頻繁にチョコ停が発生し、設備に人が張り付いてしまう
チョコ停要因となっていた駆動機器や、センサーを必要最低限に。シンプル構造だからできるチョコ停対策。

お客様の課題
チョコ停が発生することで稼働率が下がってしまう
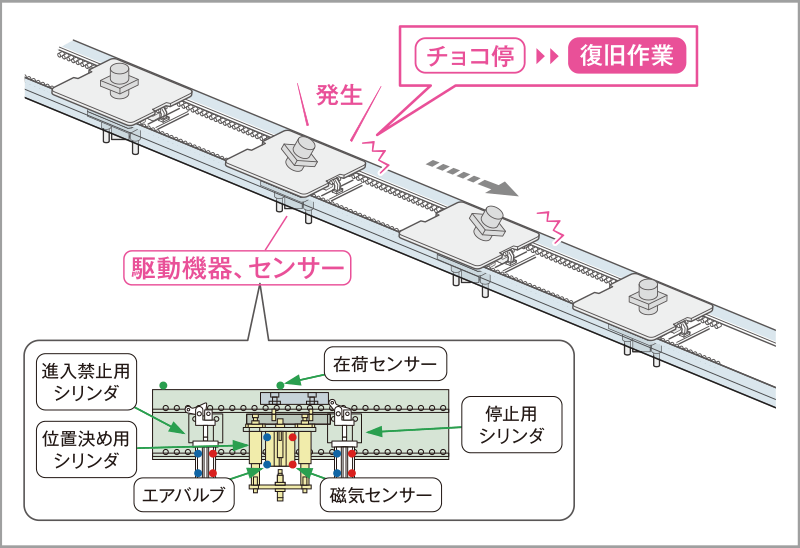
課題補足
- チョコ停が与える悪影響
① 納期遅延
② 対応工数のムダ
③ 品質の低下
④ 残業による原価アップ
従来方式の自動化だと…
駆動機器やそれに付随したセンサーが多く、
設備が止まり易い
- 停止するために複数の駆動機器が必要
- 駆動機器制御用のセンサーが必要
- いずれかが不具合発生したらチョコ停発生
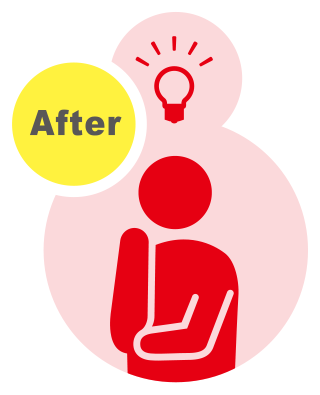
チョコ停要因となっていた駆動機器や、センサーを
必要最低限に。シンプル構造だからできるチョコ停対策。
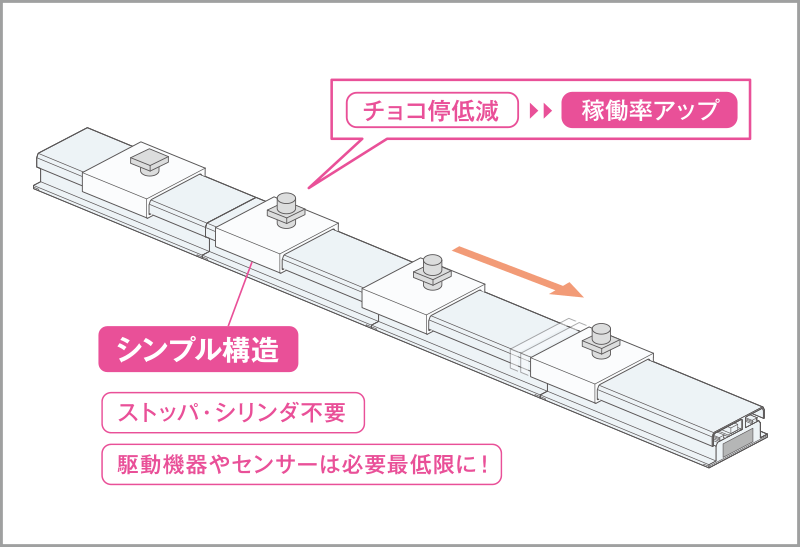
ヤマハのご提案内容
- 停止するために必要だった駆動機器を最低限に
- 駆動機器制御用のセンサーが不要に
- 在荷センサーなど必要最低限に
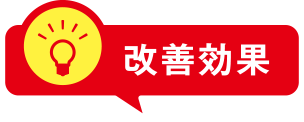
チョコ停が減る + 段取り替えが減ることで生産効率がアップ!
