全自動段取りラインづくりのレシピ
「止まらないライン」「オペレーションフリー」なラインを実現する為には「全自動段取りライン」化が必要不可欠。ヤマハならではの秘伝のレシピを大公開します
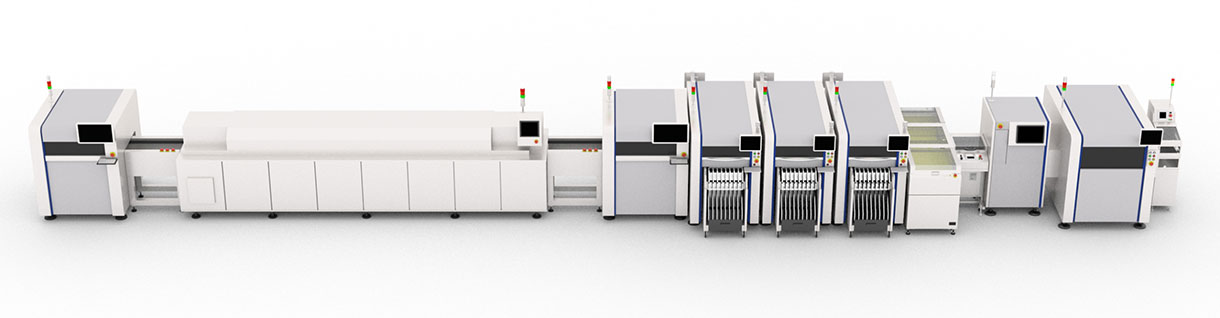
こんなお困りごとありませんか?
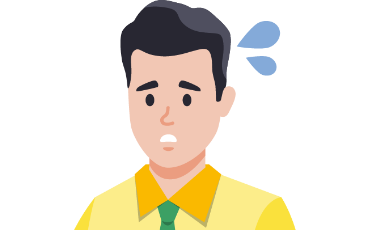
段取り替えに伴うロスを減らしたい。でも、設備仕様に縛られて簡単には段取り替えの効率アップが難しい…
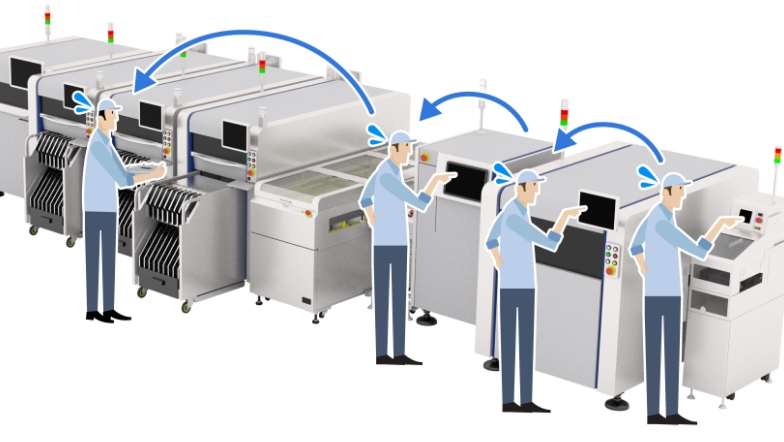
ローダー、印刷機、SPI、マウンター…1台ずつの段取り替えはすごく時間がかかる。
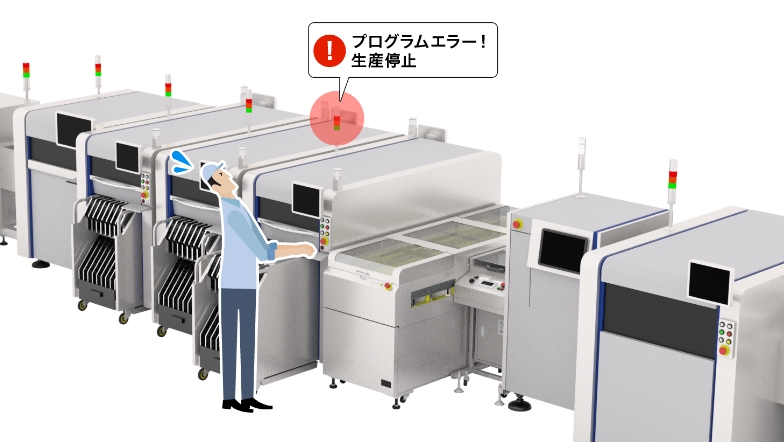
段取り替え時に読み込むプログラムを間違えてエラーで止まってしまった。
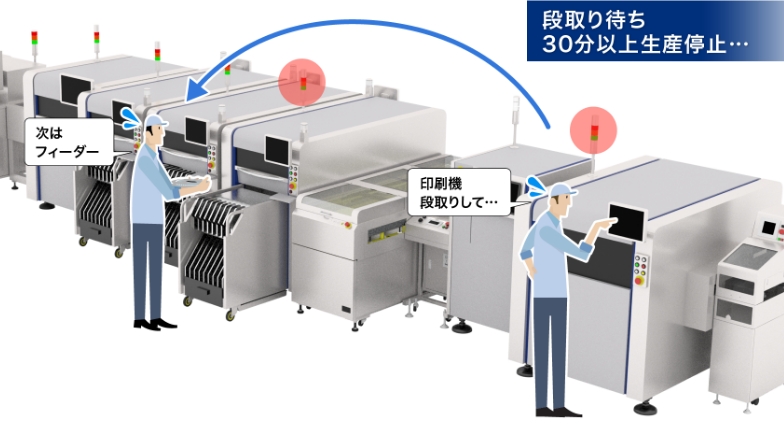
印刷機の段取り替えを終えたら、マウンターのフィーダー交換…長いと30分以上の設備停止になってしまう。
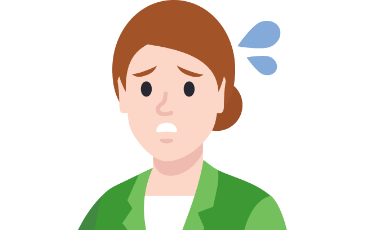
SMTラインの価値を生むライン稼働率を0.1%でもUPさせたい!でも、どうすればいいのか…
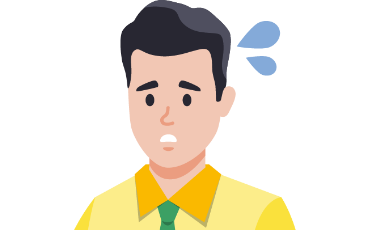
作業者の作業工数・効率を改善したい。一人でも少ないオペレーター数で最大の生産性を達成したい!でも、どうすればいいのか…
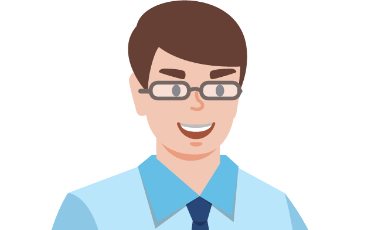
そんなSMTユーザー様の代表的な声にヤマハはライン丸ごとの最適提案(YAMAHA SMT Concept 『1 Stop Smart Solution』)でお応えします!
