生産ラインで使って満足! 『量 × 質 × 省人化』 SMTソリューション
ヤマハSMT装置の導入により、生産ラインで体感することができる高い生産品質を実現するSMTソリューションを紹介します。
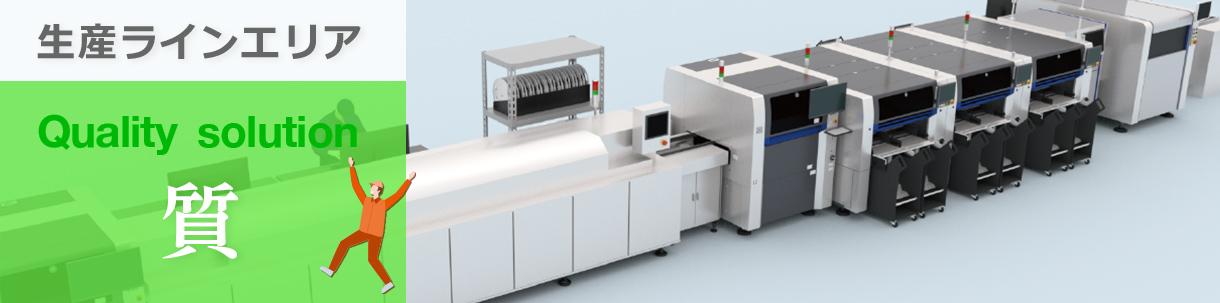
チョコ停が少なくてストレス軽減!

吸着率悪化を防ぎ、高い吸着・搭載性能を維持するソリューション
生産ラインで最も多く発生するエラーとして、マウンターの吸着エラーが挙げられます。
1 STOP SMART SOLUTIONでは吸着エラー・搭載ミスを最小限にするためのソリューションを提供します。
多重補正による安定した吸着・搭載性能
ヤマハマウンターは、安定した部品吸着と高度な搭載を実現するために様々な補正機能を搭載しています。
生産中に装置内に設置された補正マークを自動で読み込むことで、常に安定した吸着・搭載性能を実現します。
多重補正システム MACS
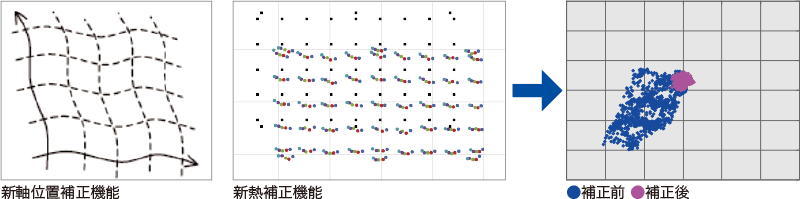
