多品種少量製品を稼働率下げずに生産したい
段取り替え時間をほぼゼロにできた理由とは?

お客様の課題
段取り替えによるロスタイムを減らし、装置の稼働率をアップしたい
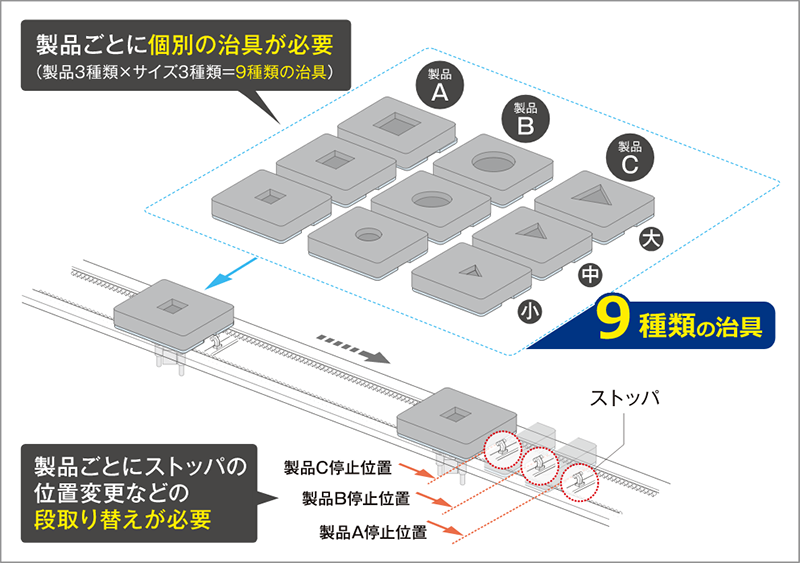
稼働率を上げるための方法
- 同一品種をできるだけまとめて生産する
- 段取り替え作業をできるだけ簡略化して作業時間を短くする
- 作業ノウハウの蓄積とマニュアル化して効率化する
従来方式の自動化だと…
稼働率をアップさせるのは難しい
- 製品ごとにストッパの位置変更などの段取り替えが必要
- 製品ごとに個別の治具が必要
- 段取り替えに伴う作業ミスの発生リスクはなくならない
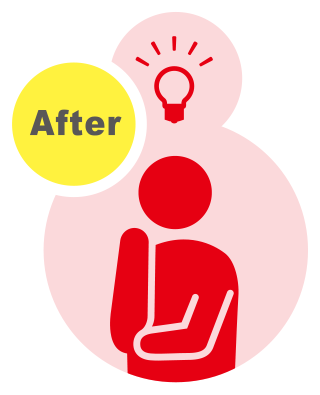
段取り替え時間ほぼゼロに!
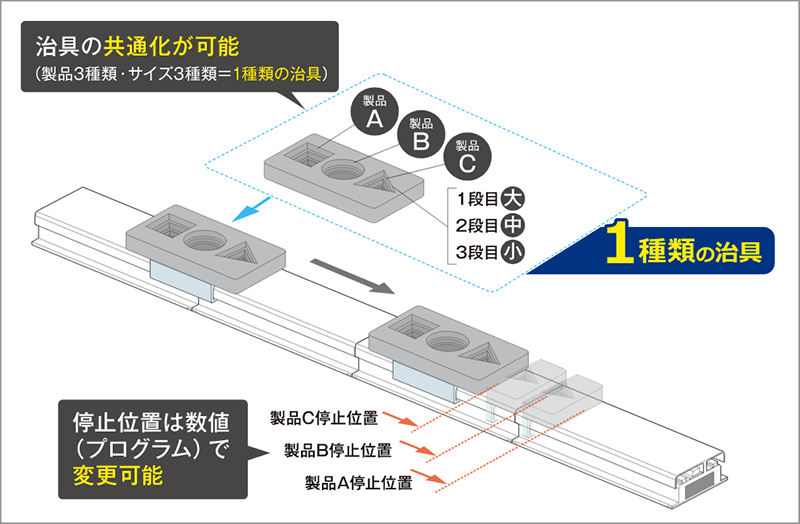
ヤマハのご提案内容
リニアコンベアモジュール(LCMR200 / LCM100)のご提案
- 停止位置をプログラムで自由に設定・変更
- 段取り替え作業不要
- 治具の共通化が可能(製作コスト・管理コスト削減)
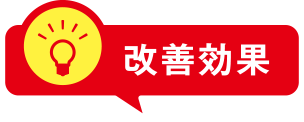
1か月に16時間(2日分)の段取り時間削減!
<例> 段取り替えにかかる時間 (工場の稼働時間:8時間/日、20日稼働とした場合)