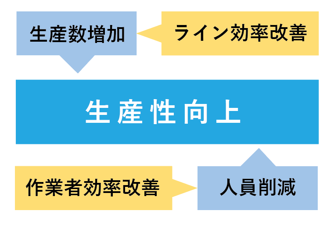
ヤマハの提案
YAMAHA SMT Concept 『1 Stop Smart Solution』 Presents「全自動段取りラインづくりのレシピ」紹介!
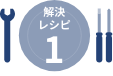
自動段取り
上流機からの引継ぎ段取りで稼働率向上!
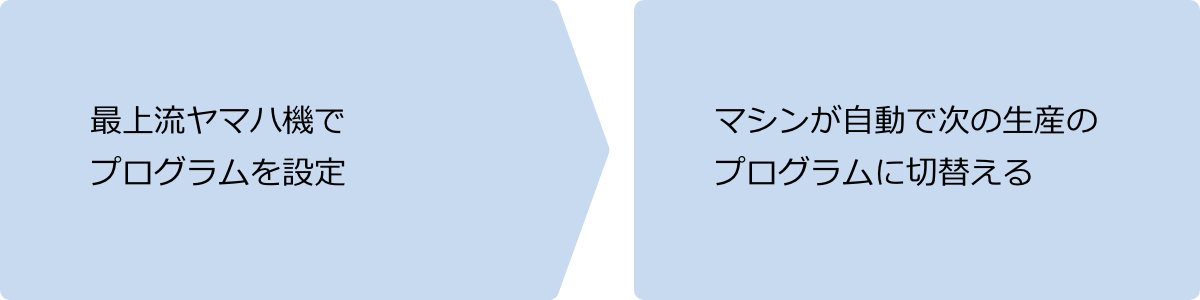
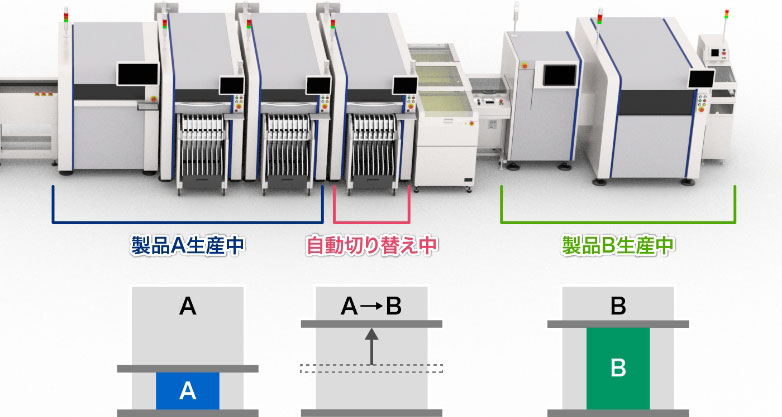
Case 1
最上流ヤマハマシンでプログラム指定
下流マシンへ引継ぎ自動段取り完成
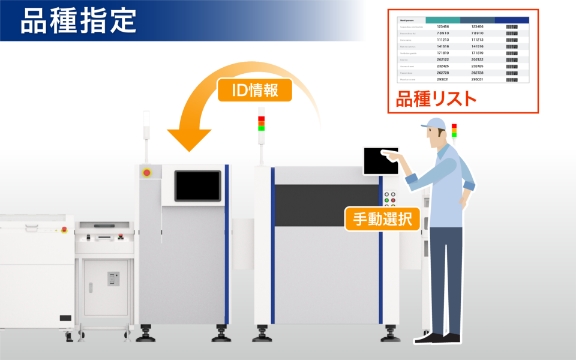
Case 2
最上流ヤマハマシンでカンバン段取り
下流マシンへ引継ぎ自動段取り完成
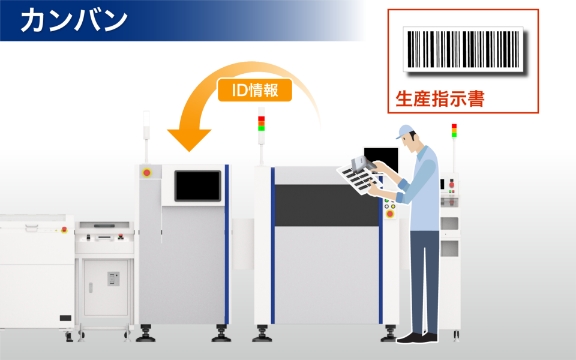
Case 3
最上流ヤマハマシンの更に上流コンベアで2Dコード読み取り
下流マシンへ引継ぎ自動段取り完成
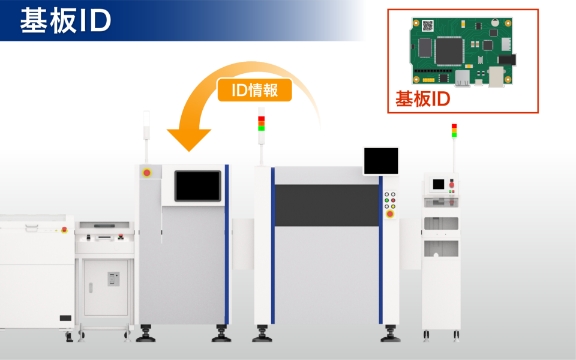
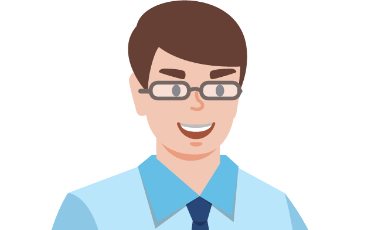
ヤマハマシンで揃えると、印刷機からリフロー前まで全自動段取りライン化が実現します!