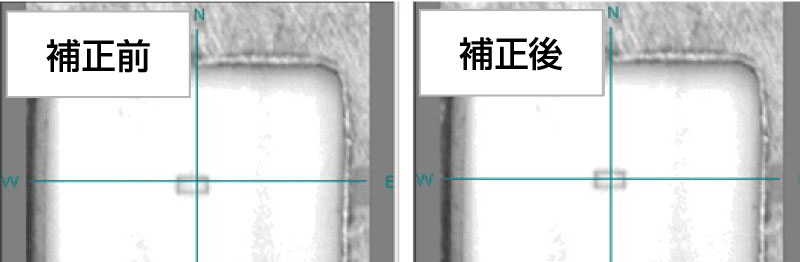
ダッシュボードによる高度な吸着エラー分析
吸着エラーの改善は、エラー数やエラー率の高い部品の改善から進めると効果が高まります。
1 STOP SMART SOLUTIONでは、「どの部品から改善すべきか」、「問題は部品なのか、 ヘッド、またはフィーダーなのか」など、吸着エラーを発生させている原因を迅速に特定するソリューションがあります。
分析ダッシュボード
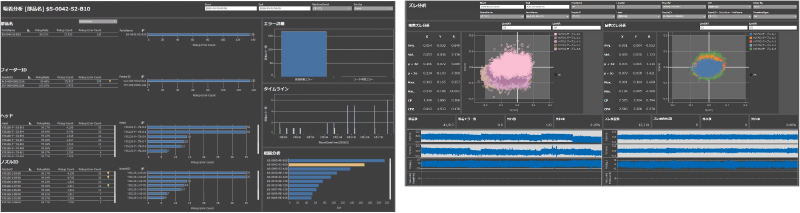
All Image Tracer
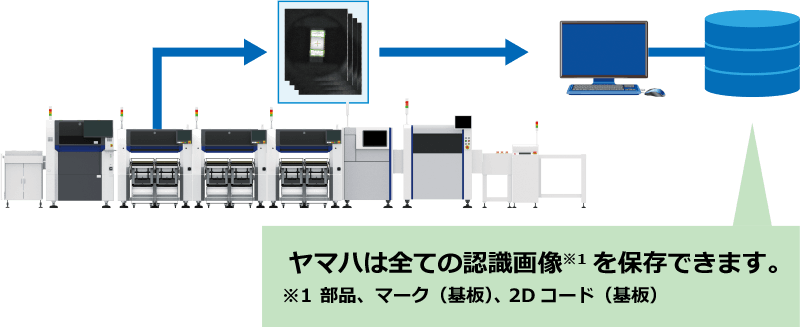
ノズルヘルスチェックによるノズル状態の自動適正化
高い吸着率を維持するには、ノズルの状態を適切に保つことが非常に重要です。
ヤマハのマウンターでは定期的にノズルをブローするブローステーションを搭載しています。エア―経路の清掃を行い、吸着率の悪化を防止します。また、ノズル先端バネの摺動状態チェックや画像検査をして、常に正常な状態に保ちながら、生産が可能です。

