タクトタイム2秒短縮!
ラインの常識を覆した“リニアコンベア”の選択
電子機器組立メーカーA社 生産管理部
製品寿命が短いデバイス機器の製造現場では、フレキシブルな生産ラインが求められます。
A社でも、取引先からさらなる納期短縮を要求されていました。
課題
課題のポイント
- タクトタイムを2秒短縮したい
- 限られたスペースの中で生産性の高いライン設計が必要
「あと2秒短縮」には限界が・・・現場から聞こえるお手上げの声
スマートフォン・タブレット端末に搭載される電子部品の組立をしているA社では、タクトタイム短縮が最大の課題となっていました。市場投入台数も下降気味で、どのメーカーもいかに早く次期シーズンで展開するかを競っており、部品を供給するA社もその煽りを受けていました。
「メーカー側が求める納期を実現するためには、タクトタイムを2秒以上縮める必要がありました。しかし、現場からはこれ以上は厳しいのでは…という声も上がっていました」と担当のM氏は振り返ります。度重なる要求に応えるべく、生産工程の見直しはもちろん、ラインを増設し多品種生産にも対応してきた社内では"お手上げ"の空気が漂っていたのです。
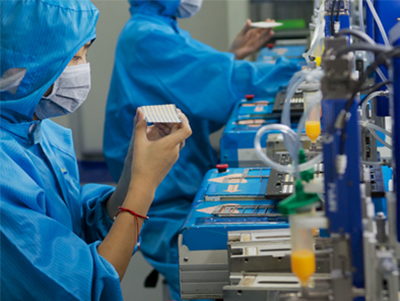
ターゲットは搬送工程。トレイの送り速度アップを検証するが、ロスを生む結果に
とはいえ諦めるわけにもいきません。M氏を中心に立ち上がったプロジェクトチームは、搬送工程の短縮に的を絞り、検証を始めました。
まずプロジェクトチームが考えた方法は、コンベアのトレイの送り速度でした。速度調整ができないため、ストッパ衝突時の衝撃が大きくなり、ワークずれやパレットの損傷などロスを出します。この調整によりラインを止めることとなり、さらに生産効率が落ちる、という悪循環が生じていたのです。
また、生産体制にも課題がありました。レイアウト変更やライン増設を繰り返し行った工場内では、さらなる増設のスペースがありません。また、段取り替えに工数がかかっており、小ロット生産の対応に適していませんでした。
「想定はしていましたが・・・それをはるかに上回るほど、タクトの短縮は難しいものでした」(M氏)
メンバーみな、解決策を見出せず途方に暮れていました。
解決
解決のポイント
- 搬送工程の改善でタクトタイム1.5秒短縮を実現
- 両方向に動作する自由なライン設計で省スペースに設置
両方向に動くスライダに見た、リニア駆動の可能性
M氏のチームが情報収集を行っていると、YouTube上でヤマハ発動機の『リニアコンベアモジュール LCM100』の動画を見つけました。
「とにかく驚いた、というのが最初の感想です」(M氏)
従来の搬送は一方向に流すだけですが、その動画では、スライダがコンベアの上を両方向に動いていたのです。A社は、詳しい話を聞くために、すぐに問合せました。
『LCM100』の最大の特徴は、高速かつ精密な動作ができる点でした。リニアモータ、スライダ、コントローラが1モジュールとなっていて、さらにスライダごとにサーボ制御することで、ストッパに衝突させず滑らかにピタッと止めることができました。これであれば、送り時間の短縮ができそうです。

テスト稼動でタクトタイム1.5秒短縮!2秒の壁は見えた
また、設置のしやすさも、中長期的な設備投資としてはメリットがありました。長さの変更はモジュールの増減のみで対応できるため、レイアウト変更もスムーズに行えます。余計な冶具が不要となるので自由にライン構築を行うことができ、これまでA社が苦手であった多品種・小ロット生産の対応も可能では、と考えたのです。A社は、導入を前提にテストすることを決めました。
テストにはヤマハ発動機側の技術協力もあり、スムーズに行うことができました。まずは、タクトタイムの目標値を6秒から4秒に設定して取り組んだところ、1.5秒の短縮に成功しました。M氏のチームは、次期シーズンで生産予定の製品用ラインで導入することを決めました。ヤマハ発動機のサポートのもと、さらなる改善を行っており、目標の2秒もまもなくです。
「まだ2秒は達成していませんが、メンバー全員、十分な手ごたえを感じています。メーカーからの要求にも応えられそうです」と、目標達成に向けチームの士気も高まっている、ということです。