ヤマハ設備からの他社設備への引継ぎ実績も多数あります!
他社周辺設備連携実績紹介 各種コンベア、インライン検査機、リフローメーカー など
YAMAHA SMT Concept 『1 Stop Smart Solution』でお応えします!
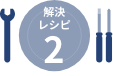
自動段取り他社装置連携
主要SMT関連装置メーカーが連携!他社マシン同士の引継ぎ段取りで稼働率向上!
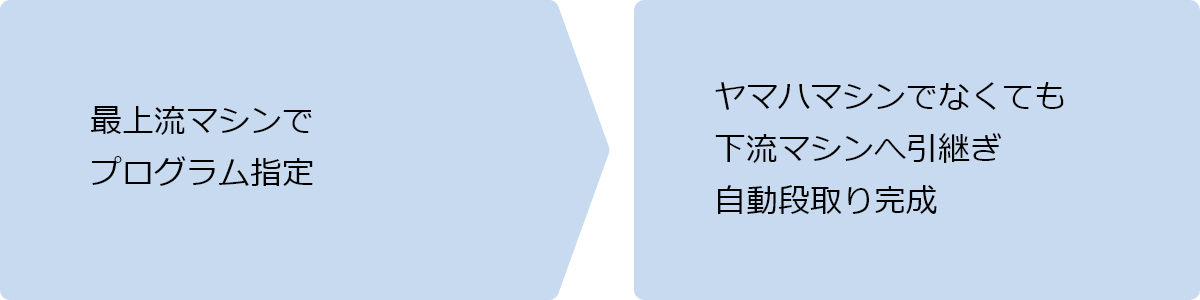
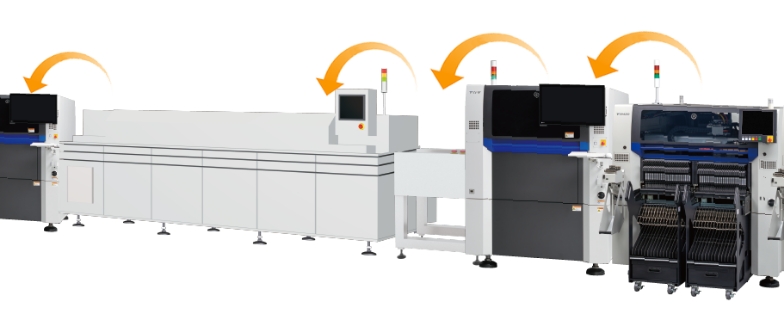
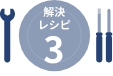
共通段取り最適化
共通段取りでの最適化によりマウンター段取り替えを最小化する
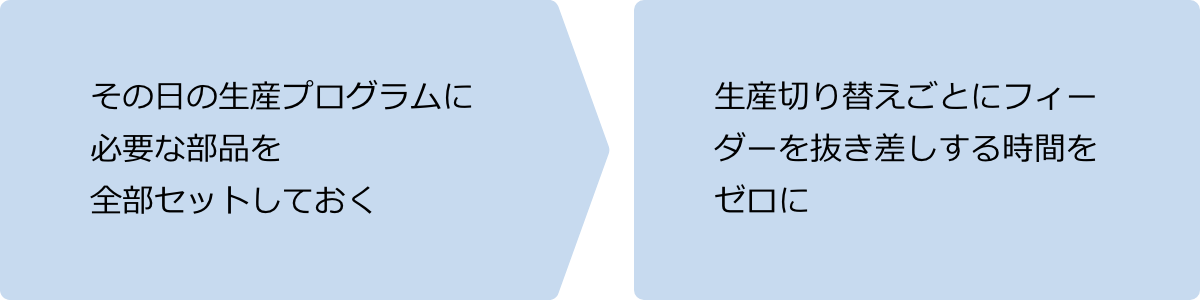
