導入事例
お客様の課題を解決した導入事例をご紹介します。課題解決のヒントが見つかります。
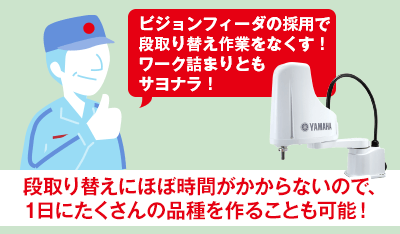
- ビジョンフィーダの採用で段取り替え作業をなくす!ワーク詰まりともサヨナラ!
-
ワーク供給の段取り替えをラクにしたい
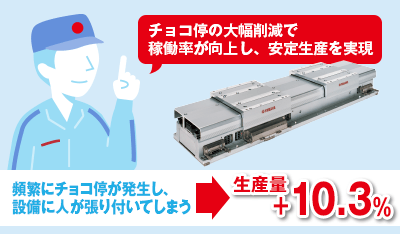
- チョコ停要因となっていた駆動機器や、センサーを必要最低限に。
-
頻繁にチョコ停が発生し、設備に人が張り付いてしまう
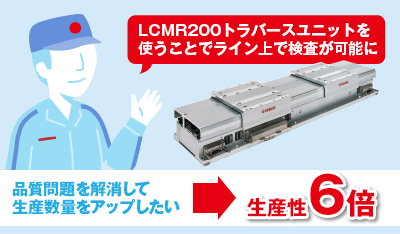
- LCMR200トラバースユニットを使うことでライン上で検査が可能に
-
生産効率を上げて生産量を増やしたい
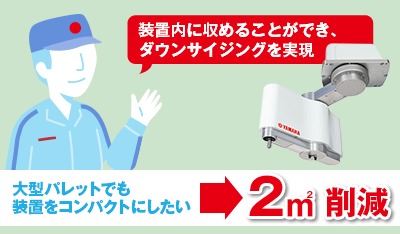
- 装置内に収めることができ、ダウンサイジングを実現
-
大型パレットでも装置をコンパクトにしたい
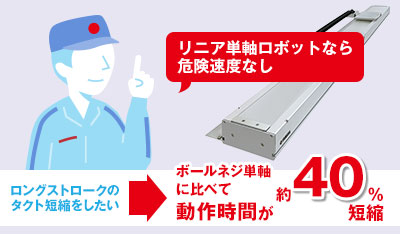
- ロングストロークでもタクトタイム短縮
-
単軸ロボットでロングストローク搬送がしたい
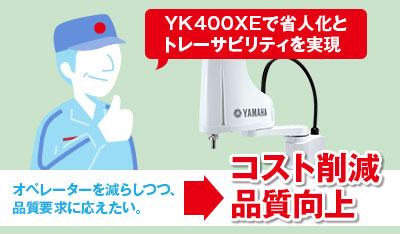
- 目に見えないコストが下がり、品質も向上!
-
省人化を図りつつ、品質のよい製品を安定生産したい
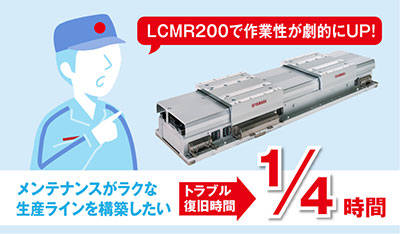
- トラブル復旧にかかる時間が1/4に!
-
メンテナンスがラクな生産ラインを構築したい
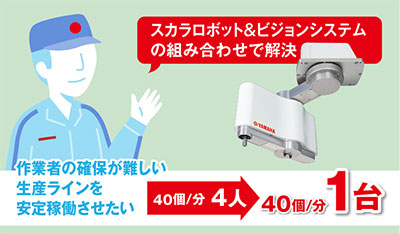
- 4人の作業者が0人に!
-
厳しい環境下の生産ラインを安定稼働させたい
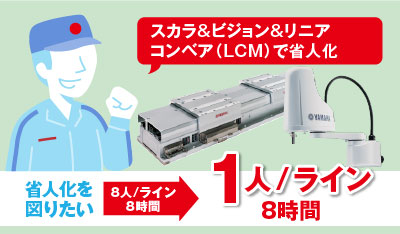
- 従来8人必要だった工程が1人に!
-
焼き菓子の箱詰めをする作業者を減らしたい
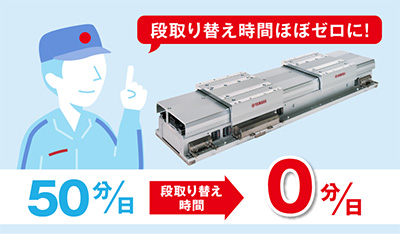
- 段取り替え時間ほぼゼロに!
-
多品種少量生産を稼働率下げずに生産したい
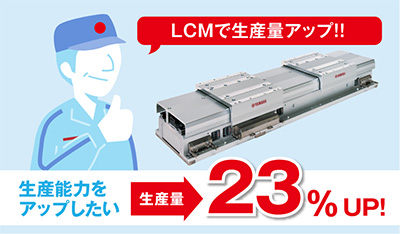
- 生産量約23%アップ
-
製品のコストダウンをするためラインあたりの生産数を増やしたい!
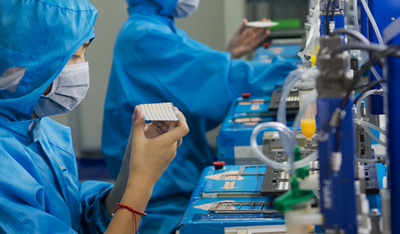
- タクトタイム2秒短縮!
-
ラインの常識を覆した"リニアコンベア"の選択
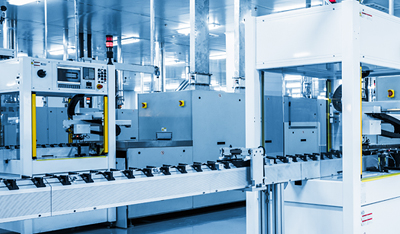
- 狭小幅"500mm"への挑戦
-
複数工程を狭小スペースで実現した方法とは
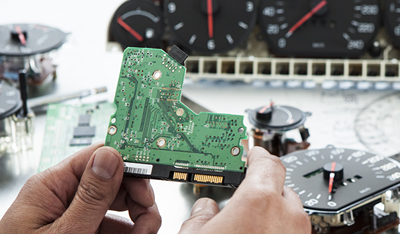
- セットアップ時間80%短縮
-
ロボットビジョンシステムを驚きの短時間で構築できたわけ
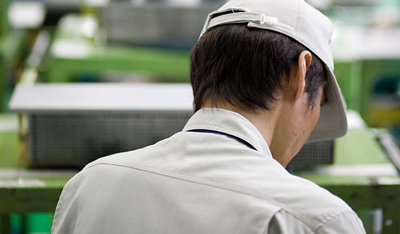
- 装置の立ち上げ時間が半分!
-
インデックステーブルからの置き換えに新発想
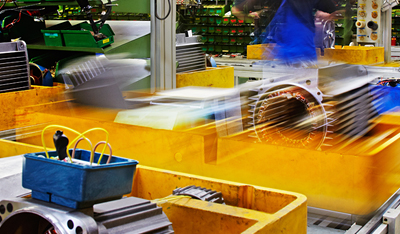
- 塗布の精度もスピードアップもどちらも譲れない
-
生産性向上のためにシーリング工程がすべき選択とは