 STOP SMART SOLUTION では、工程内不良を最小限化することができるソリューションを用意しています。
リフロー前検査による不良の大量発生の抑制
より高い品質を求めて、リフロー前検査を導入するお客様が増えています。
リフロー前に検査することで、連続的な不良などもはんだが硬化する前に検出可能。
リフロー後での不良の大量発生を未然に防止します。
リフロー後検査時に文字がフラックスで消えて検出できない例
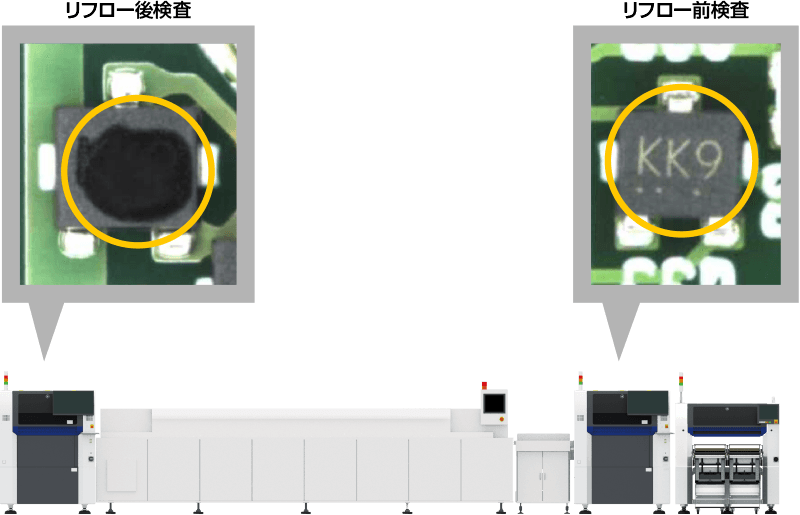
リフロー前で自動で不良を検出することで、初品チェックの自動化、修理作業工数の削減、廃棄ロスのコスト低減
リフロー前で極性検査、文字検査することで、検査機の過判定を低減し、直行率を改善
不良発生原因を特定することで、工程の不具合改善を促進し、工程内品質の向上を支援
検査機 - マウンタ連携による不良発生の抑制
不良発生時に、その不良の発生源である工程や原因を調査することは非常に面倒な作業です。
ヤマハではマウンターとAOIを連携させ、不良発生時に、発生したマウンターを即時停止します。
不良の連続生産の防止と不良発生要因特定のサポートも行います。
QAオプション

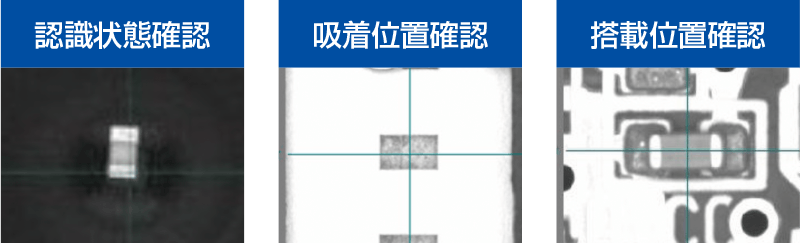