1head solutionにより一つのヘッドで多様な部品を搭載でき、最大128本(YRM20の場合)のフィーダーを搭載可能なヤマハマシンだからできる、共通段取り。生産切り替え時のフィーダー抜き差し作業にかかる時間は長いと30分を超えることも。事前にセットしておくことで、フィーダー交換に伴う停止時間をゼロにします。
ヘッド交換なしで様々な部品を実装できる
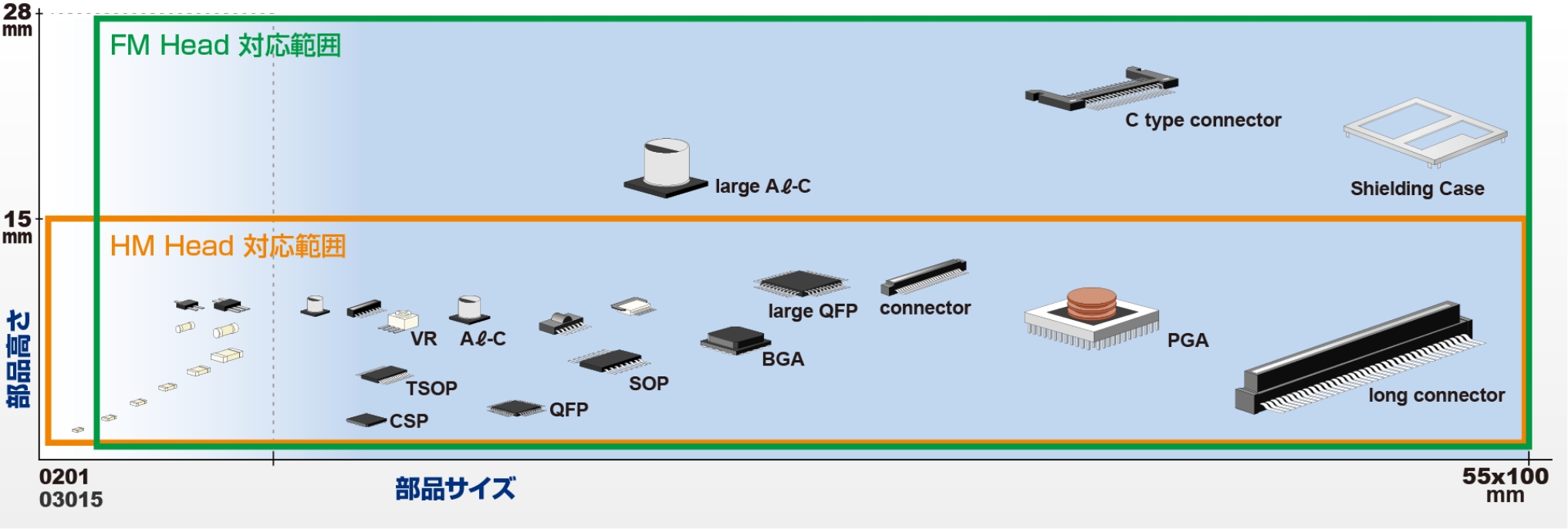
搭載可能部品数が多い
YRM20
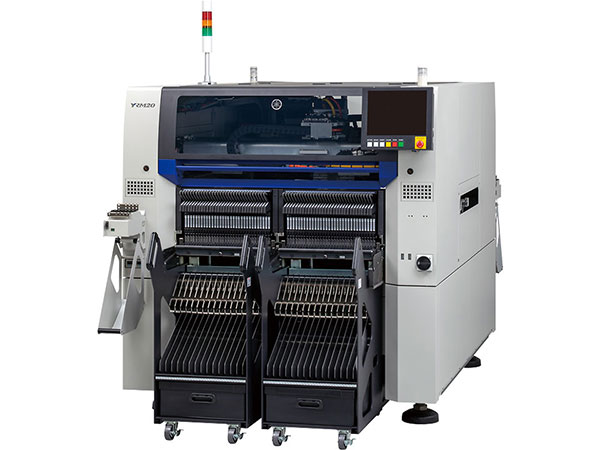
1台で大量(8mm換算)128本のフィーダー配置が可能。
小型軽量4分割台車
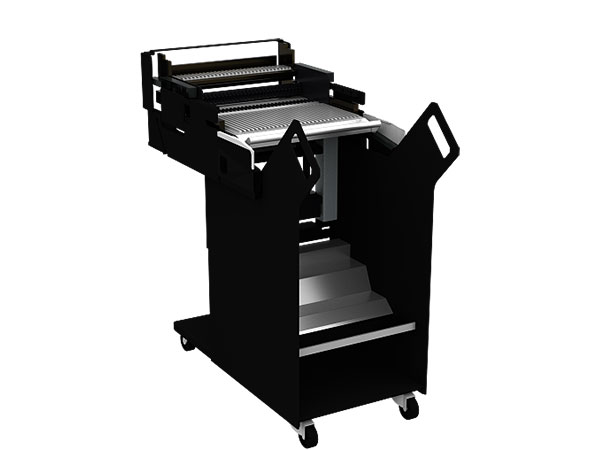
・1台車に(8mm換算)32本のフィーダーをセット可能
30段トレイ供給装置(無停止補給タイプ)
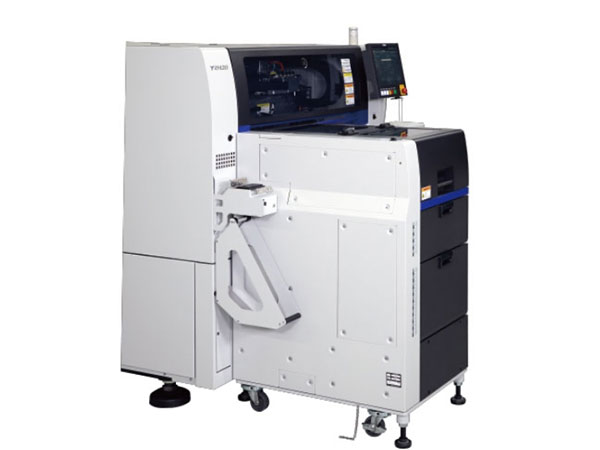
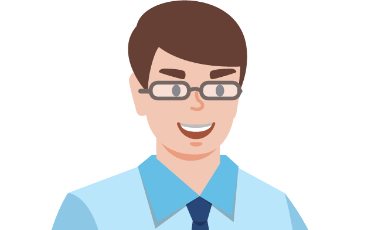
1head solutionのヤマハだからできる共通段取り最適化!