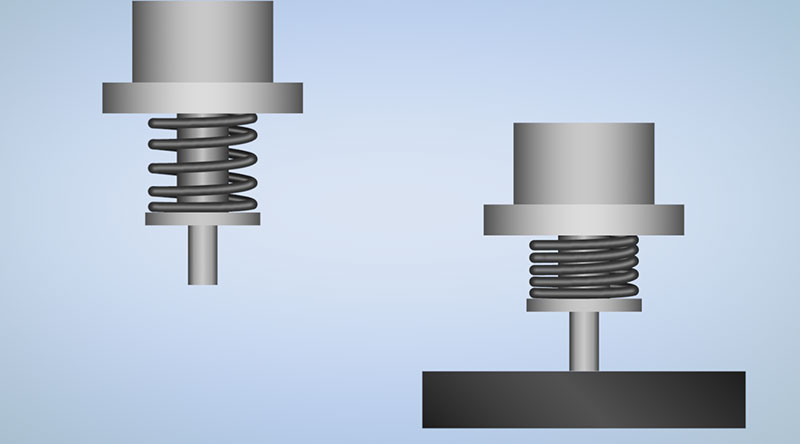
生産ラクラク!

高いはんだ印刷精度とフレキシビリティ
生産ライン内で最も不良発生の割合が高いと言われる、印刷工程。
ヤマハのはんだ印刷ソリューションは、この課題を解決します。
アタック角度可変スキージ 3Sヘッド
ヤマハ印刷機オリジナルの角度可変スキージ3Sヘッドにより、印刷条件の幅が広がります。
あらゆる基板へのはんだ印刷を、高い品質で行うことが可能です。
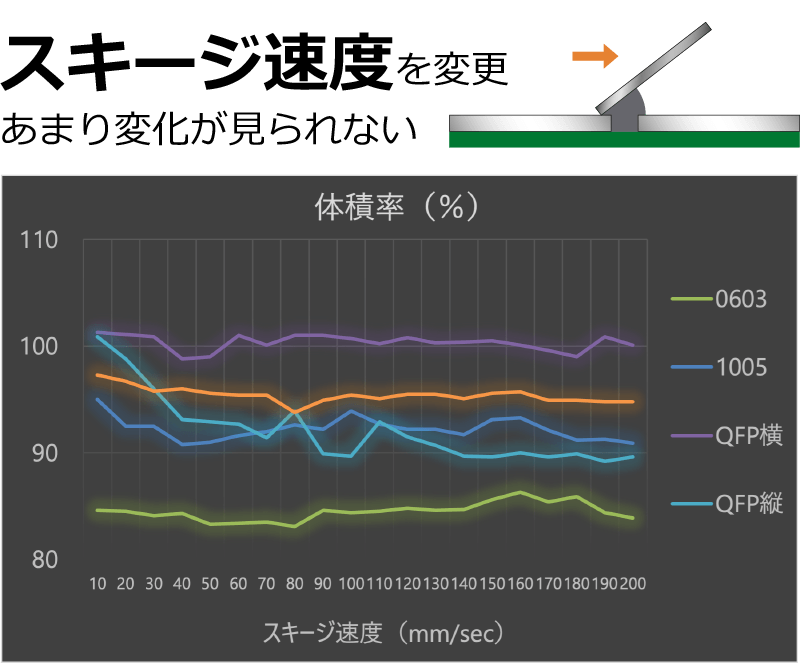
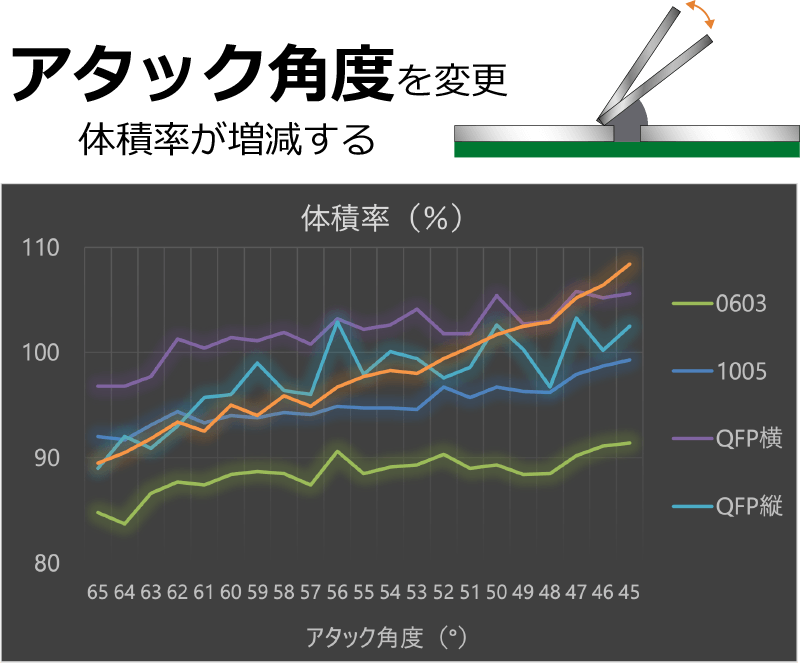
SPIと連携、自律制御による高精度印刷
SPIとの連携により、印刷情報をリアルタイムで印刷機へフィードバックします。
製造ロットによる生産基板の仕上がり精度の変化に追従し、自律的に高い印刷精度を維持できます。
印刷位置フィードバック:印刷位置が安定
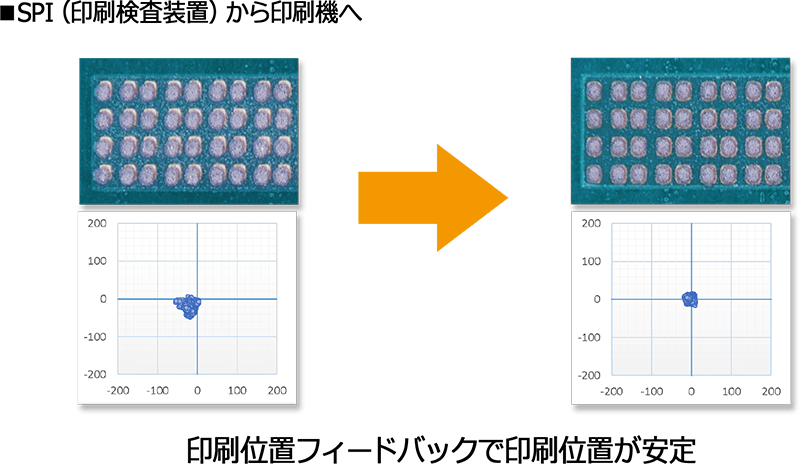