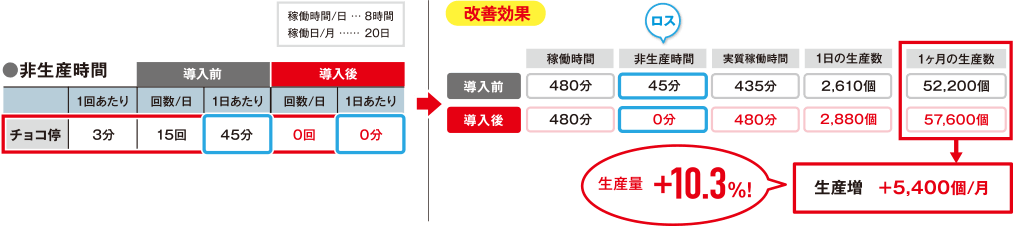
チョコ停の大幅削減で稼働率が向上し、安定生産を実現
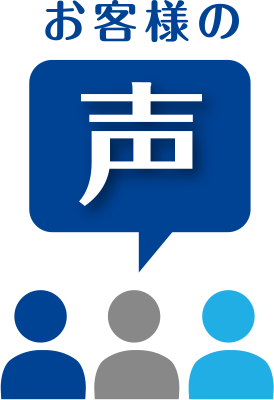
電子部品メーカー 生産技術担当者
搬送要因のチョコ停が圧倒的に減って、生産量も品質も安定したものづくりができるようになりました。
当社は自動車に搭載される電子部品を製造するメーカーで、24時間稼働で生産をしています。
そんな当社の悩みの種が『チョコ停』でした。チョコ停発生時はすぐ復旧させる必要があります。リセットしたらなぜか復旧するという時もありますが、簡単に復旧したから良いというわけではなく、設備が止まってしまった分をどこで挽回するかは、毎月末の悩みの種でした。
特に近年は夜勤帯の人員のやりくりも大変で、ちょっとした不具合でも、復旧まで時間が掛かってしまうケースや、頻繁に発生するチョコ停が原因で少ない作業員が設備に張り付いてしまうこともありました。
そのため、新規設備検討時には安定稼働をテーマのひとつに挙げました。まずチョコ停の要因分析をした結果、当社では搬送要因のチョコ停が圧倒的に多いことが分かったため、搬送部を中心に見直すことにしました。
いろいろなサイトや展示会で情報集めをしたところ、リニアコンベアモジュールに興味をもったのがきっかけです。
実機を見学したところ、搬送周りの駆動機器やセンサーが必要最低限に減っており、「導入したお客様からは、チョコ停が減った!とのことでご満足いただいてます」というお話も伺うことができました。
ヤマハさんに社内で紹介をしてもらった結果、社内でも高評価で、さらにSIerさんも紹介してもらい無事に導入にまでいたりました。
現在は目論見通り、搬送要因のチョコ停が圧倒的に減少し、安定生産ができるようになりました。メンテナンスの時間も従来の半分以下になり現場としても大変助かってます。これからも安定生産で高品質なものづくりを続けていきたいと思います。
LCMの機能説明&メリット
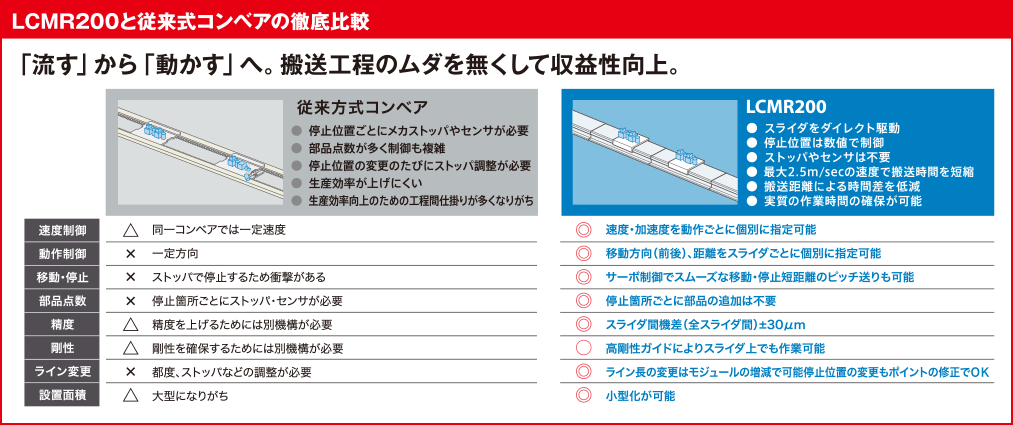