ヘッド交換なしで最小0201mmから最大55x100mm部品まで対応できるため(HMヘッドの場合)、予め共通段取りで部品をセットしておけば様々な生産プログラムをオペレーターの手を借りずにこなすことができます!
“共通段取り最適化”とは…
“1ラインに乗り切る部品品種数分の基板”の最適なフィーダー配置をシミュレートする機能
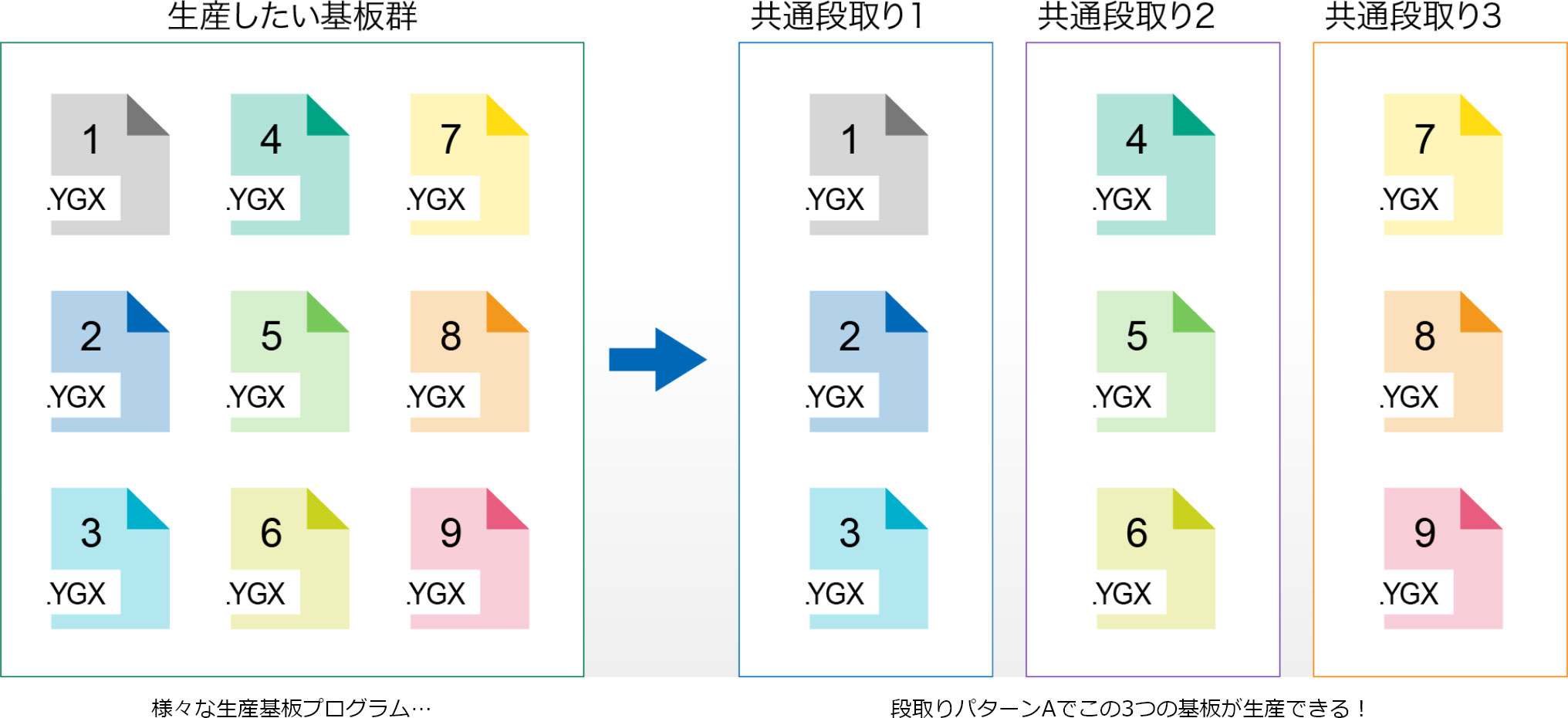
台車グループを設定しての共通段取り最適化
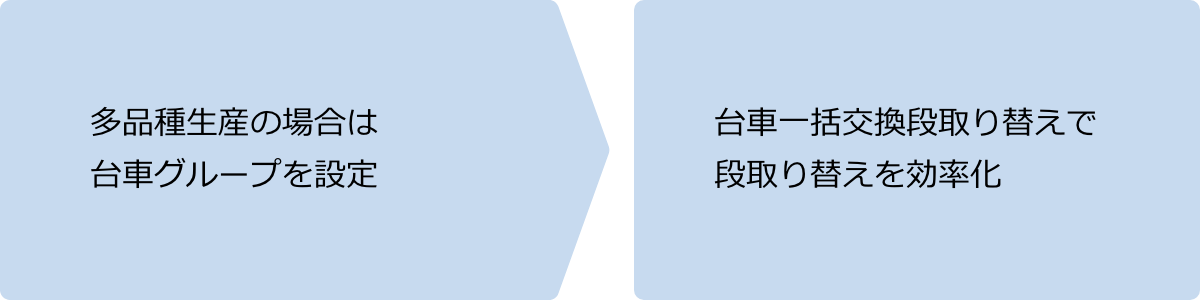
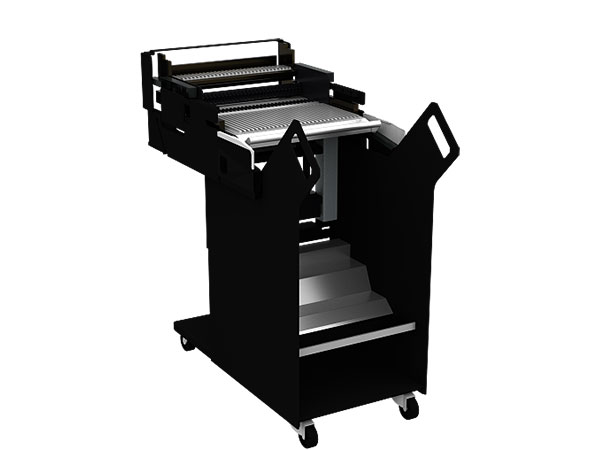