クリーニングフィードバック:ブリッジ発生を未然防止
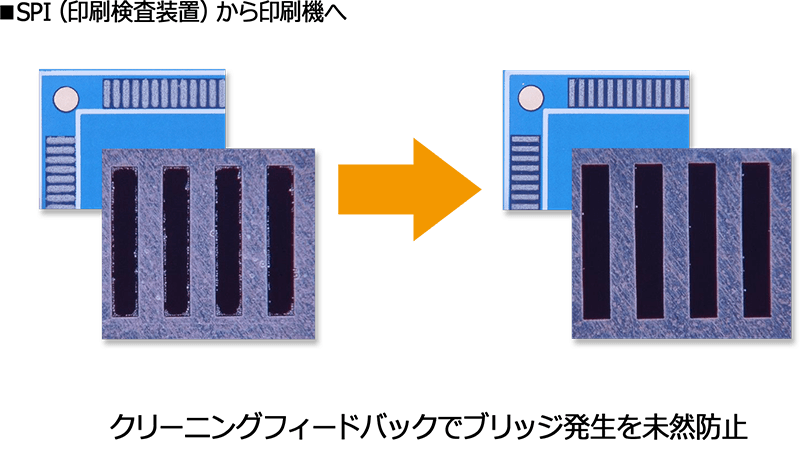
工法や周辺部材に関する豊富な知見
はんだ印刷を高品質に行うためには、はんだやメタルマスクなどの周辺部材の選択や設計なども重要です。
ヤマハでは、はんだやメタルマスクのメーカー各社と共同評価を行っており、豊富な知識と経験があります。個別の印刷セミナーなども承っており、お客様のお悩みごと解決のヒントとなるような情報をご提供します。
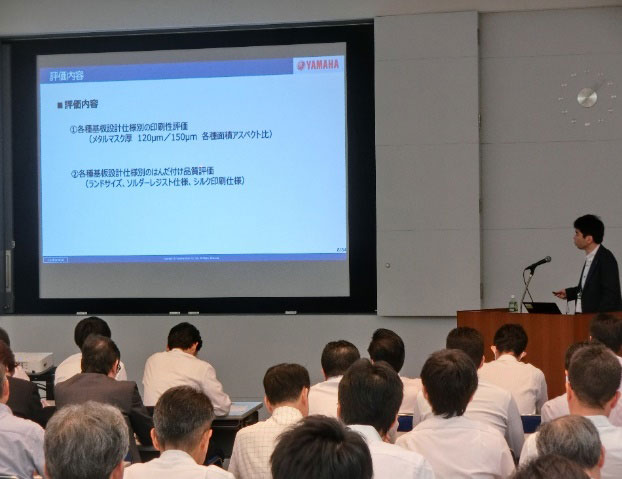

不良発生源の即時特定、正確かつ簡単な原因究明
不良が発生した際に、ラインを止めて原因を特定することは非常に時間がかかり、大きな生産ロスを生みます。
逆に、そのまま生産を継続すれば、大量の不良を発生させてしまいます。
検査機のラインナップを持つヤマハは、これらを解決するソリューションをご提供します。
リフロー前検査による不良の大量発生の抑制