質

高い繰り返し性の高機能基板検査
SMTの生産現場において、後工程、お客様、市場への不良流出が発生した場合、極めて重大な問題になります。
ヤマハの検査装置は高い繰り返し検査性能により、不良流出の可能性を大幅に低減することができます。
検査装置にマウンター譲りの高剛性フレーム設計を採用
マウンターは、10本以上のノズル先端が数μm単位の位置に、超高速で部品を正確に搭載できる能力を保持しています。
この力のベースとなるのが、マウンター本体を支えるフレームです。
ヤマハでは、マウンターメーカーである強みを生かし、高剛性フレームを検査装置にも採用。業界でもトップクラスの検査精度を実現しています。
高剛性フレーム
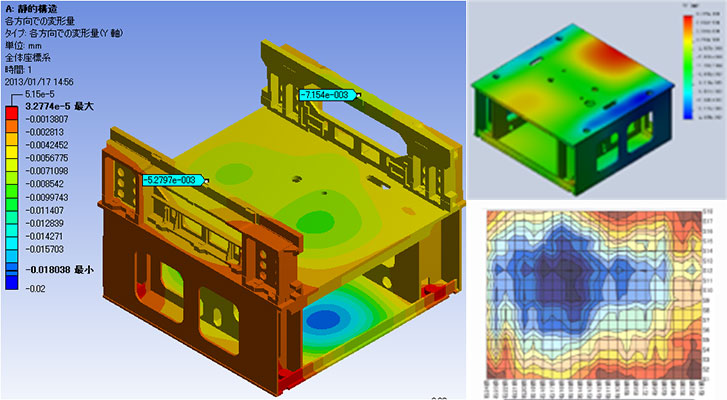
多様なSMT基板にマッチする多機能な検査装置
ヤマハのAOIでは、背の高い部品やウェハ部品のような3D検査が難しい基板にも対応できる、多機能な能力を有しています。
SPIには、はんだだけではなく接着剤を検査する機能もあり、様々な場面で不良流出を防止する用途でご活用頂けます。
8方向プロジェクター(AOI)
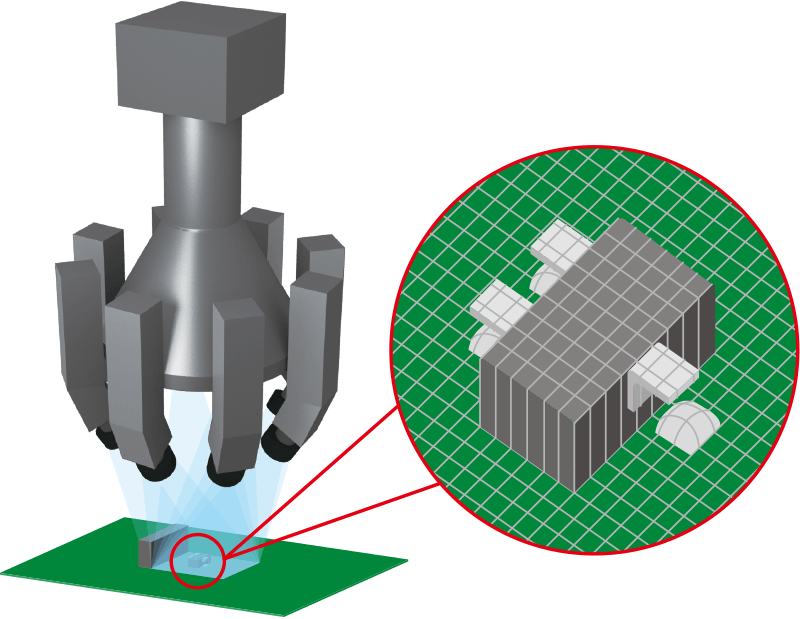
同軸照明(AOI)