”グルーピング”とは…
類似基板を自動判別し、最少段取り回数になるグループに自動的に分割
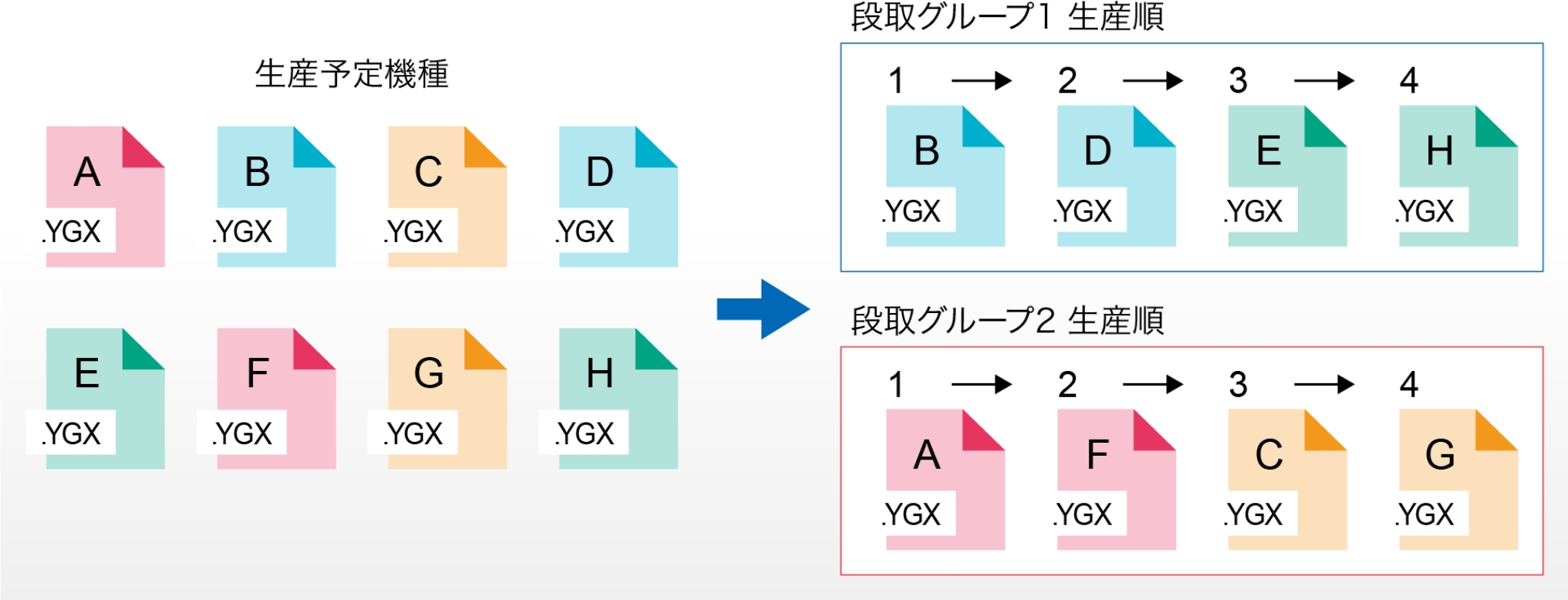
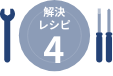
印刷段取り全自動化
印刷機の段取り替えの全自動化対応
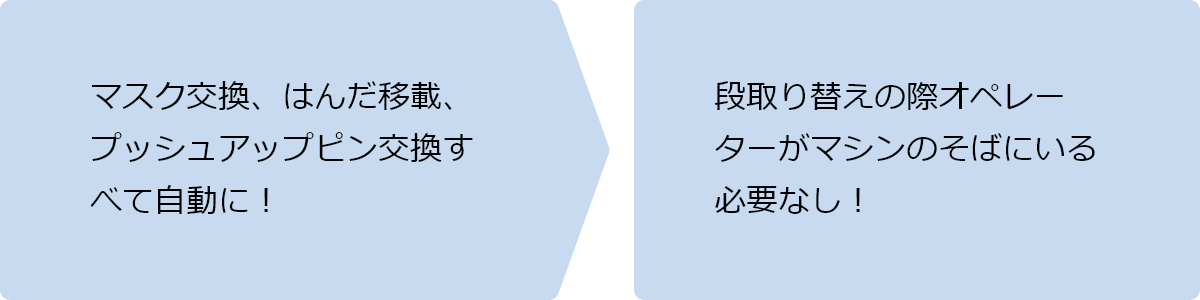
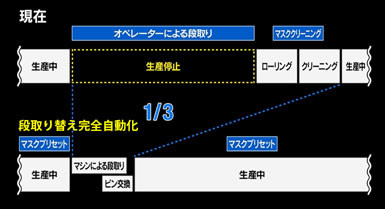
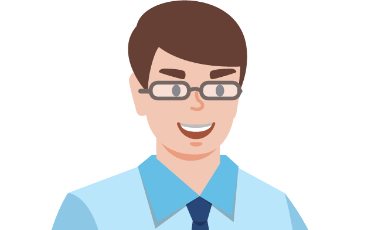
プッシュアップピン自動交換は「4ゼロ」を実現!