より高い品質を求めて、リフロー前検査を導入するお客様が増えています。
リフロー前に検査することで、連続的な不良などもはんだが硬化する前に検出可能。
リフロー後での不良の大量発生を未然に防止します。
リフロー後検査時に文字がフラックスで消えて検出できない例
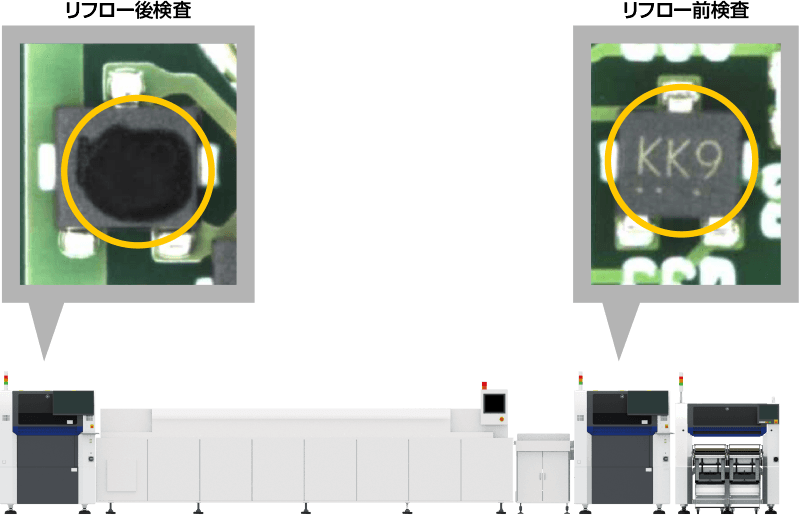
リフロー前で自動で不良を検出することで、初品チェックの自動化、修理作業工数の削減、廃棄ロスのコスト低減
リフロー前で極性検査、文字検査することで、検査機の過判定を低減し、直行率を改善
不良発生原因を特定することで、工程の不具合改善を促進し、工程内品質の向上を支援
検査機 - マウンタ連携による不良発生の抑制
不良発生時に、その不良の発生源である工程や原因を調査することは非常に面倒な作業です。
ヤマハではマウンターとAOIを連携させ、不良発生時に、発生したマウンターを即時停止します。不良の連続生産の防止と不良発生要因特定のサポートも行います。
QAオプション
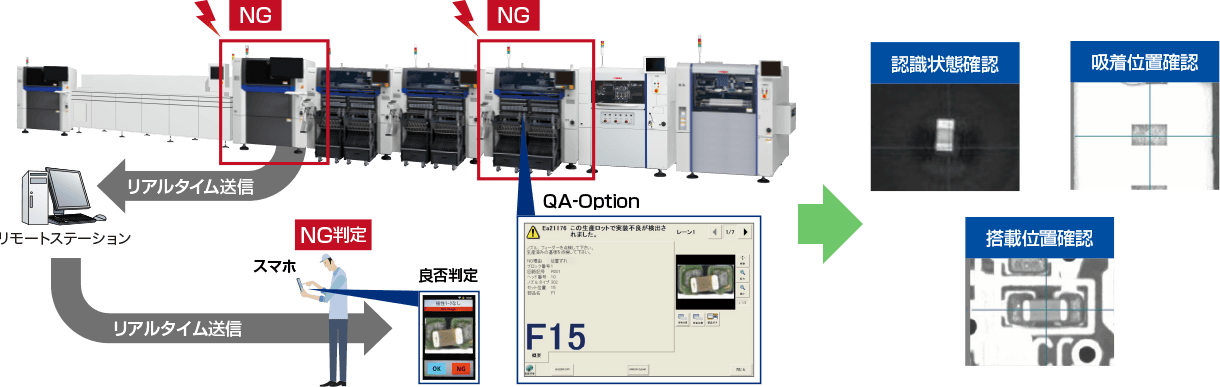