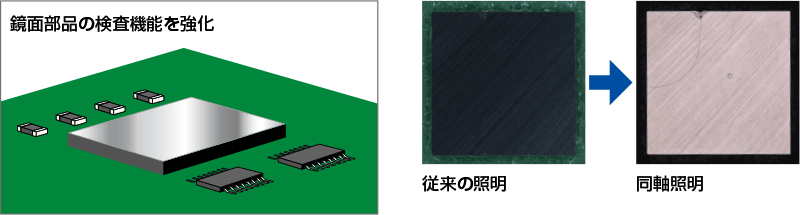
文字検査(AOI)
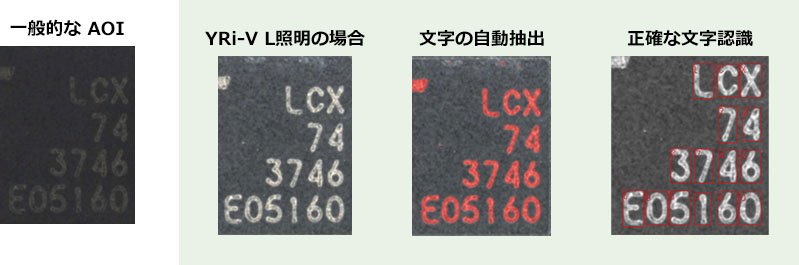
ボンド検査
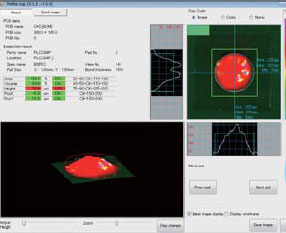
高速、高分解能検査
精度の良い検査をするためには、高い分解能による画像取得が非常に重要です。
5μmの超高分解能レンズや、複数回撮像することで、疑似的に高分解能を実現する技術を用いて、高精度検査を実現します。
超高分解能 5μmレンズ(AOI)
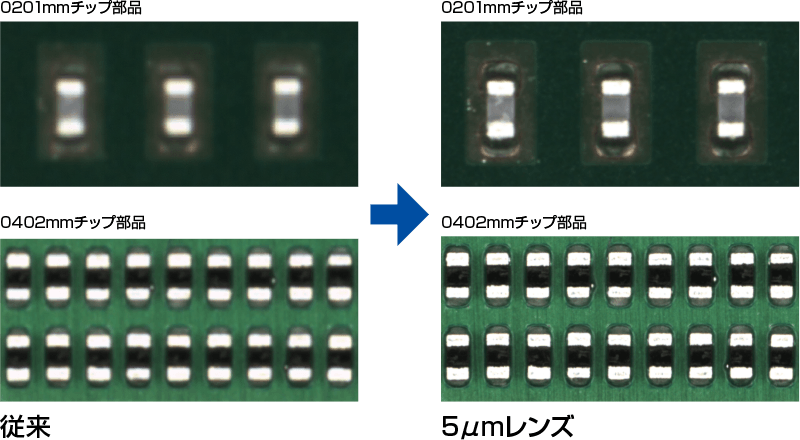
超解像技術(SPI)
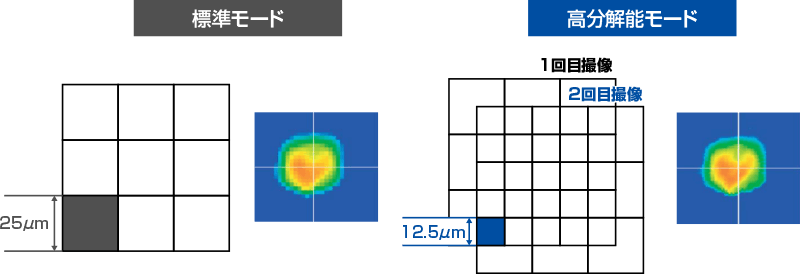
省人化
改善活動が簡単

不良発生要因分析
不良が発生した際に最も重要なことは、同じ不良を発生させないように適切な対策を実行することです。
1 STOP SMART SOLUTION ではこの対策実行までの過程を、効率的かつ効果的に行うことができるようになります。
工程毎の画像照合による不良発生原因特定
リフロー後の基板で不良が発覚した場合、不良が発生した原因がどの工程であったのかを特定することは困難なため、改善活動に繋げることは困難でした。