LCMを使った段取り替え作業の改善とQRコード読み込みで完全自動化へ
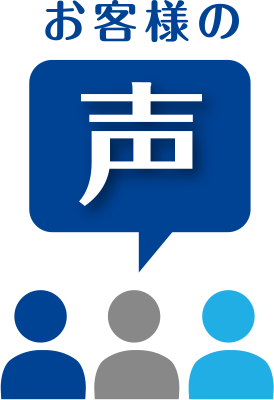
小型モータメーカー 装置設計者
長年の課題であった「段取り替えゼロ」を実現
今までも当社では多品種生産を効率よく稼働させるために、品種切り替え作業の改善に力を注いできました。その甲斐あって、作業時間を10分から5分へと50%短縮させることができ、お客様が工場見学される際には、その改善効果をご紹介してきました。
しかし作業時間を短縮できたとはいえ、5分の作業が1日に何回も発生するのは効率的とは言えず、稼働率を下げないために、生産数の多い品種を優先してある程度まとめて生産するなどの工夫を行う必要がありました。
今回ヤマハ発動機のLCMを検討したのは、さらなる稼働率アップを実現したいという期待からです。
LCMは、プログラムで停止位置を変更できるため「段取り替え作業なし」を実現し、期待通りの効果が得られました。さらに次の装置もLCMを採用し、その装置では投入側で製品のQRコードを読み取る仕組みも取り入れ、タッチパネルからの操作をやめました。それにより、完全自動化を実現することができています。稼働率が格段に上がり、品種切り替えの必要がないことで、今では小ロットの受注も気にならなくなりました。
LCMの機能説明&メリット〈従来方式との比較〉
停止位置を変更する場合
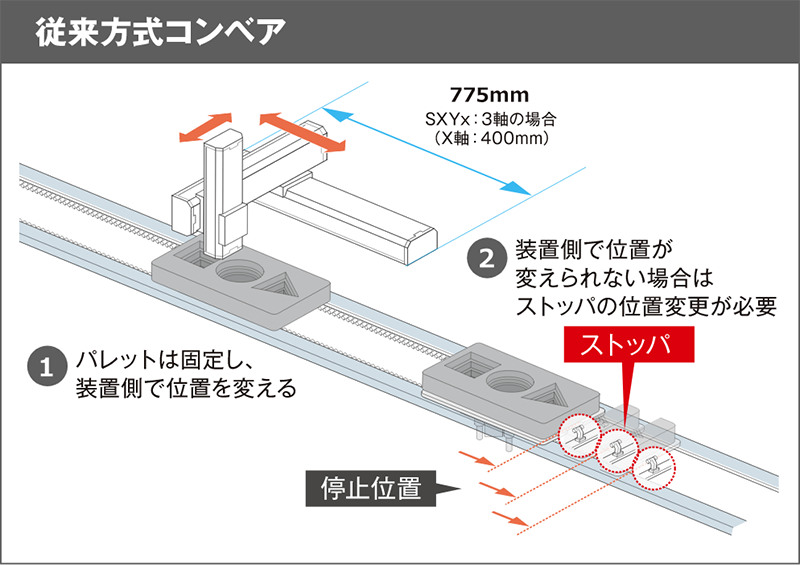

- 1.
- 作業位置を変更させるための3軸ロボットが必要で装置サイズが大きくなる。
- 2.
- ストッパの位置変更作業が発生し工数がかかる。
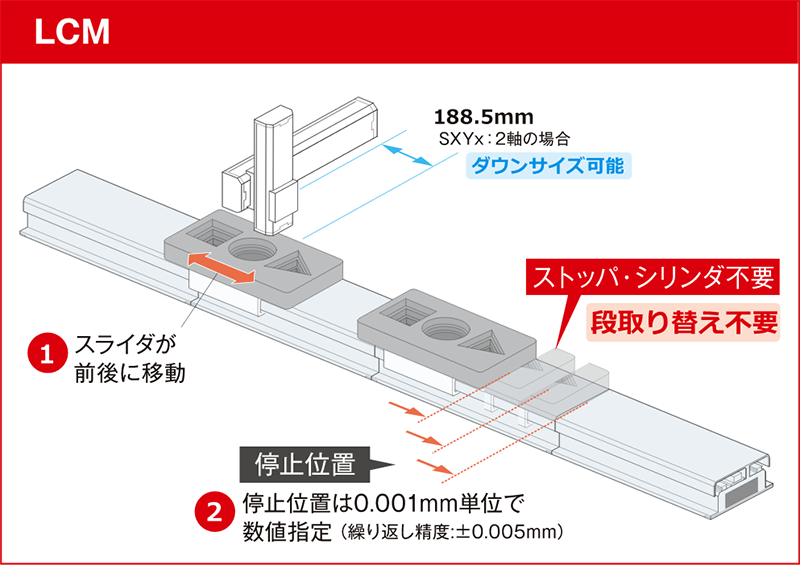

- 1.
- 作業位置を変更させるためのロボットも1軸分はLCMが担うため2軸ロボットでOK。装置のダウンサイジングが図れる。
- 2.
- 停止位置を自由に数値設定可能。