工程毎の画像照合による不良発生原因特定
リフロー後の基板で不良が発覚した場合、不良が発生した原因がどの工程であったのかを特定することは困難なため、改善活動に繋げることは困難でした。
1 STOP SMART SOLUTION では、すべての工程の画像を照合できるため、リフロー後であっても、どの工程から不良になったのかを特定し、改善を促進することができます。
N点照合
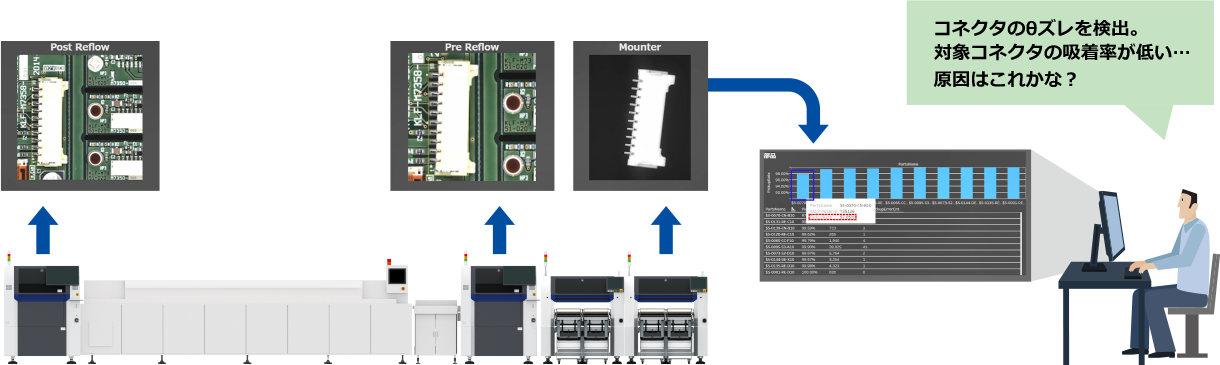
[不良発生原因特定事例]
部品に異物が付着
[原因]
はじめから部品に異物が付着していたことが原因。
[対策]
部品メーカーへフィードバック
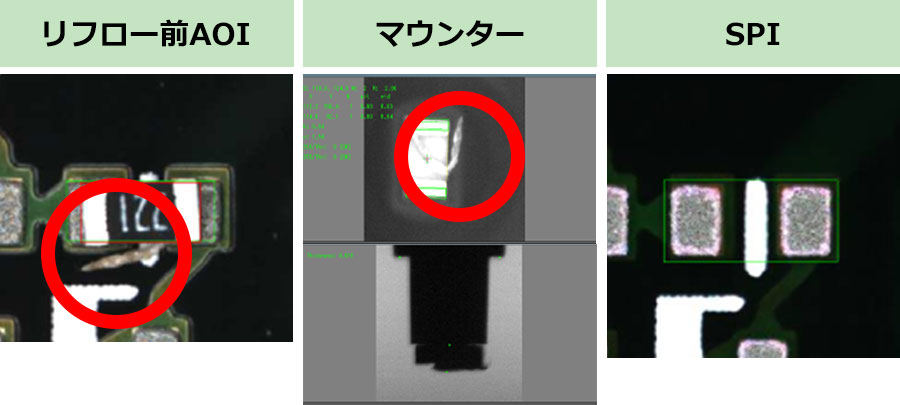
[不良発生原因特定事例]
部品の表裏反転が発生
[原因]
リールの切り替わり時に発生したことを特定。
スプライシング作業の失敗が原因。
[対策]
スプライシング作業の再指導
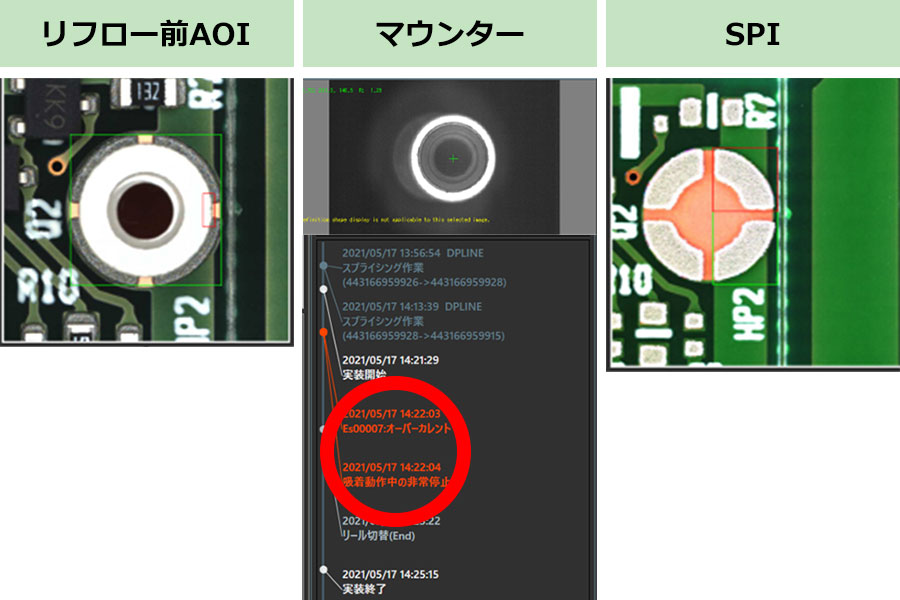