1 STOP SMART SOLUTION では、すべての工程の画像を照合できるため、リフロー後であっても、どの工程から不良になったのかを特定し、改善を促進することができます。
N点照合
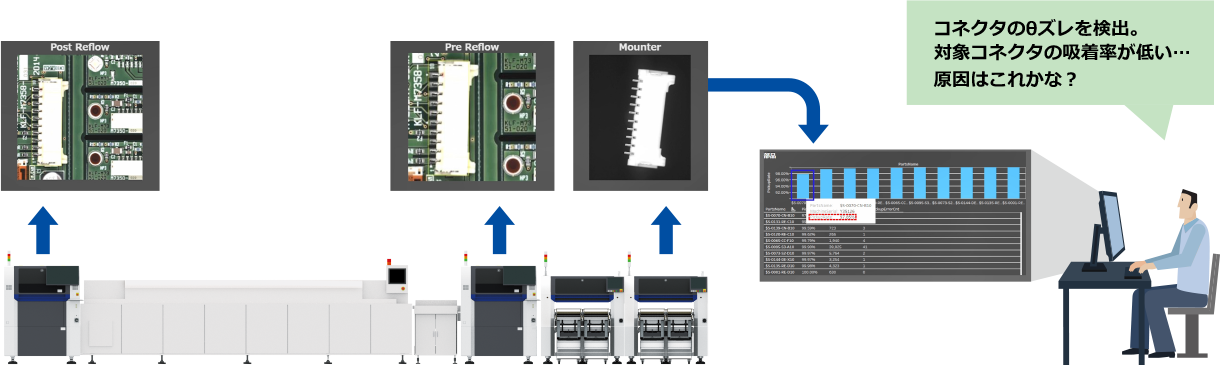
[不良発生原因特定事例]
部品に異物が付着
[原因]
はじめから部品に異物が付着していたことが原因。
[対策]
部品メーカーへフィードバック
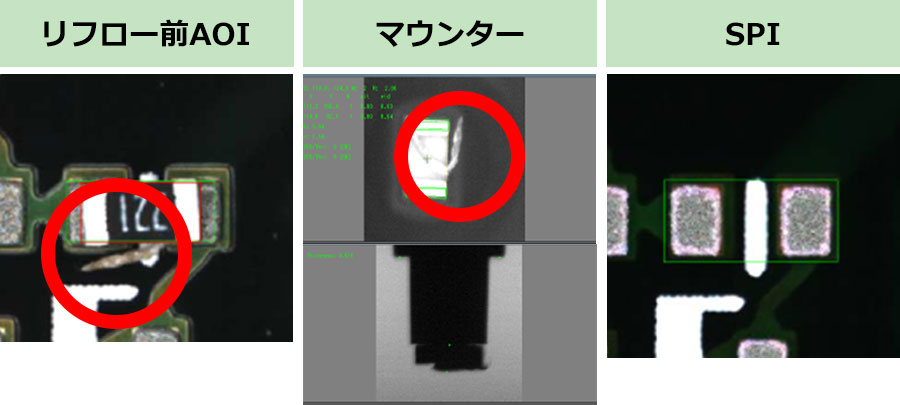
[不良発生原因特定事例]
部品の表裏反転が発生
[原因]
リールの切り替わり時に発生したことを特定。
スプライシング作業の失敗が原因。
[対策]
スプライシング作業の再指導
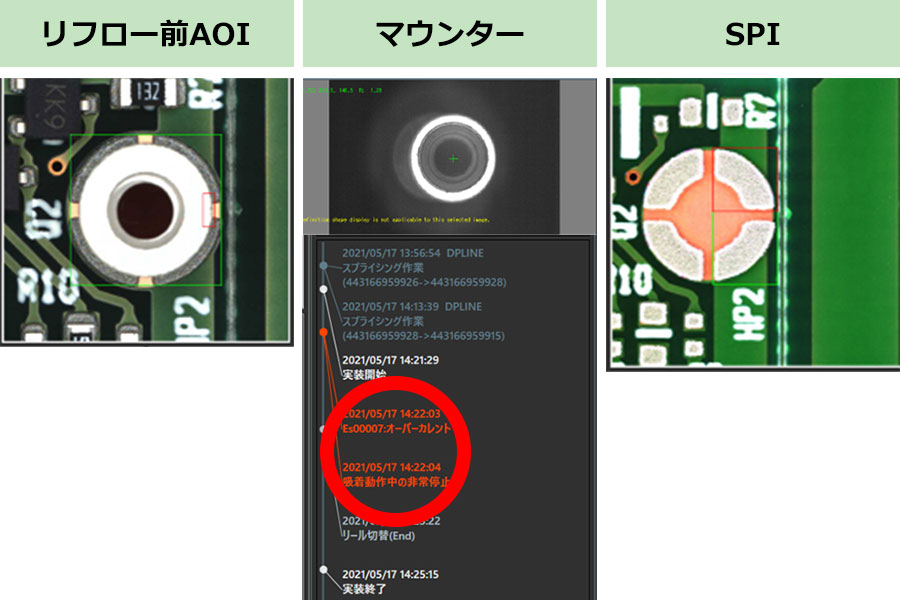
データから見る不良発生要因の特定
1 STOP SMART SOLUTIONでは、各装置から出力される膨大なログデータから、各装置間での相関関係を見つけることができます。
例えば、SPI と 印刷機では、ローリング径が小さくなった時に、はんだ量が少なくなってしまっているなど、不良発生要因の特定をサポートします。
分析ダッシュボード
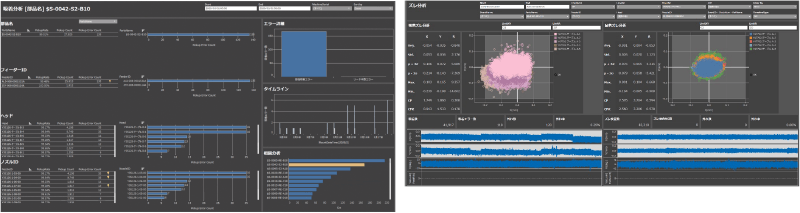