製品をコストダウンするためラインあたりの生産数を増やしたい
生産量が約23%アップ!治具コストの削減も実現した方法とは?

お客様の課題
従来よりも生産能力をアップした装置が欲しい
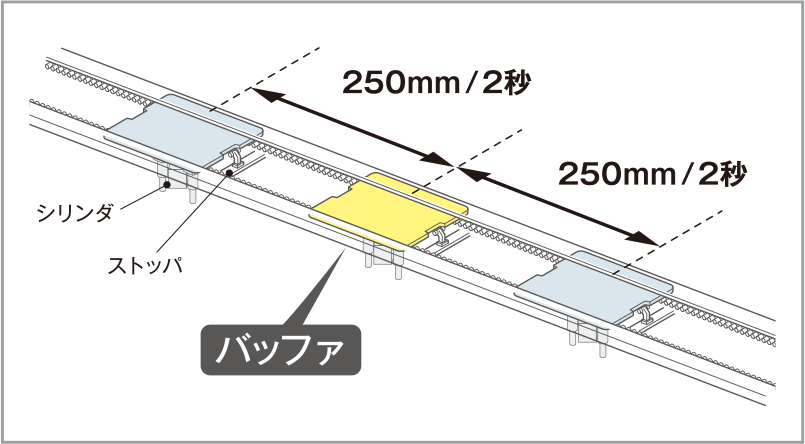
生産数アップの方法
- 生産ラインを増やす
- 加工時間の短縮
- 工程間搬送時間の高速化
- チョコ停削減による稼働率アップ
従来方式の自動化だと…
工程間の搬送時間が長く生産量を増やすのが難しい
- ストッパ + エアーシリンダによるバックアップで工程間の搬送に時間がかかる。
- 搬送時間を短くするために、工程間にバッファを設ける必要がある。
- シリンダや在荷確認などセンサが多く、チョコ停の原因になっている。
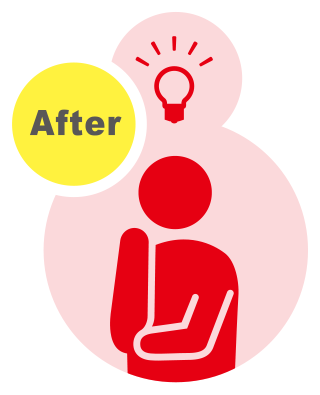
高速搬送&高精度位置決めのLCMで解決
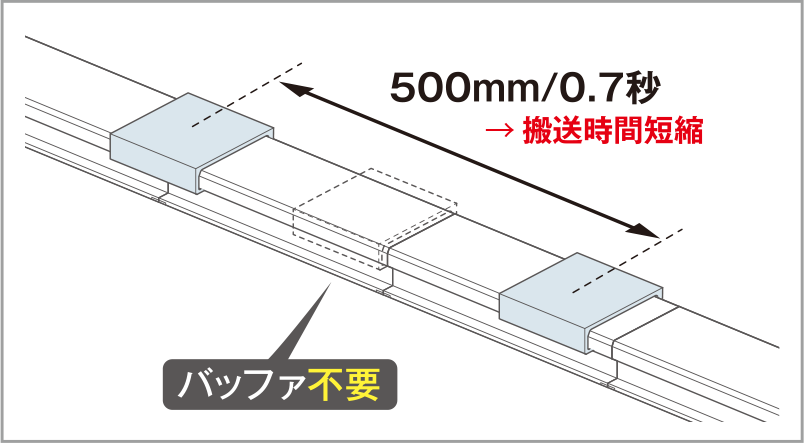
・繰り返し位置決め精度:±5μm(スライダ単体)
*動作時間は公差±0.005mmの場合です。公差を大きくすると動作時間が短くなります。
ヤマハのご提案内容
- 高速搬送による搬送時間の短縮
- 搬送時間短縮に伴いバッファが不要
- 単軸ロボット同様、数値による高精度位置決め
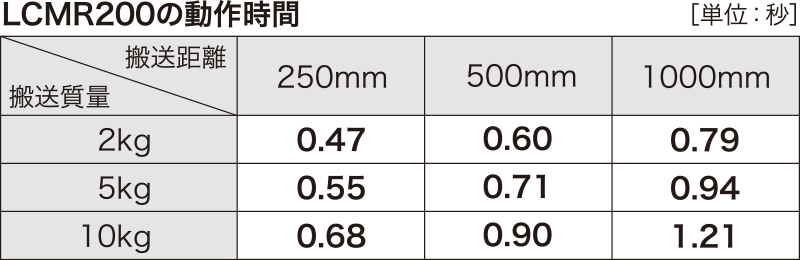
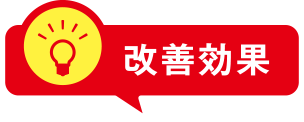
生産量が約23%アップ! 治具コストの削減も実現
<例> 1日8時間稼働、稼働率100%で試算した場合