これまでオペレーターを悩ませていた治具の置き場、治具のコスト、治具の手配納期、ピン配置のセットミスがゼロになります!
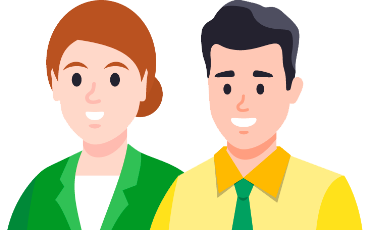
段取り替え作業をマシンに任せられるようになることで、1歩1秒1円といわれるオペレーター作業が大幅に削減され、生産性アップにつながります。
YAMAHA SMT Concept 『1 Stop Smart Solution』導入事例
「全自動段取りラインづくりのレシピ」紹介!
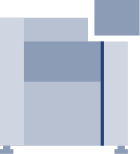
導入事例 1
産業機器向け基板生産ライン
Before

・ローダー
・YSP
・コンベア
・YS24
・YS24X
・コンベア
・YSi-12
・コンベア
・リフロー
・冷却コンベア
・バッファコンベア
・YSi-12(レーザー検査付き)
・OK/NG振り分けコンベア
・アンローダー
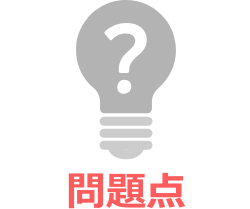
- 1.
- 段取り替えに伴う各装置のプログラム変更、印刷機の段取り替え作業などにより、20分程度生産を停止する必要あり。
- 2.
- 未習熟者の作業に依る、リード浮きなどの不良がリフロー後の検査機まで流出してしまい、修理作業が大変。
- 3.
- 部品補給作業に追いつかず、装置をエラー停止させてしまい、生産性を落としてしまう。
After

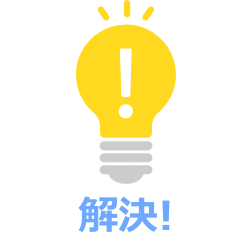
- 1.
- 印刷機からの自動段取りにより、これまで20分かかっていた段取り替えの停止時間が5分に短縮された。
- 2.
- リフロー前への3D検査導入により、リード浮きなどの不良もリフロー前で検出し、工程内不良率は平均1ppm未満を達成。
- 3.
- WEB残数モニタとオートローディングフィーダーの組み合わせで、部品補給を効率化し、マシンのチョコ停時間を大幅に削減。
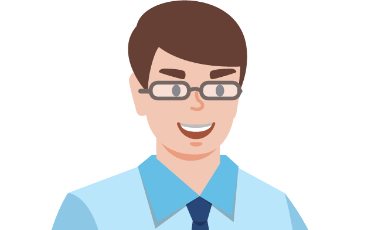
このラインで使ったヤマハの技術のポイントは…
マシン:YSP10、YSi-SP、YRM20、オートローディングフィーダー、YSi-V
ソフト:自動段取り、ダッシュボード、WEB残数モニタ
印刷機:段取り替えの全自動化対応、12ozシリンジPSC、印刷位置ズレフィードバック
検査機:QAオプション、モバイル判定、N点照合
自動段取り、オートローディングフィーダーなどの導入で生産停止時間の大幅短縮を実現しました。リフロー前に3D検査を導入し、リフロー後の不良発生を抑制しています。
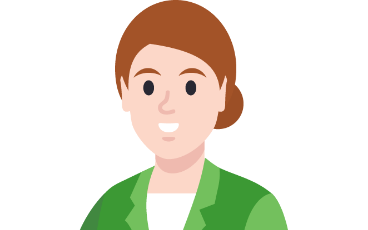
ヤマハの良いところは、段取り替え作業が簡単で、かつ高い生産性も出せるところです。
自動段取りをカンバン段取り+引継ぎモードで導入しました。先頭の印刷機で生産品種のバーコードを読むだけで、SPI及びマウンターまで自動で段取りが行われるため、その間に投入基板のハンドリングなどの作業が行えるようになりました。段取り時間の大幅短縮につながっています。1ヘッドソリューションの特徴を活かした共通段取り最適化も併用しており、フィーダーや台車交換無しでの切り替えを実現できました。
また、リフロー前に3D AOI(YSi-V)を導入することで、ほとんどの不良をリフロー前で検出することができるため、未習熟のオペレータによる作業があったとしても、1ppm未満の工程内不良率を実現できており、はんだこてによる修理作業がほとんどなくなりました。
ダッシュボードやi-ProDBで使用可能な各工程ごとのN点照合により、発生原因が特定できる不良が増えたことも品質向上の一因であると感じています。
部品補給の面においても、WEB残数モニタにより ラインの大画面やモバイル端末へライン全体の部品残数情報を表示するとともに、オートローディングフィーダーを併用することで、より効率的な部品補給ができるようになり、部品補給が間に合わないことによるライン停止はほとんど発生しなくなりました。
生産量が大幅に増加しつつも、1ライン 1オペレータでの生産が継続できているのは、ヤマハの豊富な機能群と各装置の大幅な生産性向上に依るものだと思います。 今後も、有効な機能を積極的に導入して、より高効率で高品質な生産ラインの構築を目指していきたいと思います。
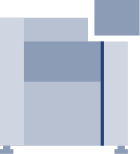
導入事例 2
多品種多部品24H生産車載基板生産ユーザー
Before

・ローダー
・基板クリーナー
・YGP(下流延長コンベア)
・SPI
・YG100
・YG100
・YG100
・リフロー
・冷却バッファコンベア
・アンローダー
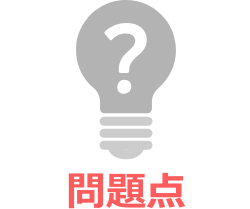
- 1.