生産量アップで製造コストを大幅に削減
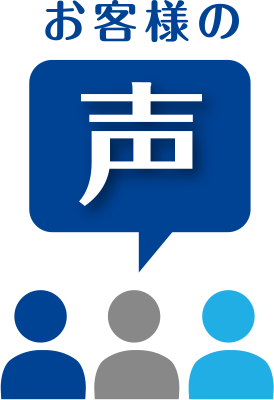
車載部品メーカー 製造技術担当
タクトアップだけでなく稼働率も大幅に改善し、計画以上に生産量が増加しました
これまでも生産量を上げるために、作業時間の短縮や稼働率アップを目的とした様々な改善を行ってきました。改善後それなりに効果はありましたが、作業時間を追い込んだことで搬送ミスなどのチョコ停が減らず、なかなか思ったように稼働率が上がらないというジレンマに悩まされてきました。
そんな中、展示会でヤマハさんのLCMを知り、『これなら生産量を上げられるのでは?』と思い、検討を開始しました。導入後の見込みを試算したところ充分な投資効果が期待できたため、LCMを使った生産ラインの製作を決定しました。
稼働後は搬送時間の短縮に加え、工程間の仕掛品の削減など予想通りの効果を得ることができました。さらに、搬送時間を充分に短縮できたため、無理にシリンダやロボットの速度を追い込む必要が無くなりました。その結果、搬送ミスなどのチョコ停も減り、社内でも非常に評価の高い生産ラインになりました。
LCMのおかげで当社の生産ラインは稼働率が大幅に改善され、当初の期待以上に生産を増やすことができました。担当者として、導入して本当に良かったと実感してます。
LCMの機能説明&メリット〈従来方式との比較〉
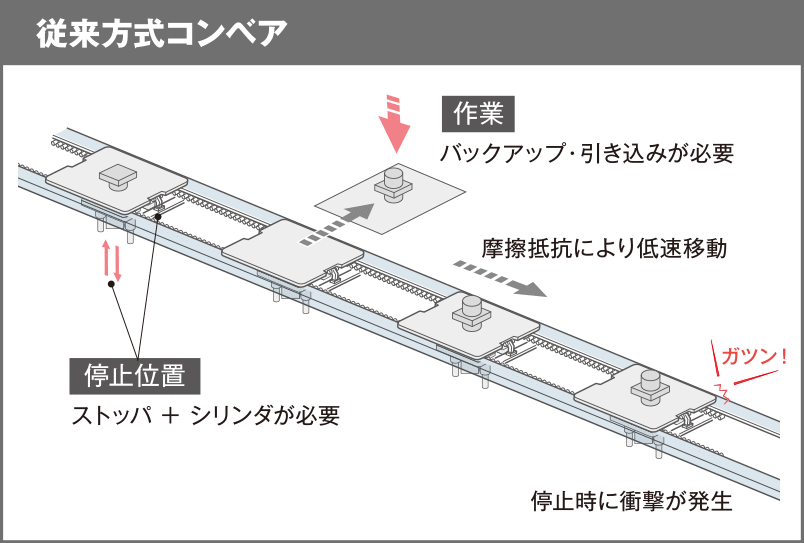

複数のシリンダを制御するために、各々シリンダセンサや電磁弁を制御する必要があります。
これに伴い、配線・ソフト開発・メカ調整などの工数が発生するため、立上げにも時間が必要です。
また構成部品が複数あることで、チョコ停の原因にもなります。
これに伴い、配線・ソフト開発・メカ調整などの工数が発生するため、立上げにも時間が必要です。
また構成部品が複数あることで、チョコ停の原因にもなります。
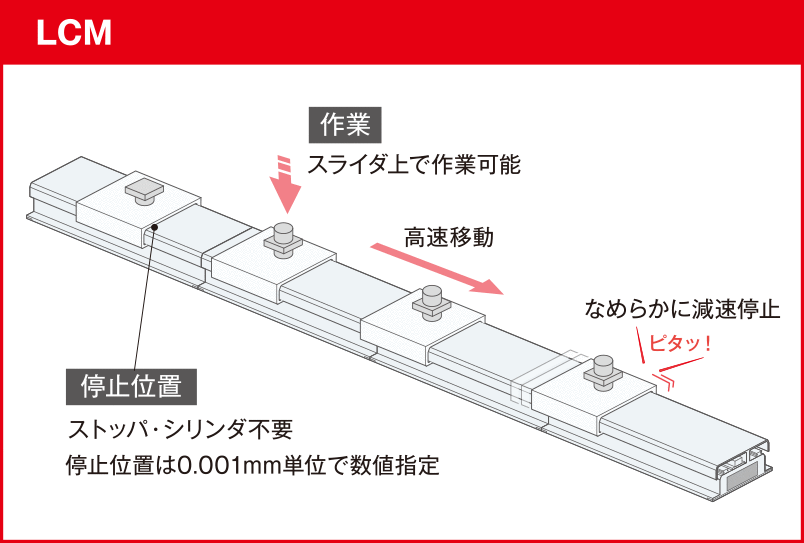

モジュールの構造はモータにセンサとシンプルな構造で設置も容易です。
配線工数、メカ調整工数は格段に楽になり、やりとりをするセンサ数が減るため、ソフト開発工数も削減でき、これにより、チョコ停の改善にも役立ちます。
配線工数、メカ調整工数は格段に楽になり、やりとりをするセンサ数が減るため、ソフト開発工数も削減でき、これにより、チョコ停の改善にも役立ちます。