- 工程内不良率が平均15ppm。不良発生原因が潰し込めずなかなか改善が難しい。1ライン1オペレーター運用なので…
- 2.
- 段取り替えに時間が掛かり稼働ロスが発生する
- 3.
- 部品補給が必要な時に作業が追いつかず稼働ロスが発生する
- 4.
- 1名でローダーやアンローダーのマガジン出し入れ、印刷機へのはんだ補充や各マシンの段取り替えとプログラム切り替え作業を行うためオペレーター歩数が1名1日(1直で)2万歩近い歩数。
After

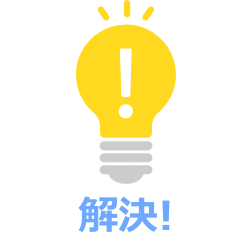
- 1.
- 工程内不良率が平均で1.00ppm未満に。最も良い月では0.1ppmを切った(1か月間で工程内不良1点のみ。)
- 2.
- 段取り替えが完全自動化。ローダーで2Dコードを読み込みあとは自動で段取り替え完了。印刷機の段取り替えもYSP10にて完全自動となった。段取り替えも2.5~4.5分で完了する。
- 3.
- オートローディングフィーダー導入で部品補給での稼働ロスが激減。
- 4.
- 印刷機のはんだ補充自動化と段取り替えの全自動化対応により印刷機への訪問回数8割減。その結果オペレーター歩数2割削減。
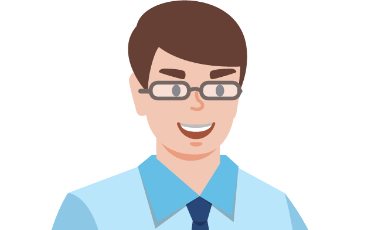
このラインで使ったヤマハの技術のポイントは…
マシン:YRM20、YSi-V、YSP10、オートローディングフィーダー
ソフト:QAオプション、モバイル判定、N点照合
印刷機:12ozシリンジPSC 段取り替えの全自動化対応
オペレーターの負担を減らすことで、効率化につながり、結果的に生産性アップを実現しました。
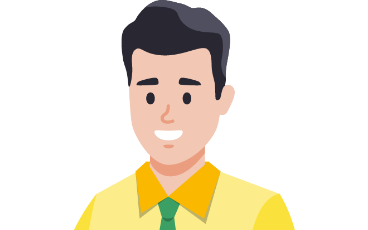
ヤマハの良いところは多品種生産だけど「速い!」事です。
4ライン保有でヤマハラインは1ラインだけですが、ほかのラインに比べてとにかく速いです。
ヤマハラインを更新する前は、ほかのラインと同じぐらいの生産能力でしたが、YSM20R導入後は同じ面積にも関わらず生産能力が約2倍にUPしました。オペレーターの数は変わらずです。部品の補給頻度は2倍近くなっているもののオートローディングフィーダーを活用する事で補給切れ発生は最小限にとどめられています。結果として、90%を超える設備総合効率でヤマハラインを稼働できています。
また工程内不良の発生は1/10以下に抑えられています。
これはリフロー前に3D外観検査装置YSi-Vを導入したことが非常に大きいです。
YSi-Vで不良を発見したら即時にマウンターをサイクル停止させて不良発生個所をチェックします(QAオプション)。この運用によって不良の大量発生を無くすことが出来たほか、オペレーターが自分で考えてノズルメンテナンスなどの改善アクションを取れるようになり大幅に品質向上させることが出来ました。
不良が減ったことで納入先に迷惑をかけることが無くなり、現場も生技も管理部門もみな喜んでいます。もちろん、社長、部長など役員も喜んでいます。(笑)
更に良いラインに育てるべく、これからも現場でヤマハ装置を使い倒します!
さらに! 部材自動補給で「止まらない」「オペレーションフリー」ソリューション!
1.印刷機 12ozシリンジPSC
印刷品質に影響するハンダのローリング径を安定化。新規開発の12ozシリンジタイプにより長時間の無停止生産を実現。
2.マウンター オートローディングフィーダー
オートローディング機能により、いつでも、だれでも、簡単にテープ部品の補給が可能。約5秒と高速なテープローディング時間※
※テープ送り開始~吸着準備完了
3.マウンター 無停止トレイ補給
パレット単位、マガジン単位の無停止トレイ部品供給へ対応し、効率的なトレイ部品の補給作業と、マシンを止めない生産を実現。
4.マウンター 段積み補給ソリューション(スティック、段積みトレイフィーダーほか)
お客様のご要望、対象の部品に応じた段積みスティックフィーダーや段積みトレイフィーダーなど対応実績が多数あります。詳しい情報は販売店、もしくは以下の問い合わせページまでお問い合わせください。
ライン構築サポートエンジニアがご相談にお応えします
ヤマハのライン構築サポートエンジニアがお客様(ヤマハ設備使用有無問わず)のご相談に無料で対応(電話、メール、訪問、ショールーム見学ほか)を実施しております。